If highly hazardous chemicals are not properly controlled there is the potential for an accidental release that could be disastrous. Process Safety Management (PSM) is a set of rules to keep employees, the facility, the community, and the environment safe from chemical accidents.
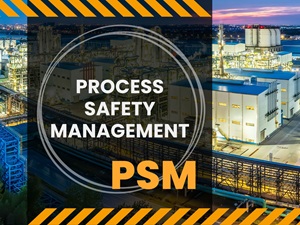
By integrating technologies, procedures, and management practices, Process Safety Management (PSM) aims to prevent the release of hazardous chemicals.
Employees play a crucial role in ensuring the safe handling of hazardous chemicals and processes. Active participation and awareness is essential to the PSM program's success.
OSHA Standard 1910.119 This section contains requirements for preventing or minimizing the consequences of catastrophic releases of toxic, reactive, flammable, or explosive chemicals. These releases may result in toxic, fire or explosion hazards.
OSHA’s PSM Standard 1910.119 applies to both General Industry and Construction.
The essential elements of PSM include:
- Hazard identification and risk assessment
- Safe operating procedures
- Emergency planning and response
- Mechanical integrity of equipment
- Employee training and involvement
OSHA’s Process Safety Management (PSM) standard applies mainly to manufacturing industries–particularly those pertaining to chemicals, transportation equipment, and fabricated metal products.
Other affected sectors include those involved with natural gas liquids, farm product warehousing, wholesale trade, as well as food processing, electric, gas, and sanitary services.
The standard also applies to pyrotechnics and explosives manufacturers and has special provisions for contractors working in covered facilities.
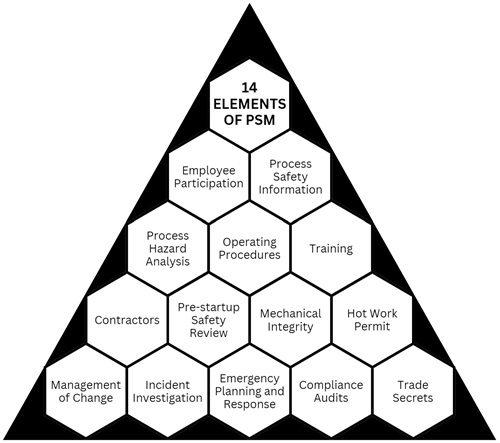
Process Safety Management (PSM) is critically important to businesses with highly hazardous chemicals and helps to ensure that the facility and the people working there are safe from hazards like large chemical spills, toxic gas releases, runaway chemical reactions, fires, and explosions.
Unexpected releases of highly hazardous chemicals including toxic, reactive, or flammable liquids and gases from processes have been reported for many years.
Incidents continue to occur in various industries that use highly hazardous chemicals that may be toxic, reactive, flammable, or explosive, or may exhibit a combination of these properties.
Regardless of the industry using these highly hazardous chemicals, there is a potential for an accidental release any time they are not properly controlled. An accidental release of highly hazardous chemicals creates the possibility of a catastrophic disaster.
OSHA Standard 1910.119(c)(2) Employers shall consult with employees and their representatives on the conduct and development of process hazards analyses and on the development of the other elements of process safety management in this standard.
All potentially affected employees should know:
- the hazards related to storing, mixing, or processing chemicals
- how each of their processes work
- when equipment is operating improperly or outside safe limits
- how to respond and who to contact if equipment is not operating properly
- how to respond and who to contact if there is an emergency
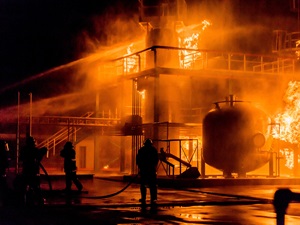
PROCESS HAZARD ANALYSIS
Hazardous chemical releases pose a significant threat. A key provision of Process Safety Management (PSM) is a Process Hazard Analysis (PHA), which is a careful review of what could go wrong.
The PHA analyzes the hazards of the process including potential causes and consequences of fires, explosions, and releases of toxic or flammable chemicals.
Safeguards must then be put in place which may include inherently safer or passive approaches to hazard control, new engineering controls, or administrative controls.
Engineering controls may include things like improved fire detection and suppression systems. Administrative controls will include items like new operating procedures, inventory control measures, or separation of highly hazardous chemicals into different storage areas.
OSHA Standard 1910.119(e)(1) The process hazard analysis shall be appropriate to the complexity of the process and shall identify, evaluate, and control the hazards involved in the process.
The PSM standard also requires:
- written operating procedures and written procedures for managing change
- employee training and participation, as well as contractor requirements
- pre-startup safety reviews and evaluation of the mechanical integrity of equipment
- a permit system for hot work
- investigation of incidents or near-misses involving releases of covered chemicals
- emergency action plans
- compliance audits at least every 3 years
To learn more about Process Safety Management visit OSHA's website at osha.gov/process-safety-management.
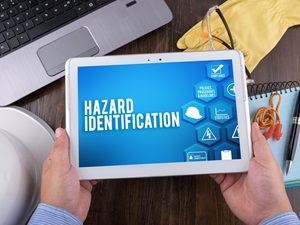
EMPLOYEES’ ROLE IN PROCESS SAFETY
Process safety is a team effort, and employees are critical to the success of the program.
Identifying Safety Hazards
As the first line of defense in identifying potential safety hazards, employees play a vital role by staying vigilant and observing their surroundings. One of their key responsibilities is to identify changes in equipment, chemicals, or procedures that could introduce new risks. Employees are often the first to spot warning signs, such as unusual odors, leaks, strange noises, or malfunctions, which may indicate an issue with hazardous chemicals. Understanding chemical properties like flammability, reactivity, and toxicity enables employees to recognize when chemicals are being mishandled or stored improperly. Using their knowledge from training, employees are equipped to identify and assess any deviations from normal operating conditions that might lead to unsafe situations.
Following Safety Procedures
Adhering to safety procedures is essential for preventing accidents and ensuring smooth operations. Employees are expected to strictly follow written operating procedures, whether during startup, normal operations, shutdowns, or emergencies. Proper use of personal protective equipment (PPE) is important and employees must ensure their PPE is in good working order and fits properly when handling hazardous chemicals. In addition, employees need to understand the limits of equipment and processes, ensuring they never exceed safe operating thresholds. By participating in ongoing training, employees stay informed about any changes to processes, safety measures, or equipment, further contributing to overall safety.
Reporting Unsafe Conditions
Maintaining a safe workplace depends heavily on employees' ability to recognize and report unsafe conditions promptly. Employees must report malfunctioning equipment immediately, especially when it involves chemical processing equipment like pumps, valves, or storage tanks. Notifying supervisors of chemical spills, leaks, or improper storage helps address potential hazards before they escalate. Identifying and reporting near misses is crucial, as these situations provide valuable learning opportunities for future incident prevention. Open communication about unsafe behaviors observed among colleagues, such as ignoring safety protocols or misusing equipment, is also encouraged and should be done without fear of retaliation.
Safety Preparedness Training
Effectively responding to incidents and minimizing their impact depends on employees actively engaging in safety preparedness activities. Participation in regular emergency training drills, such as those for evacuations, fires, and spill responses, helps employees stay prepared for emergencies. Employees must know the location of essential safety equipment, including fire extinguishers, emergency shutoff systems, eye wash stations, and first aid kits. Understanding emergency procedures, such as facility evacuation routes, assembly points, and how to assist others during an emergency, is critical. Familiarity with the company’s emergency action plan, which outlines responses to incidents like chemical spills, explosions, or toxic gas releases, ensures that employees can contribute to an orderly and safe response. By staying calm and following instructions during emergencies, employees help maintain safety and prevent further harm.
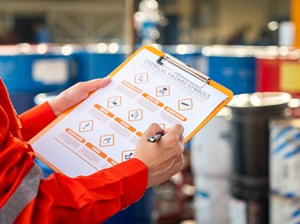