Do your employees know what to do if there is an emergency at your workplace? Does the staff know when to evacuate and when to shelter-in-place? If the answer is no, why not? Learn why Emergency Action Plans are essential.
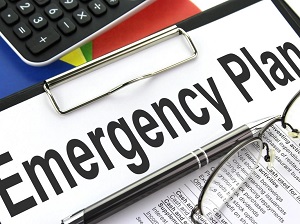
Workplace emergencies can happen at any company and may have the potential for severe injury to workers and even extreme property damages. Emergency Action Plans provide procedures in a workplace so workers know what is expected and what to do in the event of an emergency.
According to OSHA, the purpose of an Emergency Action Plan (or EAP for short) is to facilitate and organize employer and employee actions during workplace emergencies.
The goal with any EAP is to prevent employee injuries and structural damage to the facility during emergencies.
OSHA Standard 1910.38(b) Written and oral emergency action plans. An emergency action plan must be in writing, kept in the workplace, and available to employees for review. However, an employer with 10 or fewer employees may communicate the plan orally to employees.
In the event of an emergency all personnel must know to do or be aware of:
- how to report any emergency situation
- the procedure for emergency evacuation, including the type of evacuation and exit route assignments
- what does the alarm system look or sound like to alert workers of emergencies
- designated employees that may be required stay behind to continue critical plant operations
- how to account for all employees after evacuation
- procedures for employees performing rescue or medical duties
- name or job title of employees to contact for plan information
Examples of potential workplace emergencies that all staff must be prepared for include:
- Fires and Explosions
- Tornadoes
- Earthquakes
- Chemical Spills
- Bomb or Terrorism Threats
- Active Shooter
The most common type of emergency in a workplace is fire.
OSHA Standard 1910.37(a)(3) Exit routes must be free and unobstructed. No materials or equipment may be placed, either permanently or temporarily, within the exit route. The exit access must not go through a room that can be locked, such as a bathroom, to reach an exit or exit discharge, nor may it lead into a dead-end corridor. Stairs or a ramp must be provided where the exit route is not substantially level.
OSHA defines an exit route as a continuous and unobstructed path of exit travel from any point within a workplace to a place of safety. An exit route consists of three parts:
- Exit access – Designated walkways to the exit that are permanent
- Exit – Openings to allow access for exit, most likely doors
- Exit discharge – After the exit, a path that leads directly to another location away from the location of the potential emergency, typically a designated area outside
- Exit signs must be clearly visible and emergency exits must not be blocked.
- Evacuation maps should be posted in the workplace.
- Assembly points at the exit discharge should be identified ahead of time and known by the employees.
- Workers should report immediately to the designated assembly area upon evacuation.
- No one should go home or to an offsite location other than assembly area during an emergency evacuation.
OSHA Standard 1910.38(e) Training. An employer must designate and train employees to assist in a safe and orderly evacuation of other employees.
Workers should be trained on the EAP:
- Initially upon hire
- If the plan changes
- If designated persons’ duties change
While most employees are familiar with fire and emergency drills that lead them to an outdoor assembly point, an EAP will also have shelter in place procedures for other types of emergencies.
When there is a chemical, biological, or radiological release into the environment in such quantity and/or proximity to a place of business, then it may be safer to remain indoors rather than to evacuate employees.
In the case of a tornado warning in the area, employees should proceed to the nearest tornado shelter or designated area inside the building, like an inner hallway.
If an earthquake occurs it is safer to remain indoors and brace against a sturdy frame rather than to quickly try to evacuate employees.
A designated person should survey the immediate area for unfamiliar objects if there is a bomb or terrorism threat. If a suspicious object is found, evacuate the area immediately.
While all employees should be trained on the Emergency Action Plan for the specific work location that they are currently working in, here are some important points all workers should remember.
- Everyone in the workplace should be aware of the Emergency Action Plan and familiarize themselves with the posted evacuation diagrams.
- All employees should know how to report an emergency situation.
- During any emergency drill, all employees should follow the evacuation procedure. No one stays behind!
- All employees must be aware of their role during any emergency situation. Most employees will follow evacuation or shelter-in-place safety procedures but some will have safety facilitator, medical rescue or critical operations roles.
- Emergency exits should be clearly labeled, lighted and visible at all times. Emergency exits should NEVER be blocked, even temporarily.
- Assembly points at the exit discharge should be identified ahead of time and known by the employees.
- Workers should report immediately to the designated assembly area upon evacuation.
- No one should go home or to an offsite location other than assembly area during an emergency evacuation.
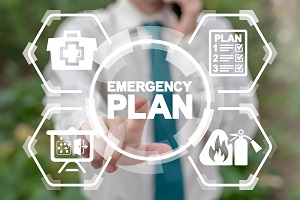