Personal protective equipment (PPE) is designed to protect workers from serious workplace injuries or illnesses resulting from contact with chemical, radiological, physical, electrical, mechanical, or other workplace hazards. In some cases, workers must shield most or all of their bodies against workplace hazards.
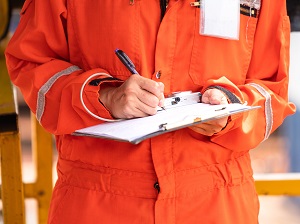
Employees who face possible bodily injury of any kind that cannot be eliminated through engineering, work practice, or administrative controls, must wear appropriate body protection while performing their jobs. Workplace hazards that could cause bodily injury include:
- Radiation or temperature extremes
- Exposure to blood, bodily fluids, or waste
- Hazards created by welding, cutting, or brazing operations
- Hot splashes from molten metals and scalding liquids
- Potential impacts from tools, machinery, and materials
- Exposure to hazardous chemicals or materials
OSHA Construction Standard 1926.95(a) and General Industry Standard 1910.132(a) Protective equipment, including PPE for eyes, face, head, and extremities, protective clothing, respiratory devices, and protective shields and barriers, shall be provided, used, and maintained in a sanitary and reliable condition wherever it is necessary by reason of hazards of processes or environment, chemical hazards, radiological hazards, or mechanical irritants encountered in a manner capable of causing injury or impairment in the function of any part of the body through absorption, inhalation or physical contact.
Besides face shields, safety glasses, hard hats, and safety shoes, protective equipment includes a variety of devices and garments such as goggles, coveralls, gloves, vests, earplugs, and respirators.
Materials used in whole-body personal protective equipment include fire-retardant wool or cotton, rubber, leather, synthetics, and plastic.
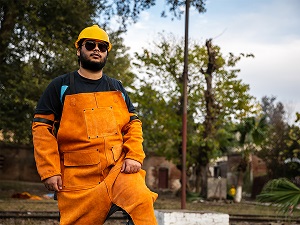
There are many varieties of protective clothing available for specific hazards. Workers must wear personal protective equipment for all parts of the body exposed to possible injury. Examples of body protection include laboratory coats, coveralls, vests, jackets, aprons, surgical gowns, leggings, shin guards, arm coverings, and full body suits.
If a hazard assessment indicates a need for full body protection against toxic substances or harmful physical agents, the clothing should be carefully inspected before each use, it must fit each employee properly, and it must function for the purpose for which it is intended.
Protective clothing comes in a variety of materials, each effective against particular hazards, such as:
- Paper-like fiber used for disposable suits provide protection against dust and splashes.
- Treated wool and cotton adapts well to changing temperatures, is comfortable, and fire-resistant and protects against dust, abrasions and rough and irritating surfaces.
- Duck is a closely woven cotton fabric that protects against cuts and bruises when handling heavy, sharp or rough materials.
- Leather is often used to protect against dry heat and flames.
- Rubber, rubberized fabrics, neoprene, and plastics protect against certain chemicals and physical hazards.
OSHA Standard 1926.441(a)(5) Face shields, aprons, and rubber gloves shall be provided for workers handling acids or batteries.
Workers who are required to wear personal protective equipment, including body protection, must be trained on how to do the following:
- Use protective equipment properly
- Be aware of when personal protective equipment is necessary
- Know what kind of protective equipment is necessary
- Understand the limitations of personal protective equipment in protecting workers from injury
- Put on, adjust, wear, and take off personal protective equipment
- Maintain protective equipment properly
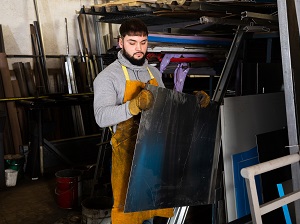
If workers face potential injury to hands and arms that cannot be eliminated through engineering and work practice controls, employers must ensure that employees wear appropriate protection. Protective equipment includes gloves, finger guards and arm coverings or elbow-length gloves.
Workers who face possible foot or leg injuries from falling or rolling objects or from crushing or penetrating materials should wear protective footwear. Employees whose work involves exposure to hot substances, or corrosive or poisonous materials must have protective gear to cover exposed body parts, including legs and feet.
Foot and leg protection choices include leggings made from leather, aluminized rayon, or other appropriate material can protect the lower legs and feet from heat hazards such as molten metal or welding sparks and combination foot and shin guards protect the lower legs and feet and may be used in combination with toe guards when greater protection is needed.
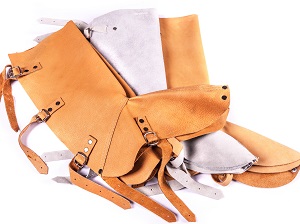
Welders must wear suitable personal protective equipment (PPE) to protect against hazards such as burns, sparks, spatter, electric shock, and radiation. For body protection, the American Welding Society (AWS) recommends that welders wear:
- oil-free protective clothing made of wool or heavy cotton
- long-sleeved shirts buttoned at the cuffs, pockets, and collar to protect arms and neck from radiation exposure and skin burns
- heavy, durable, long pants without cuffs that overlap the tops of boots
- aprons, leggings, capes, and sleeves as needed for the hazards associated with the welding task
OSHA Construction Standard 1926.353(d)(1)(iii) Welders and other employees who are exposed to radiation shall be suitably protected so that the skin is covered completely to prevent burns and other damage by ultraviolet rays.
If welders, or any other workers, are exposed to flash fires or short-duration flame exposures, OSHA expects that employers would provide and ensure the use of flame-resistant clothing (FRC) to protect workers from these hazards.
OSHA General Industry Standard 1910.252(b)(3) Employees exposed to the hazards created by welding, cutting, or brazing operations shall be protected by personal protective equipment. Appropriate protective clothing required for any welding operation will vary with the size, nature and location of the work to be performed.
Employees wearing FRC may be exposed to hazards related to heat stress, so it is important, when possible, to provide light weight breathable fabrics and allow employees to drink cold liquids, such as water and other electrolyte replenishing drinks.
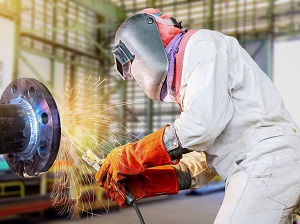
Workers who may be exposed to asbestos must be protected. Protective clothing, that may include coveralls or similar whole-body clothing, head coverings, gloves, and foot coverings, is required for employees exposed to asbestos above the time-weighted average (TWA) and/or excursion limit.
A competent person should examine employee worksuits at least once per work shift for rips or tears. Rips or tears found while an employee is working must be mended or the worksuit replaced immediately.
Laundering of contaminated clothing must not release airborne asbestos in excess of the permissible exposure limit (PEL). Contaminated clothing should be transported in sealed, impermeable bags or other closed impermeable containers with appropriate labels. Contaminated clothing must be removed in the decontamination area and must never be worn off site.
OSHA Construction Standard 1926.1101(i)(1) The employer shall provide or require the use of protective clothing, such as coveralls or similar whole-body clothing, head coverings, gloves, and foot coverings for any employee exposed to airborne concentrations of asbestos that exceed the time-weighted average (TWA) and/or excursion limit prescribed.
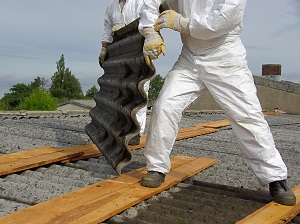
Workers who may be exposed to bloodborne pathogens or other potentially infectious materials (OPIM) must use personal protective equipment (PPE) that may include gloves, gowns, lab coats, face shields or masks, eye protection, and other protective gear.
The level and type of protection must match the expected exposure, so those employees who may encounter increased amounts of blood, OPIM, or splashes and sprays will need more protective clothing. Protection against exposure to the body is provided by protective clothing, such as gowns, aprons, lab coats, and similar garments.
OSHA General Industry Standard 1910.1030(d)(3)(xi) Appropriate protective clothing such as, but not limited to, gowns, aprons, lab coats, clinic jackets, or similar outer garments shall be worn in occupational exposure situations. The type and characteristics will depend upon the task and degree of exposure anticipated.
Workers exposed to blood or OPIM must remove personal protective equipment before leaving the work area. If a garment is penetrated by blood or OPIM, it must be removed immediately or as soon as feasible. Once PPE is removed, it must be placed in an appropriately designated area or container for storage, washing, decontamination, or disposal.
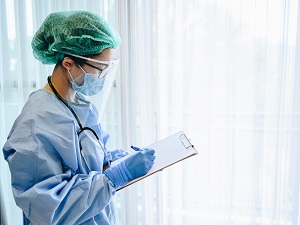