All workers need to be aware of the main safety hazards that might be found in a loading dock area including slip, trip and fall hazards, working safely with pallets and around pallet racking, and materials handling safety precautions.
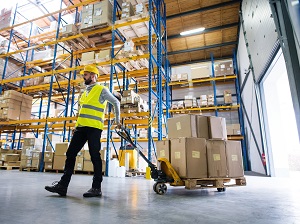
Loading docks are often high-traffic areas with workers, materials, equipment and a variety of hazards.
Loading dock areas may be occupied by forklifts, pallet jacks, or other heavy equipment and they can also be congested with materials and workers performing different types of tasks.
As a consequence, workers should be aware of loading dock hazards, including:
- Struck-by hazards
- Falls from heights/docks
- Slips and trips
- Protruding materials
- Falling objects
- Sharps hazards
- Heat stress/cold stress
- Caught-between equipment and materials
- Back injuries from lifting and other ergonomic issues
When workers are performing work on or near loading docks, it is important to follow safety guidelines to prevent injuries.
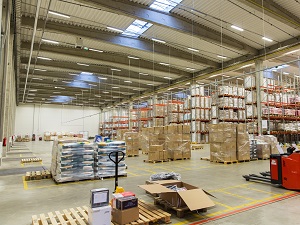
Slips, trips, and falls to the same level, falls from heights or falls off the dock edge are common causes of injuries at loading docks. Materials may accumulate in the loading dock area and there may be objects that obstruct or partially block walkways or aisles. Keep paths clear so pedestrians, visitors and workers can move freely.
All storage areas shall be kept free from the accumulation of materials that could be hazardous including trip, fire and pest hazards. When walkways are blocked by pallets or other materials it is important to stop and carefully push or carry the items out of the way. Never kick materials or empty pallets when attempting to clear a path.
OSHA Standard 1910.141(a)(3)(iii) To facilitate cleaning, every floor, working place, and passageway shall be kept free from protruding nails, splinters, loose boards, and unnecessary holes and openings.
- Walk, never run, while in a loading dock area.
- Practice good housekeeping.
- Keep floors and dock plates dry.
- Clean up spills of wet or dry material immediately.
- Report damaged floors so they can be repaired quickly.
Be aware of loading dock edges. Do not attempt to jump off or onto the loading dock. Always use the access steps and ladders provided.
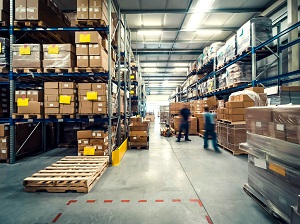
Steel storage racks or pallet racks are used to hold goods stacked on pallets. The two most common causes of racking failures are racking that is not installed properly and damaged racking that is not reported or not repaired quickly. Every piece or component of pallet racking must be installed according to the manufacturer’s requirements. Column or post guards help prevent impacts and protect uprights from damage that could result in catastrophic failures.
Inspect racks regularly to discover any damage, wear, or problems. Report any damage found on racks and ensure that repairs are made quickly. If necessary, unload racks, and then tag and mark or barricade them to remove them from service until repairs are completed.
OSHA Standard 1910.176(b) Secure storage. Storage of material shall not create a hazard. Bags, containers, bundles, etc., stored in tiers shall be stacked, blocked, interlocked and limited in height so that they are stable and secure against sliding or collapse.
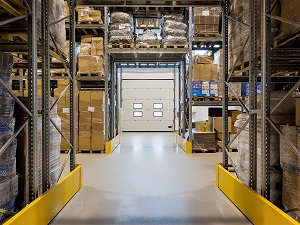
Wood pallets are most common type of pallet used but can be also be made of plastic or metal. When working with pallets, injuries can be caused by issues such as
- Using a damaged pallet
- Selecting the wrong sized pallet for racking
- Handling pallets with a forklift incorrectly
- Exceeding the maximum load for the pallet
Inspect pallets before use, specifically looking for loose or broken boards or stringers or protruding nails. Ensure any pallets in use are not damaged. It's important to know the safe load capacity of the pallets being used. Use pallets that are the correct size. Pallets that are too small for the rack may become a hazard. Wire mesh on racks may not be strong enough to support the full weight of smaller pallets.
Forks of the lift truck should enter the pallet straight and level to avoid damaging the pallet.
Stack empty pallets flat, not leaning up on their sides.
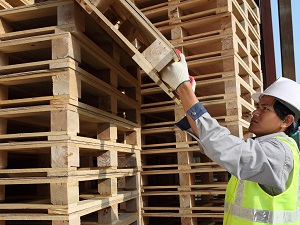
Wear PPE appropriate for the work tasks including:
- Gloves, when unpacking crates or handling materials to protect hands from lacerations
- Steel-Toed Boots, to protect feet when handling heavy loads that could fall
- Safety Glasses, when cutting banding, strapping or shrink wrap
- Hard Hats, to protect yourself from struck-by or falling object hazards
Use caution when manually handling material. When removing items from shelves or racks, remove one item at a time. If lifting is required to move a load, remember to bend at the knees, not at the waist. Stack heavier goods and materials that will be handled manually on the bottom or mid-level shelves to reduce strain on the back. It is every employee’s responsibility to practice proper lifting techniques while at work and to ask for help when needed.
Beware of laceration and puncture hazards when packing or unpacking crates or boxes. Watch for protrusions such as nails, screws, staples, splintering wood, broken boards, and metal banding or straps. Removing any sharp object that could cause injury is a priority when unpacking any crate. When cutting shrink wrap, boxes or other material, direct the blade away from your face and body. Do not use any cutting device near your eyes/face and ensure co-workers are a safe distance from the area where blades of any kind are being used.
Items that hang over the edge of the shelf into the walkway can pose a struck-by or falling object hazard.
Clean loading areas regularly.
If you are unsure of safety rules or operations, stop and ask for clarification. If you see a hazard either correct it or report it.
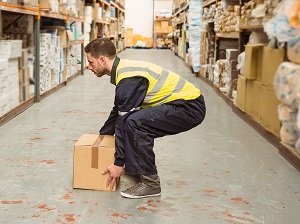