There are quite a few safety topics and precautions all warehouse workers need to be trained on include PPE, forklifts, housekeeping, materials handling, ladder safety, and fall hazards.
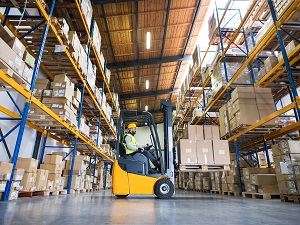
According to OSHA, the fatal injury rate for the warehousing industry is higher than the national average for all industries.
Potential hazards for warehouse workers include:
- Unsafe use of forklifts
- Improper stacking of products
- Failure to use proper personal protective equipment
- Failure to follow proper lockout/tagout procedures
- Inadequate fire safety provisions
- Repetitive motion injuries
Warehouse workers should know that if they are unsure about the safety rules or operations in the warehouse, they must stop and ask for clarification. If warehouse workers see a hazard they should either correct it or report it.
Warehouse workers should be wearing PPE appropriate for the work environment and their work tasks. Gloves are essential when unpacking crates or handling materials to protect hands from lacerations. Steel-toed boots will protect workers feet when they are tasked with handling heavier loads. Safety glasses are critical when workers are cutting banding, strapping, or shrink wrap from deliveries. Hard hats are usually required in warehouses to protect workers from struck-by and falling object hazards.
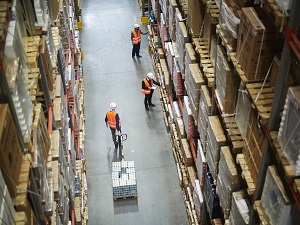
In the warehouse, forklift operators and workers nearby are at risk of hazards such as collisions, falls, tip-overs, and struck-by conditions. Every forklift operator must be trained and certified. No one under the age of 18 is allowed to operate a forklift.
OSHA Standard 1910.178(m)(3) and 1926.602(c)(1)(vii) Unauthorized personnel shall not be permitted to ride on powered industrial trucks.
Operators should always wear seatbelts when operating a forklift and absolutely no stunt driving or horseplay is allowed. Do not allow passengers to ride on a forklift unless the forklift is specifically designed that way.
Forklift operators must have clear visibility of the work area to ensure they have enough clearance when raising, loading, and operating a forklift. Train forklift operators to watch for pedestrians and other vehicles in the warehouse, observe speed limits, and use horns at cross aisles and obstructed areas.
Consider the noise level in the warehouse. Do not assume other workers can hear the back-up alarm of the forklift.
When forklifts are in use in the warehouse, ensure there is adequate ventilation either by opened doors/windows or using a ventilation system to provide enough fresh air to keep concentrations of noxious gases from engine exhaust below acceptable limits.
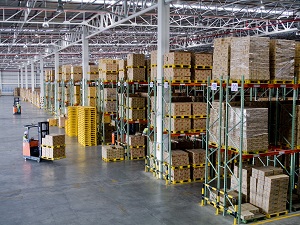
Slips, trips, and falls can be a danger in warehouses, especially if good housekeeping isn’t a priority. Materials may have a tendency to pile up in a way that obstructs or partially blocks the walkways or aisles. Keep paths clear so workers and forklifts can move safely.
OSHA Standard 1910.176(a) Aisles and passageways shall be kept clear and in good repair, with no obstruction across or in aisles that could create a hazard.
All areas shall be kept free from the accumulation of materials, trash, and extension cords that could be hazardous including anything else that could be a trip, fire, and pest hazards. Keep floors dry and clean up spills immediately.
OSHA Standard 1926.250(c) Storage areas shall be kept free from accumulation of materials that constitute hazards from tripping, fire, explosion, or pest harborage. Vegetation control will be exercised when necessary.
To prevent slip, trip, and fall hazards, provide these safety tips to warehouse workers.
- Walk, do not run, while in the warehouse.
- Never jump off forklifts, loading docks, or ladders.
- When walkways or aisles are blocked by pallets or other materials it is important to stop and carefully push or carry the items out of the way.
- Never kick materials or empty pallets when attempting to clear a path.
Exposed or open loading dock doors and other areas that workers could fall 4 feet or more or walk off should be chained off, roped off, or otherwise blocked.
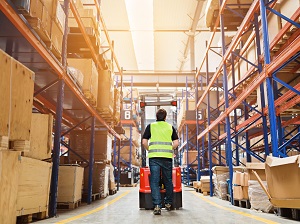
Warehouse workers must use caution when manually handling material and always use proper lifting technique. When pulling items from shelves or racks, only one item should be removed at a time.
If lifting is required to move a load, workers must keep their back straight, and bend at the knees, not at the waist. Never twist while lifting a load.
Heavier goods and materials that will be handled manually should be stacked on the bottom or mid-level shelves to reduce strain on the back. Prevent falling object hazards by stacking and storing materials safely.
Ensure stored materials, especially those items overhead, are not hanging over the edge of the shelf when they are stored. Put bound material on racks when possible, or secure items by stacking, blocking, or interlocking them to prevent sliding, falling, or collapsing. Whether stacking manually, or by forklift, allow sufficient clearance around materials for easy access and safe handling.
When stacking, consider the height restrictions, clearance limits, maximum safe load limits, and the need for availability of the material. Signs should be posted to remind workers of stacking height limitations and clearance limits.
Material and supplies should never block access to emergency exits, fire extinguishers, fire alarms, fire hoses, or electrical panel boxes.
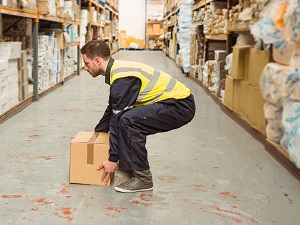
Warehouse workers must be aware of laceration and puncture hazards when packing or unpacking crates or boxes and watch for protrusions such as nails, screws, staples, splintering wood, broken boards, and metal banding or straps. Removing any sharp object that could cause injury should be a priority when unpacking.
When cutting shrink wrap, boxes or other material, workers must always direct the blade away from their face and body. Do not use any cutting device near the eyes/face and ensure co-workers are a safe distance from the area where blades of any kind are being used.
When ladders are used in the warehouse, workers should practice good ladder safety. All ladders should be inspected before each use and a damaged ladder must never be used. Workers must maintain 3 points of contact when climbing up or down a ladder.
Warehouse workers should have the opportunity to transport materials mechanically, when possible, to avoid overexertion or back injuries.
Pallet jacks should not be pulled down an incline. When descending any ramp, the pallet jack should be in front.
Hand trucks should be loaded for good balance and stability. When stacking, the heavier items should be placed on the bottom to keep the center of gravity of the load as low as possible.
