For those who are conducting the safety walk-around or inspection, OSHA provides a good deal of advice and best practices to get the most out of the experience, not only for the manager or safety department, but also for the organization.
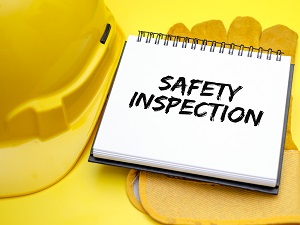
Workplace safety inspections are an important tool for identifying hazards and resolving them. A safety inspection can be a:
- periodic walk-around by managers or business owners
- comprehensive safety audit by the safety team
- thorough inspection focused on only one area
- comprehensive inspection covering the entire operation
- weekly inspection on a construction site
- monthly inspection in a warehouse or industrial facility
- quarterly safety review of an office building
- or any other safety inspection process that works best for your organization
Set up a schedule to inspect the job site or workplace on a regular basis. With everything else going on it’s very easy for the safety inspections to get pushed if they aren’t scheduled and prioritized.
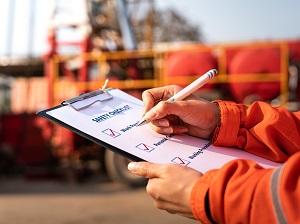
Preparation is important prior to starting an inspection. Take the time to familiarize yourself with the workplace and operations, and the hazards that have been previously identified. Be prepared to gather and document additional information from conversations with workers.
Where available, review prior inspection reports, injury and workers compensation records, incident investigation reports, and recent near-miss incidents. Use these to familiarize yourself with the most hazardous work areas, tasks, or activities. Focus the inspections on areas where hazards have been identified. Check to see if previously identified hazards have been eliminated or if further corrective action is needed.
Safety inspection checklists can take time to develop, and it’s okay to start with a generic checklist that has been provided by the organization, found online, or is already part of the safety program. Review the checklists you have, pick the best items that apply, and modify the lists as needed. After you have conducted a few inspections, you may want to develop more tailored checklists for different areas of the job site or facility.
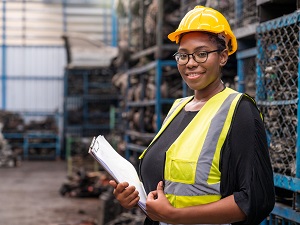
Determine what personal protective equipment (PPE) you will need to conduct inspections in all areas. It is important that as the person (or team) conducting safety inspections you lead by example and be prepared to use all necessary PPE, be aware of any posted safety warning signs, and follow safety procedures during the inspection.
As you begin a safety inspection, it may be easier to start with easily identifiable hazards, such as:
- Slip, trip, and fall hazards
- Blocked exits
- Frayed or exposed electrical wires
- Missing machine guards
- Poor housekeeping
- Poorly maintained equipment
Whenever possible, try to work with the supervisor and workers near the hazard to resolve the problem on the spot.
If you encounter more complex hazards during a safety inspection, recognize that you may need assistance. Hazards such as the following should be evaluated by a safety professional or industrial hygienist:
- Chemical hazards such as solvents, welding fumes, or toxic dust
- Noise exposure (areas where you need to raise your voice to be heard)
- Excessive heat
- Accumulations of combustible dust
For fixed worksites, such as a manufacturing facility, one effective method for conducting a wall-to-wall inspection is to start at the receiving area where materials enter, follow the materials through the process, and finish the inspection at the shipping department. This approach ensures that no area of the plant is missed. For other types of workplaces, such as offices and retail establishments, consider the layout and develop a plan that ensures that each work area is inspected.
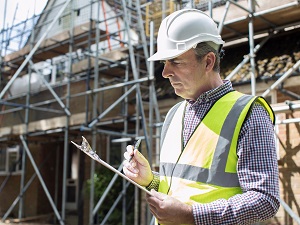
Workers are likely to know the most about hazards and safety issues so it’s important to chat with employees during the course of the inspection. Build personal relationships wherever possible. Assure them that you are interested in finding problems and fixing them. It’s important that workers understand the goal is to improve safety, and not to blame anyone for hazards found during the inspection. Avoid asking yes/no questions but encourage conversation instead.
Great questions to ask workers during a safety inspection include:
What is the most hazardous task in your job and what makes it hazardous?
If you have been injured on your job, what was the injury, how did it happen, and then what was done to make your job safer?
How would you report an injury, hazard, or near-miss?
The goal of workplace inspections is to develop a comprehensive list of hazards and to prioritize them for control. The strategies for achieving this goal recognize the reality that no single person is capable of identifying all hazards or determining appropriate controls. When you develop relationships and build trust with workers, the chances of success in preventing injuries, illnesses, and fatalities will increase.
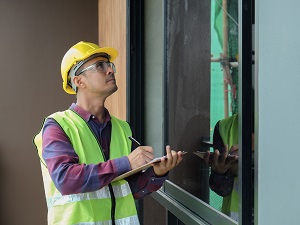
Following the inspection, prioritize the hazards based on the severity of the potential injury and the probability that an injury might occur. Use a risk assessment matrix or other system to prioritize, track, and follow up on hazards. The highest priority hazards are those that have a high probability of occurring and have the potential for the most serious outcomes.
Share the list of hazards with management, along with an estimate of what is involved in fixing them. Schedule time to go through the list so that they understand the problem, and how it could affect operations if not addressed. Use this opportunity to secure their commitment to provide the resources needed to fix any hazards.
To further demonstrate management’s commitment to improving safety and health, managers and owners should periodically conduct workplace inspections themselves. Walk-arounds let managers see for themselves how the safety and health program is working and whether it is effective in identifying and eliminating hazards. Safety walk-arounds can also help managers and owners assess how key elements of the safety program are working.
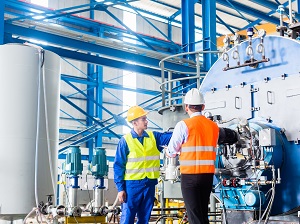