Although forklifts (powered industrial trucks) make work more efficient, they can pose serious hazards to those operating or working near them. Forklift operators and workers nearby are at risk of hazards such as collisions, falls, tip-overs, and struck-by conditions.
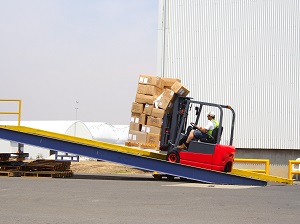
Forklift overturns are the leading cause of fatalities involving forklifts and they represent about 25% of all forklift-related deaths. Workers can also be injured when:
- forklifts are inadvertently driven off loading docks
- forklifts fall between docks and an unsecured trailer
- they are struck by a forklift.
- they fall while on elevated pallets or the forks of the lift.
Determining the best way to protect workers from injury largely depends on the type of forklift operated and the worksite where it is being used. Employers must ensure that each forklift operator is competent to operate a forklift safely, as demonstrated by the successful completion of training and evaluation.
Only trained and certified operators allowed! The first and most important rule to follow with forklifts – get trained!
Many injuries to both the operator and their co-workers occur because the user of the forklift was not trained in the specific model and type of forklift they tried to use.
It is a violation of Federal law for anyone UNDER 18 years of age to operate a forklift or for anyone OVER 18 years of age who is not properly trained and certified to do so.
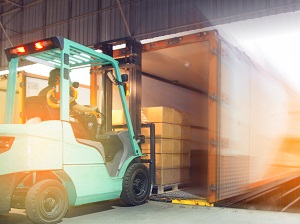
Before using a forklift, examine it for hazardous conditions which would make it unsafe to operate. The operator should conduct a pre-start visual check before turning the forklift on and then also perform an operational check with the engine running. Check and report unusual noises or excessive vibration. Remove from service any forklift found to be in unsafe operating condition.
OSHA General Industry Standard 1910.178(a)(4) Modifications and additions which affect capacity and safe operation shall not be performed by the customer or user without manufacturers prior written approval. Capacity, operation, and maintenance instruction plates, tags, or decals shall be changed accordingly.
Forklifts may be equipped with safety devices that should not be altered, removed or disabled. Examples of safety devices include seat belts, horns, back-up alarms, signals and brake lights, mirrors and flashing warning lights.
OSHA Construction Standard 1926.602(c)(1)(ii) No modifications or additions which affect the capacity or safe operation of the equipment shall be made without the manufacturer's written approval. If such modifications or changes are made, the capacity, operation, and maintenance instruction plates, tags, or decals shall be changed accordingly. In no case shall the original safety factor of the equipment be reduced.
Forklifts typically have warning labels or decals that provide safety information to operators. Safety labels should be clearly visible and must be replaced if missing, damaged, or illegible.
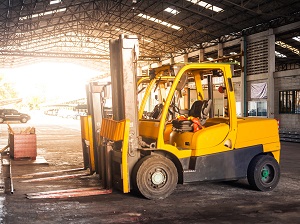
The nameplate found on every forklift provides important information for the operator, including the fuel type, forklift weight, and capacity. Forklift operators should read the nameplate to know the forklift’s capabilities and limitations.
OSHA General Industry Standard 1910.178(a)(6) The user shall see that all nameplates and markings are in place and are maintained in a legible condition.
Never exceed the rated load, and ensure loads are stable and balanced. Exceeding the capacity of a forklift presents serious hazards, including tip-over. If there is a special attachment, it must be listed on the nameplate. Do not operate a forklift with an illegible or missing nameplate.
OSHA Construction Standard 1926.602(c)(1)(i) Lift trucks, stackers, etc., shall have the rated capacity clearly posted on the vehicle so as to be clearly visible to the operator. These ratings shall not be exceeded.
Taking the following steps can protect workers from forklift hazards.
- Always wear seatbelts when operating a forklift.
- Be aware of other vehicles in the work area.
- Use horns at cross aisles and obstructed areas.
- Watch for pedestrians and observe speed limits.
- Keep a safe distance from platform and ramp edges.
- Have clear visibility of the work area and ensure you have enough clearance when raising, loading, and operating a forklift.
- Consider the noise level at the worksite. Do not assume other workers are able to hear a back-up alarm.
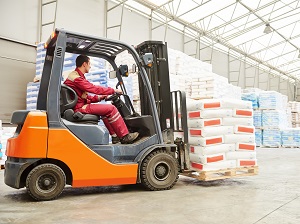
Drive loaded forklifts forward going up a ramp with the load upgrade and drive in reverse going down a ramp with the load upgrade. Always drive unloaded forklifts with the forks downgrade. Never drive with the load downgrade. Never turn a forklift on a grade.
Park forklifts on a hard, level surface when possible. Park in authorized areas only, and do not block traffic or emergency equipment. When parking, lower the lifting mechanism, neutralize the controls and engage the parking brake. Do not park on an incline, unless the wheels are blocked.
If the forklift has become disabled and the forks cannot be lowered to the floor, follow proper lockout/tagout procedures and do not allow anyone to stand or pass under the forks.
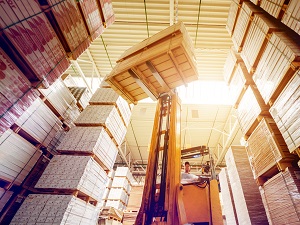
Do not raise or lower the load while traveling. Do not give rides or use the forks to lift people. Do not engage in stunt driving and horseplay.
OSHA Construction Standard 1926.602(c)(1)(vii) and General Industry Standard 1910.178(m)(3) Unauthorized personnel shall not be permitted to ride on powered industrial trucks. A safe place to ride shall be provided where riding of trucks is authorized.
Do not allow passenger(s) to ride on a forklift unless the forklift is specifically designed to accommodate passengers.
Forklift operators should use the proper footing and handhold when mounting and dismounting the forklift. Do not jump off the forklift.
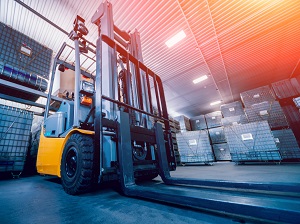