Performing safe lockout tagout requires workers to follow a series of steps that help to ensure that the equipment they are working on will not be started accidentally.
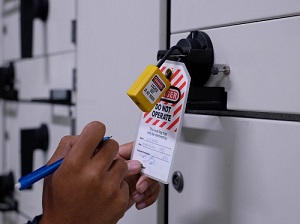
Steps for lockout/tagout could include:
- Notifying affected personnel before beginning lockout tagout work.
- Shutdown of the equipment by normal procedure.
- Isolate hazardous energy by using device(s).
- Apply locks and tags to the proper locations.
- Dissipate or restrain stored and/or residual energy.
- Verify lockout/tagout by making certain the equipment cannot be started accidentally.
OSHA Standard 1910.147(a)(3)(i) [requires employers to] utilize procedures for affixing appropriate lockout devices or tagout devices to energy isolating devices, and to disable machines or equipment to prevent unexpected energization, start up or release of stored energy in order to prevent injury to employees.
An important step during lockout/tagout is to isolate any possible hazardous energy by using certain types of devices.
Examples of lockout devices:
- Cable lockout devices that restrict handles or valves from moving.
- Flange lockout devices that prevent access to a blind flange to protect workers during pipeline activities.
- Circuit breaker, push button, or switch lockout devices that prevent a specific breaker or switch from being activated.
- Plug lockout covers to prevent machines or equipment from being plugged back in while they are being serviced or repaired.
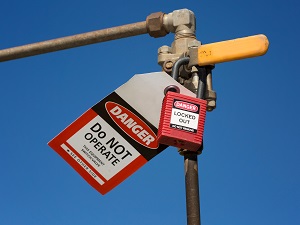
Locks and tags should be applied to the proper locations by trained and authorized workers. Lockout devices must be set so that they keep the equipment in a “safe” or “off” position.
Tags should be placed at the same point where the lock is attached and clearly indicate that the equipment should not be turned on, activated or operated. Tags should be labeled clearly with the necessary information including the identity of the employee applying the tags and warning statements to remind others not to attempt to turn on the equipment.
OSHA Standard 1910.147(d)(3) Machine or equipment isolation. All energy isolating devices that are needed to control the energy to the machine or equipment shall be physically located and operated in such a manner as to isolate the machine or equipment from the energy source(s).
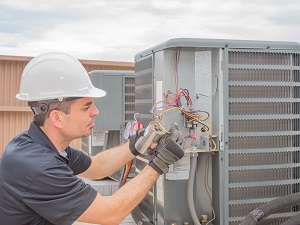
Dissipate or restrain stored and residual energy by methods such as grounding, repositioning, blocking, bleeding down, or other methods. Examples of areas that could contain stored or residual energy include:
- capacitors
- springs
- elevated machine parts
- air, gas, steam or water pressure
- rotating flywheels
- hydraulic systems
Before starting the actual work on the equipment, it is critically important to verify the lockout/tagout. Ensure the equipment is in a safe condition and that the lockout/tagout is complete by ensuring the equipment cannot be started accidentally.
Only trained and authorized workers can perform the verification and work under lockout/tagout.
OSHA Standard 1910.147(d)(6) Verification of isolation. Prior to starting work on machines or equipment that have been locked out or tagged out, the authorized employee shall verify that isolation and de-energization of the machine or equipment have been accomplished.
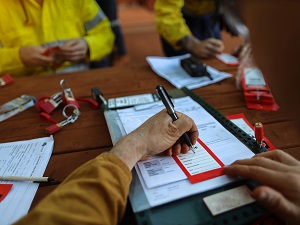