When the servicing or maintenance is completed, and the machine or equipment is ready to return to normal operating condition, lockout/tagout procedures for restoring service should be used to make sure all workers are protected.
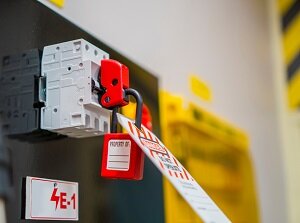
Steps to follow after lockout/tagout could include:
1. Check the machine or equipment and the immediate area around the machine to ensure that nonessential items have been removed.
2. Confirm that all employees have been safely positioned or removed from the area.
3. Verify that the controls are in neutral, set to off, or in a ready-state, if applicable.
4. Remove the lockout devices and energy isolating devices and re-energize the machine or equipment.
5. Notify affected employees that the servicing or maintenance is completed, and the machine or equipment is ready for use.
OSHA Standard 1910.147(e) Before lockout or tagout devices are removed and energy is restored to the machine or equipment, procedures shall be followed and actions taken by the authorized employee(s)…
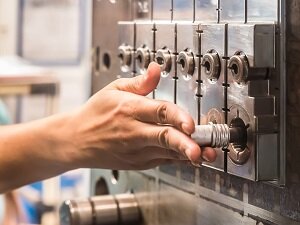
One of the first steps to restoring equipment after lockout/tagout is to check the machine or equipment and the immediate area to ensure that nonessential items have been removed.
- Ensure that all tools have been accounted for and have not been left in or on the machine.
- Replace all machine and equipment components, safety mechanisms, covers, and guards.
- Return all parts, spare parts, accessories, and damaged components to the appropriate locations or inventories.
OSHA Standard 1910.147(e)(1) The machine or equipment. The work area shall be inspected to ensure that nonessential items have been removed and to ensure that machine or equipment components are operationally intact.
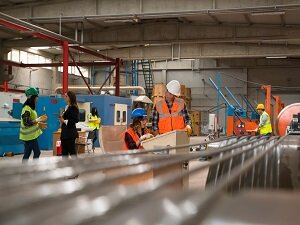
Workers completing any project with lockout/tagout are required to make sure that there are no people inside of, around, or near the equipment to be restarted.
Before removing any lockout/tagout devices inspect the work area and account for all personnel including:
- Equipment operators, maintenance personnel or contractors
- Workers returning from lunch, a break, or shift change
- Inspectors, laborers, and cleaning personnel
OSHA Standard 1910.147(e)(2)(i) The work area shall be checked to ensure that all employees have been safely positioned or removed.
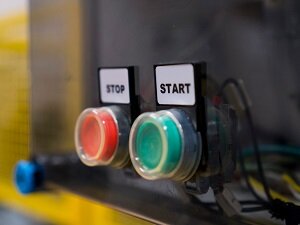
To make sure lockout/tagout removal is performed safely, each lock and tag should be removed from each energy isolating device by the employee who applied them.
In some situations, the original worker who placed the lockout/tagout device may not be available due to a shift or employment change, illness, or other emergency.
When the authorized employee who applied the lockout or tagout device is not available to remove it, procedures and training for removal should be developed and followed.
Steps could include:
- verification that the authorized employee who applied the device is not at the facility
- making all reasonable efforts to contact the authorized employee to inform them that their lockout or tagout device has been removed
- ensuring that the authorized employee has this knowledge before they resume work at that location
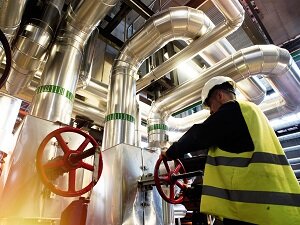
Any project involving the use of lockout/tagout can be very dangerous, not only for the authorized workers, but also for the people who may be assigned to use the equipment.
Only trained and authorized workers can perform the lockout, verification or removal and work under lockout/tagout.
Notify affected employees that the servicing or maintenance is completed, and the machine or equipment is ready for use.
OSHA Standard 1910.147(e)(2)(ii) After lockout or tagout devices have been removed and before a machine or equipment is started, affected employees shall be notified that the lockout or tagout device(s) have been removed.
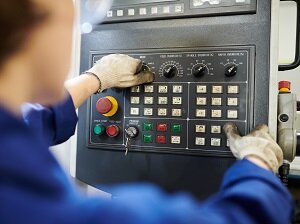