Because conveyor hazards vary depending on the application, it is important that machine guarding, secondary safeguarding methods, and lockout/tagout practices are implemented in effective ways that promote worker safety.
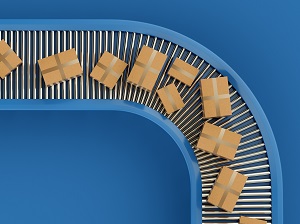
Conveyors are used in many industries to transport materials horizontally, vertically, at an angle, or around curves. Many conveyors have different and unique features and uses, so that hazards vary due to the materials being handled, the location of the conveyor, and the proximity of the conveyer to workers. There are different types of conveyors including unpowered and powered, live roller, slat, chain, screw, and pneumatic.
Conveyors eliminate or reduce manual material handling tasks, but they can introduce caught-in, crushed-by, struck-by, and amputation hazards associated with mechanical motion. Conveyor-related injuries typically involve a worker’s hands or fingers becoming caught in nip points or shear points on conveyors which can occur when:
- cleaning and maintaining a conveyor, especially when it is still operating.
- reaching into an in-going nip point to remove debris or to free jammed material.
- allowing a cleaning cloth or clothing to get caught which can then pull fingers or hands into the conveyor.
There are also hazards associated with the materials being handled if items fall off, break, or are ejected from the conveyor system.
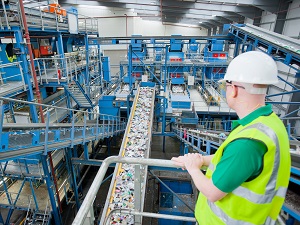
Where necessary for the protection of workers, conveyors need to have mechanical guards that protect the employee from nip points, shear points, and other moving parts, including power-transmission apparatus.
Guards may include barriers, enclosures, grating, fences, or other obstructions that prevent inadvertent physical contact with operating machine components, such as point of operation areas, belts, gears, sprockets, chains, and other moving parts.
OSHA Standard 1910.212(a)(1) One or more methods of machine guarding shall be provided to protect the operator and other employees in the machine area from hazards such as those created by point of operation, ingoing nip points, rotating parts, flying chips and sparks.
Do not remove, bypass, or alter the conveyor guards or safety barriers. The conveyor should only be in operation when all guards and safety devices are in place and working properly.
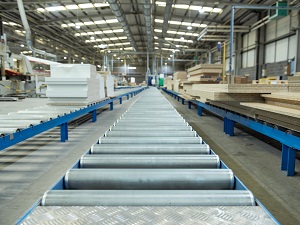
Secondary safeguarding methods, work practices, and additional equipment may be used along with the primary machine guards for additional protection, or when machine guards are not feasible.
Distance. Locate moving parts away from workers to prevent contact with hazard points.
Signals. Prominent warning signs or lights can be used to alert workers to the conveyor operation. An audible warning signal can be sounded immediately before the conveyor starts up.
Training. Only trained individuals are allowed to operate or work near conveyors, and only trained and authorized staff are allowed to perform servicing and maintenance work.
Inspections. The entire conveyor and immediate work area should be inspected prior to start-up and any hazards should be eliminated before starting the equipment.
Testing. Inspect and test conveyor safety mechanisms, like the alarms, emergency stops, and safeguarding methods.
Clothing. Employees working near conveyors should not wear loose clothing or jewelry that can get snagged or caught, and long hair should be tied back, tucked under a net or a cap, or otherwise secured.
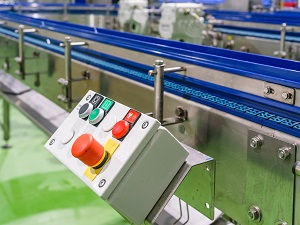
Conveyors should have emergency stop devices installed where employees work when they cannot otherwise control the movement of the conveyor. This recognized safety feature provides workers with the means to shut off the equipment in the event of a hazardous situation or emergency incident.
Interlocking devices will shut conveyors down during an electrical or mechanical overload (like a product jam or other stoppage) and should be installed in such a way that cannot be overridden from other locations.
Clearly marked, unobstructed emergency stop buttons, or pull cords, for the conveyors should be installed within easy reach of employees. Emergency stop controls should require manual resetting before conveyor operation resumes.
- Do not use any conveyor which is unsafe until it is made safe.
- Personnel must never climb, step, sit, or stand on conveyors.
- No one should be near the conveyor equipment as it is starting up.
- Never modify or misuse the conveyor controls.
- Report all unsafe conditions.
Reminder! All visitors must be informed of the safe behavior required if they will be going near the conveyors.
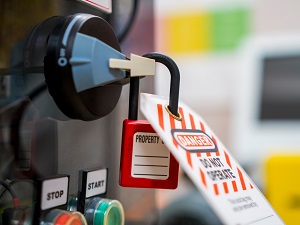
Servicing and maintenance of conveyor systems should only be performed by trained and authorized personnel following proper lockout/tagout procedures. Conveyors shall be locked out or otherwise rendered inoperable and tagged out with a "Do Not Operate" tag during maintenance or repairs when operation is hazardous to employees performing service work.
OSHA Standard 1910.147(c)(1) The employer shall establish a program consisting of energy control procedures, employee training and periodic inspections to ensure that before any employee performs any servicing or maintenance on a machine or equipment where the unexpected energizing, startup or release of stored energy could occur and cause injury, the machine or equipment shall be isolated from the energy source and rendered inoperative.
At times, OSHA recognizes that some minor servicing may have to be performed during normal production operations, so a lockout/tagout exception is allowed. An example of a common conveyor minor servicing activity involves package jams where an employee must frequently dislodge the jam. To prevent unexpected start-up of the conveyor, employers may adopt alternative control measures, such as opening (placing in the off position) local disconnects or control switches to prevent conveyor start-up. These properly applied devices, if used, must be under the exclusive control of the employee performing the jam release, so that no other person can restart the conveyor without the knowledge and consent of the person performing the servicing work.
Only trained and authorized personnel should clear material jams and remove trash or other debris when lockout/tagout procedures are in effect.
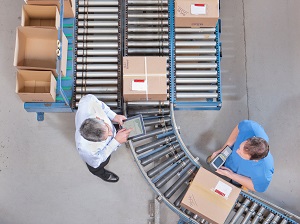