Periodically, employers should assess their safety and health program to make sure it is working as intended and achieving the goals set by the organization. If there are any areas that need improvement, they should be fixed which then drives the continual improvement of the safety and health program.
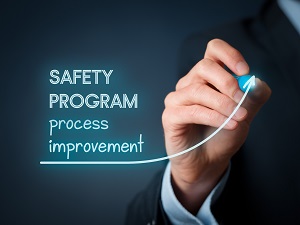
The scope and frequency of safety program evaluations will depend on the program's complexity, how long it has been in place, and what types of hazards it needs to control. Evaluations should be conducted periodically (at least once a year) but might also be needed if there is a change in the program, equipment, or an incident occurs.
There are three steps to any safety program evaluation which are 1) monitor safety data, 2) review how effective the program is, and 3) identify opportunities for improvement and make corrections.
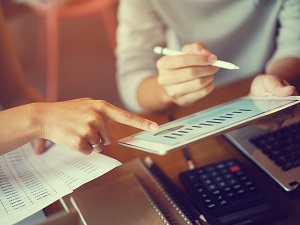
MONITORING SAFETY PROGRAM PERFORMANCE
Use both lagging and leading indicators to measure the most valuable data points to look at that will give you an overall view of how well the program is supporting and achieving the safety goals of the company.
Establish procedures that will accurately collect the statistics you want to review and ensure training is in place for everyone involved in process of recording the results.
Lagging indicators track worker exposures, workplace hazards, incidents, and injuries that have already occurred. Examples of lagging indicators are:
- Number, type, and severity of incidents and illnesses that have happened
- Monitoring results that indicate hazardous levels of exposure
- Workers’ compensation data, including claim counts, rates, and cost
Leading indicators track how well various aspects of the program have been implemented and reflect steps taken to prevent incidents before they occur. Examples of leading indicators include:
- Percentage of workers who have completed their required safety training
- Number of workplace hazards or near misses reported
- Average time to correct reported safety concerns
Keep in mind that the indicators you choose to measure may be quantitative or qualitative. When possible, select indicators that are measurable (quantitative) because that type of data gives you a better understanding of the overall safety program performance.
The number of workplace hazards reported every week is a quantitative indicator. One worker submitting a negative opinion about the safety training program is a qualitative indicator.
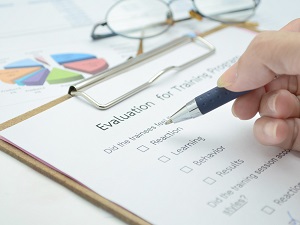
VERIFYING EFFECTIVENESS OF THE SAFETY PROGRAM
After indicators are established, measurements are taken, and data is compiled, the safety program components should be reviewed to ensure they are 1) implemented, and 2) effective. It’s important to involve employees in the evaluation process.
Confirm that key processes and intentions of the safety and health program are functional and operating as intended. The safety program areas and processes to evaluate may include:
- Hazard, near miss, and safety concern reporting
- Incident, injury, and illness reporting and investigation
- Employee training
- Hazard control measures
- Forms and inspections completion
- Personal protective equipment (PPE)
During the review process the organization may find that many portions of the safety and health program are working well, as intended, but there may be some areas that are ineffective or could be improved to provide a safer working environment.
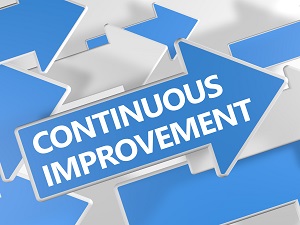
SAFETY PROGRAM CONTINUAL IMPROVEMENT
If any deficiencies are discovered during the review process of the safety and health program the next step is to take action to improve those program areas, processes, or procedures so they start working as originally intended. Or, the review may even find gaps in the program where new processes need to be considered and implemented.
Proactively seek input and feedback from managers, workers, and supervisors on how to best improve the safety program.
Determine whether changes in equipment, facilities, materials, key personnel, or work practices trigger any need for changes in the program.
Finally, evaluate whether your performance indicators and safety goals are still relevant and, if not, how you could change them to more effectively drive improvements in workplace safety and health.
For more information on how to evaluate and improve your workplace safety and health program, download a copy of OSHA’s booklet Recommended Practices for Safety and Health Programs.
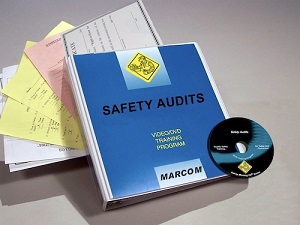