Leading indicators can play a vital role in preventing worker fatalities, injuries, and illnesses and strengthening other safety and health outcomes in the workplace.
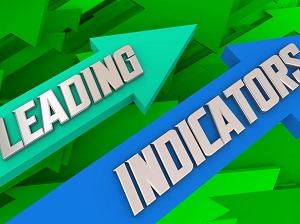
Leading indicators are proactive and preventive measures that can shed light about the effectiveness of safety and health activities and reveal potential problems in a safety and health program.
Leading indicators can be a valuable tool and may work to improve organizational performance in a variety of ways. Employers may find that leading indicators can:
- Prevent workplace injuries and illnesses
- Reduce costs associated with incidents
- Improve productivity and overall organizational performance
- Optimize safety and health performance
- Raise worker participation
Many employers are familiar with lagging indicators. Lagging indicators measure the occurrence and frequency of events that occurred in the past, such as the number or rate of injuries, illnesses, and fatalities. While lagging indicators can alert you to a failure in an area of your safety and health program or to the existence of a hazard, leading indicators are important because they can tell you whether your safety and health activities are effective at preventing incidents. A good safety and health program uses leading indicators to drive change and lagging indicators to measure effectiveness.
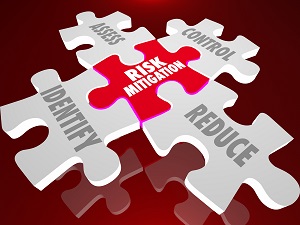
There is no one size fits all way to use leading indicators. Employers with newer programs may use indicators that focus on starting a program, while employers with more mature programs may use them to monitor how close they are to achieving higher performance targets.
Some employers may find it helpful to limit the number of leading indicators they start out with or how many they use at any one time. How employers assign who will track and carry out goals for leading indicators can vary based on the size of the business, who the business has on staff, whether the business has a safety manager, and the scope of job duties of the workforce.
THE STEPS FOR USING LEADING INDICATORS
PLAN – Choose the leading indicator, set a goal, and decide how to track it.
DO – Collect data and then measure and communicate the progress.
CHECK – After some time, evaluate progress towards the goal and review regularly. Reassess if needed.
ACT – Respond to what you’ve learned from measuring this leading indicator and communicate the results.
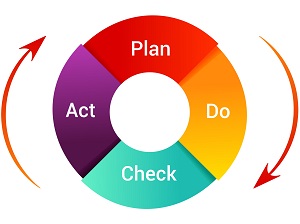
Good leading indicators are based on SMART principles, meaning they are Specific, Measurable, Achievable, Relevant, and Timely:
Specific: The leading indicator provides specific information for the action that minimize risk from a hazard or improve a program area.
Measurable: The leading indicator is presented as a number, rate, or percentage that allows the organization to track and evaluate clear trends over time.
Achievable: The organization can reasonably achieve the goal that is set for the leading indicator.
Relevant: The leading indicator tracks an item that is relevant to the safety goal.
Timely: The leading indicator is tracked regularly enough to spot meaningful trends from the data within the desired timeframe.
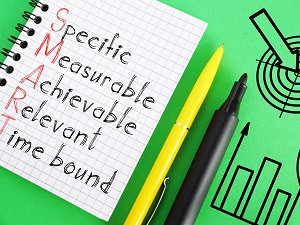
Examples of leading indicators that can be measured that might be used to improve a specific part of the safety and health program:
- Number of workers who attend a monthly safety meeting
- Average time between worker report of a hazard or concern and management acknowledgement of the report
- Number of times each month that top management initiates discussion of a safety and health topic
- Number of workers involved in developing task-specific job hazard analysis on how to perform routine tasks safely
- Frequency with which preventive equipment maintenance tasks are initiated and completed on schedule
- Percentage of incident investigations that include a root cause investigation
- Number of special work permits filled out
- Number of workers required to wear respiratory protection
- Percentage of workers receiving mandatory training on schedule
- Number of audits conducted to ensure contractors are following site safety and health policies to include in their own safety policies
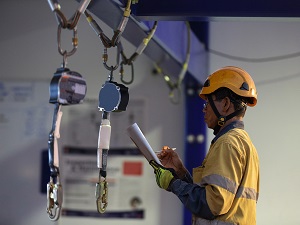
Follow this plan, provided by OSHA, to begin using leading indicators to improve your safety and health program.
Identify your top problem areas. For hazards, review your injury logs, and results from your hazard assessments. Start with the hazard with the greatest risk of harming workers by evaluating the severity of the potential exposure and the likelihood that an incident could occur. Prioritize hazards over other areas of your program, particularly if a threat is imminent.
For other program elements, talk with your workers about what areas you could improve. For data that you are already collecting, determine whether it is an area that you should prioritize.
Consider what actions you could take to address your key areas. Talk with your workers and anyone else with knowledge of the issue that can provide suggestions.
Set a goal and use leading indicators to reach it. Make an informed decision on what your goal should be and how long it might take to achieve. Choose a leading indicator that can help you to achieve your goal over time.
Collect the data. Begin collecting the leading indicator data for the time period you decided on as well as the data for your goal during that same time period.
Review the results periodically. Assemble the results into a graph to determine whether there is a positive relationship between your leading indicator and your goal. Did the action that you took help you to achieve your goal? If not, try something else.
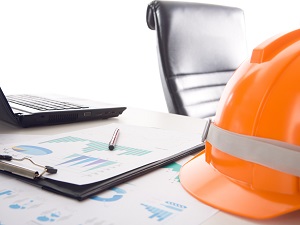
Remember that just one or two indicators can make a positive impact. OSHA recommends getting started right away and customizing the type and number of indicators to your needs, resources, and abilities as they evolve over time.
For more information on how to use leading indicators, along with plenty of specific examples, download a copy of OSHA’s booklet Using Leading Indicators to Improve Safety and Health Outcomes.