Quality and safety are different, but they also work hand in hand, enhancing each other to create a more efficient and productive work environment.

Quality and Safety represent two critical aspects of an organization, but they are not the same. The goal of a quality department is to ensure that an organization's products or services meet or surpass established standards and customer expectations. The goal of workplace safety is to create a secure environment where employees can perform their duties without fear of injury or health hazards.
Depending on how an organization is structured, it might seem like quality and safety are two completely separate goals, or alternatively, the two workplace standards may be operating smoothly as one department. But a more likely scenario is somewhere in the middle.
Regardless of how the org chart is set up, workplace quality and safety are deeply interconnected, each playing a crucial role in the success and sustainability of any business. As an organization grows, the relationship between quality and safety will evolve.
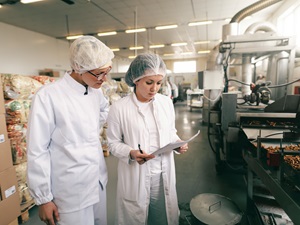
Quality is how well a product or service meets what customers need and want. Quality is about giving customers good value and making sure they're happy with what they get.
Quality can be checked in different ways, like how well something works, how long it lasts, if it does what it's supposed to do, and how it looks. To ensure quality, organizations must establish quality standards and implement control processes to check and make their products or services better.
Product safety is an important aspect of quality assurance. Consumers expect products that are safe and reliable.
Safety is primarily focused on making sure everyone on the job stays healthy and safe while meeting production deadlines or providing services to customers.
Safety is checked by looking at possible dangers, risks, incidents, and compliance with established regulatory standards. To ensure safety, organizations should be identifying and managing safety hazards and then implementing corrective and preventive actions to minimize or eliminate those risks.
A more robust safety department may encompass environment, health, and safety (EHS) as it works to protect personnel and the environment from harm.
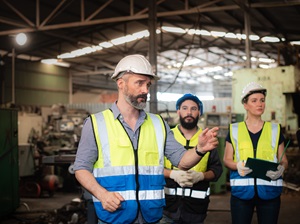
Quality and Safety may assume they should operate on their own especially when other departments like operations, logistics, sales, and product development are also fueling the competition in an effort to be the top priority for a company.
But the truth is, quality and safety (along with production and logistics) should be working together with a focus on continuous improvement, not for one individual department, but for the entire organization.
A safe work environment has a better chance to foster a sense of security among employees because workers may feel valued and respected if they feel like their company is taking care of them.
A positive work culture encourages dedication and a high level of workmanship, which is directly linked to the quality of output.
Employees who take pride in their work are more likely to produce superior results, and adhere to the safety protocols, further reinforcing the cycle of safety and quality.
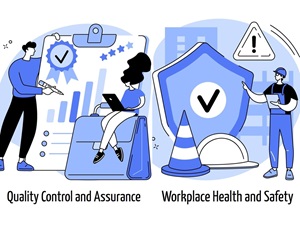
Quality and safety management in the workplace share many common processes, making them integral to each other's success.
Both quality and safety require a risk-based approach, identifying and prioritizing risks to manage them effectively. This involves tracking key metrics to ensure risk controls are working and making adjustments as necessary.
A focus on quality can enhance safety measures because quality control processes often involve detailed inspections and reviews to identify and correct errors. Quality control processes can uncover potential safety hazards, allowing for proactive measures to prevent accidents.
By integrating quality checks with safety audits, companies can identify areas of improvement more effectively, ensuring that both safety and quality standards are continuously being elevated.
Documentation is crucial for both quality and safety, involving the creation and maintenance of policies, processes, and incident records in an accessible and manageable system.
Involving employees in both quality and safety discussions encourages a culture of shared responsibility. Employee feedback can provide practical insights and promote engagement.
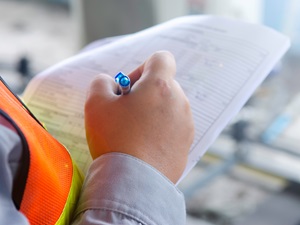
Risk assessment, root cause analysis, and corrective and preventative actions are all common and essential parts of both quality and safety management.
The quality department conducts risk assessments to identify potential issues in product design or manufacturing processes that could impact product quality, while the safety department performs risk assessments to spot hazards that could cause accidents or health issues for employees.
Both departments use root cause analysis to dig deep into incidents or non-conformities. The quality department focuses on product or service failures, while the safety department investigates on-the-job incidents.
The quality department implements corrective actions to fix identified quality issues, ensuring products or services meet the required standards. The safety department takes corrective actions to remove or reduce workplace hazards, protecting employees and the environment.
In quality management, preventative actions involve adjusting processes and systems in advance to avoid potential quality failures. For safety, preventative actions might include implementing new safety protocols or training programs to prevent future incidents.
Both departments often collaborate on investigations and solutions, especially when issues overlap between quality and safety, ensuring a comprehensive management of risks.
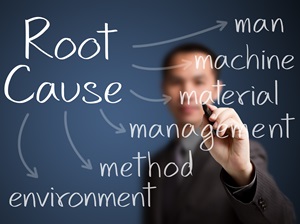
In practice, the integration of workplace quality and safety requires ongoing commitment and collaboration across all levels of an organization.
From top management to frontline workers, everyone has a role in upholding safety standards and striving for excellence in quality.
Regular training sessions, open communication channels, and a transparent feedback system can help in aligning an organization’s quality and safety goals.
By fostering a culture that equally values both quality and safety, businesses can achieve a competitive edge, ensuring not only the well-being of their employees but also the satisfaction of their customers.
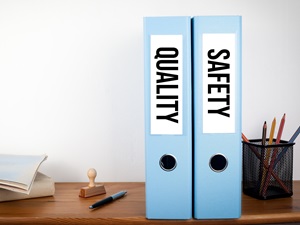