Safety Audits are a step forward as organizations become more proactive with their health and safety programs instead of only being reactive when something unexpected happens.
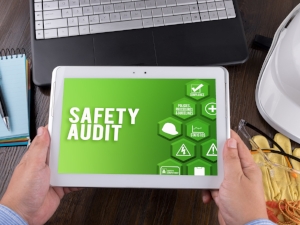
What is a safety audit?
A safety audit is an in-depth, impartial review of a company or organization’s health and safety program, procedures and processes. Safety audits report on a safety program’s effectiveness, completeness and reliability.
Are safety audits required by OSHA?
While there is no specific standard or requirement by OSHA for safety audits, OSHA’s position is that self-audits are an important part of an effective [safety] program. OSHA does require that employers take responsibility for accident prevention and any safety program should include processes (like safety audits, job site inspections, equipment inspections, etc.), that demonstrate there are preventative measures in place.
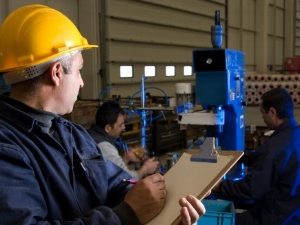
What should be reviewed during a safety audit?
Although every safety audit should be specifically tailored to the organization, program and time-frame provided, here are the top issues that are recommended for review during any safety audit:
- Is information about the safety program’s effectiveness and reliability tracked?
- Does the health and safety program cover all regulatory and industry requirements?
- Are there hazard identification, assessment, prevention and control procedures?
- Have communication and emergency procedures been established?
- Is there a safety training and education program and is employee training comprehensive and effective?
- Is the safety program aligned with and in support of the company’s goals?
- How is employee participation addressed in the safety program?
- What documentation is there to support proof of compliance?
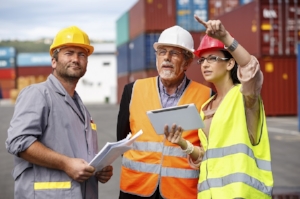
Why are safety audits important?
According to OSHA, “Employers derive many benefits from effective safety and health programs that provide for audits, including reduced absenteeism, lower workers' compensation premiums and payments for medical treatment and disability, and favorable treatment from OSHA. Employers with effective programs have fewer and less serious hazards and thereby face reduced exposure to OSHA citations and penalties as a result.”
Who conducts a safety audit?
Safety audits should be conducted by trained personnel that can be neutral and objective when conducting and reporting on the results of the audit. A great approach is to assign 3 – 5 people representing a variety of departments to complete the audit, as long as those individuals are not assigned to audit their own department. Another option is to hire qualified consultants to complete the audit.
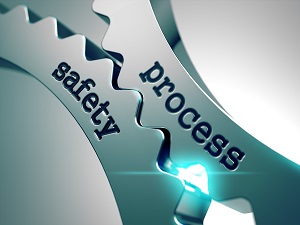
How is a safety audit conducted?
Here are the basic guidelines to get started with a safety audit.
- Determine the scope and time frame of the audit.
- Prior to the audit, inform all personnel who might be affected by the audit to ensure they will be available and will have all required documentation made available as well.
- Review all past audits and make notes regarding past problem areas and corrective/preventative actions that have been taken.
- Review all company, local, state and federal requirements.
- Prepare an outline for the audit including items to review, inspections to be made and questions that need to be answered.
- Conduct documentations reviews, walk-throughs, inspections, and interviews as appropriate.
- Compile all pertinent audit data to prepare a concise report of the audit outcome, including positive findings, areas of deficiency and recommendations for improvements.
To get started, OSHA has prepared a Safety and Health Audit Tool that can assist any organization with preparing for and completing a safety audit.
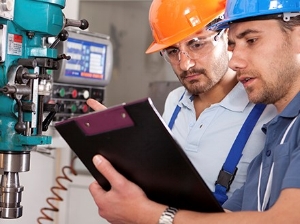
How often should safety audits be conducted?
At least one comprehensive safety audit should be scheduled every year. A different, but effective, approach is to schedule targeted safety audits throughout the year. For example, every department may have their own safety audit completed on a rotating schedule throughout the year, and then a comprehensive company-wide safety audit on high-level procedures can be conducted at the end of the year. Any safety audit schedule should be on a regular schedule, documented as such and effectively communicated to all employees.
What happens after a safety audit?
Acknowledge departments, managers and supervisors who participated in the safety audit and highlight positive findings. Recommendations should be developed for each deficient area found during the audit. Corrective action should be taken to immediately correct hazards and preventative action should be implemented to ensure procedures are in place prevent future issues. All recommendations and actions taken should be documented and saved for future reference. Follow-up reviews should be scheduled to ensure all corrective and preventative actions were implemented and are effective.
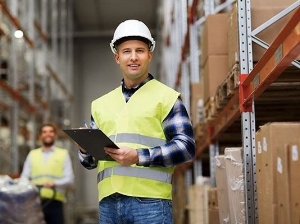