Laboratory workers are exposed to numerous potential hazards including chemical, biological, physical and radioactive hazards, as well as musculoskeletal stresses. The safety of all workers depends on clearly defined attitudes of teamwork and personal responsibility. To be most effective, safety and health must be balanced with, and incorporated into, standardized laboratory processes and procedures.
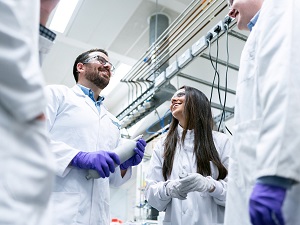
Laboratory personnel have the right to a safe working environment, but also have the responsibility to:
- read, understand, and follow all safety rules and regulations.
- plan and conduct each operation following the guidelines of the chemical hygiene procedures.
- promote good housekeeping practices.
- notify the supervisor of any hazardous conditions or unsafe work practices.
- use appropriate PPE for each procedure that involves hazardous chemicals.
OSHA Standard 1910.1450 found within Subpart Z covers Occupation Exposure to Hazardous Chemicals in Laboratories
All lab workers must receive information and training at the time of an employee's initial assignment to a work area where hazardous chemicals are present and prior to assignments involving new exposure situations. The frequency of refresher information and training will be determined by the employer.
OSHA Standard 1910.1450(f)(1) The employer shall provide employees with information and training to ensure that they are apprised of the hazards of chemicals present in their work area.
When working in a lab, it’s important to wear appropriate clothing and effective personal protective equipment (PPE).
Safety glasses, preferably with side shields, are recommended for all lab work. Chemical splash goggles protect against projectile hazards, when working with glassware under reduced or elevated pressures, when handling potentially explosive compounds, and when using glassware in high-temp operations. When pouring large quantities of hazardous chemicals, in addition to goggles, wear a face shield large enough to protect your ears and neck as well as your face.
To protect your skin, wear a lab coat and choose gloves appropriate for the chemicals being handled. Wear closed-toe shoes and long pants (or other clothing) that cover your legs and ankles. Never wear gloves or lab coats outside the laboratory or into areas where food is stored and consumed.
After a risk assessment, some hazards may require additional PPE like a lab apron or respiratory protection. Remove PPE before leaving the lab.
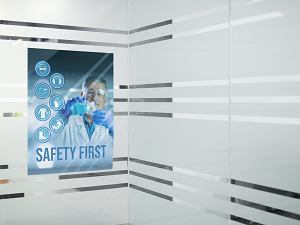
All workplace laboratories are different with each one serving a unique purpose for the specific facility or population it serves, but there are some general safety guidelines that apply to most lab work environments where hazardous chemicals are used and stored.
Perform risk assessments for hazardous chemicals and procedures prior to laboratory work. Minimize chemical exposure through consistent and proper use of engineering controls like laboratory fume hoods, glove boxes, or other ventilated enclosures. OSHA’s Permissible Exposure Limits (PELs) must not be exceeded.
OSHA Standard 1910.1450(c) For laboratory uses of OSHA regulated substances, the employer shall assure that laboratory employees' exposures to such substances do not exceed the permissible exposure limits specified in 29 CFR part 1910, subpart Z.
Maintain situational awareness and know the locations and proper use of safety equipment. Do not allow unauthorized persons to enter the laboratory.
Laboratories rely on a vast array of electrically powered equipment. To work safely with this equipment, employees need to be aware of common electrical hazards in the lab and know how to use the equipment safely.
All containers for chemicals must be clearly labeled. Container labels must be legible, permanently displayed, written in English, and include the following information:
- identity of the chemical and appropriate hazard warnings
- primary health and/or physical hazard(s) clearly conveyed through the use of words, pictures, symbols, or a combination of these elements
- name and address of the manufacturer, importer or other responsible party
OSHA Standard 1910.1450(h)(1)(i) Employers shall ensure that labels on incoming containers of hazardous chemicals are not removed or defaced.
The existing label on a container entering the laboratory from a supplier must not be removed, altered or defaced. If a chemical container’s original label must be replaced, the new label must contain the same information as the original. Only use labels, ink and markings that are not soluble in the liquid content of the container.
Often, laboratory operations require transferring chemicals from the original labeled container into a secondary container, like a beaker, flask, or bottle. Labels on these portable containers are not required if the worker who made the transfer uses all the contents immediately during the work shift, but these secondary containers must comply with labeling requirements if:
- the material is not used within the work shift of the individual who makes the transfer.
- the worker who made the transfer leaves the work area.
- the container is moved to another work area and is no longer in the possession of the worker who filled the container.
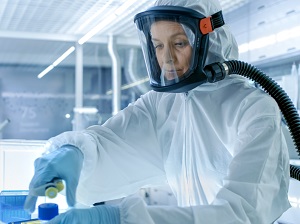
Before beginning any laboratory work, the hazards and risks associated with an experiment or activity should be determined and the necessary safety precautions implemented.
- Identify chemicals to be used, amounts required, and how they will be used. Consider any conditions that could create or increase a hazard.
- Evaluate the hazards posed by the chemicals and the experimental conditions. The evaluation should cover toxic, physical, reactive, flammable, explosive, radiation, and biological hazards, as well as any other potential hazards posed by the chemicals.
- Select appropriate controls to minimize risk and ensure that OSHA’s Permissible Exposure Limits (PELs) are not exceeded.
- Prepare for contingencies and be aware of emergency procedures.
One approach to risk assessment is to answer these questions:
- What are the hazards?
- What is the worst thing that could happen?
- What can be done to prevent this from happening?
- What can be done to protect from these hazards?
- What should be done if something goes wrong?
Even for substances of no known significant hazard, exposure should be minimized. When working with substances that present special hazards, appropriate precautions should be taken. Reference should be made to the safety data sheet (SDS) that is provided for each chemical.
OSHA Standard 1910.1450(h)(1)(ii) Employers shall maintain any safety data sheets that are received with incoming shipments of hazardous chemicals, and ensure that they are readily accessible to laboratory employees.
Determine the physical and health hazards associated with chemicals before working with them. Assume that unknown materials are toxic, and that a mixture is even more toxic than its most toxic component.
Avoid direct contact with any chemical. Never smell, inhale or taste laboratory chemicals. Never use your mouth to suction for pipetting or siphoning. Use a pipette bulb or other suitable device. Handle needles, syringes and other sharps carefully. Use self-sheathing needles whenever possible. Dispose of all sharps in an appropriate sharps container. Properly dispose of chemical wastes.
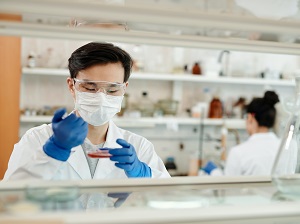
Housekeeping and personal hygiene are both important components of laboratory safety and can help reduce or eliminate many hazards. Proper housekeeping includes appropriate labeling and storage of chemicals, safe and regular cleaning of the facility, proper arrangement of laboratory equipment and being continuously mindful of personal hygiene helps to minimize accidental chemical exposure.
Keep work areas clean and uncluttered. Clean up upon completion of an operation and at the end of the workday. Do not block (even temporarily) emergency showers, eye washes, fire extinguishers, emergency equipment, hallways or exits.
Wash your hands frequently to minimize chemical exposure through ingestion and direct skin contact. Always wash your hands after working with hazardous chemicals, even if gloves have been worn. Always wash your hands before eating, drinking or touching your face.
Do not store or prepare food in the lab. Food, beverages, cups, and utensils should not be stored in areas where hazardous chemicals are handled or stored. Never eat, drink, chew gum or tobacco, smoke or apply cosmetics in the laboratory.
Safe chemical storage and access is as important as chemical handling procedures in the laboratory. Chemical storage and handling rooms should be controlled-access areas.
Highly hazardous chemicals should be stored in a well-ventilated and secure area designated for that purpose. Compressed gas cylinders must be secured to prevent them from being knocked over. Cylinders must be capped when the regulator is removed or not in use. Flammable chemicals should be stored in a spark-free environment and in approved flammable-liquid containers and storage cabinets. Grounding and bonding should be used to prevent static charge buildups when dispensing solvents.
Use appropriate safety carriers (secondary containment) when transporting chemicals, either inside or outside of the building.
- Use secondary containers such as acid buckets or plastic totes. Transport containers should be break-resistant.
- Secure containers on carts.
- Wear appropriate PPE.
- Use freight elevators or limit access in passenger elevators. Avoid high-traffic areas.
- Use a hand truck with a safety chain when moving compressed gas cylinders.
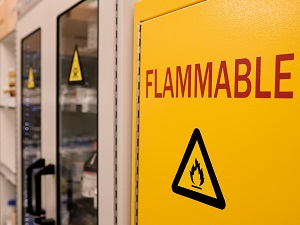
Prominent signs of the following types should be posted:
- Phone numbers of emergency personnel/facilities and supervisors.
- Location signs for safety showers, eyewash stations, other safety and first aid equipment, and exits.
- Warnings at areas or equipment where hazards exist, including additional PPE requirements.
Before working with any chemicals, know the location of emergency equipment as well as the facility procedures for handling an accidental spill, fire, or other emergency situation. Safety equipment, including spill control kits, safety shields, fire safety equipment, PPE, safety showers and eyewash units, and emergency equipment should be available in clearly marked locations in or near the lab. Locate the nearest exit(s) from the laboratory area in case of an emergency. Report all injuries, incidents, near misses and unsafe conditions.
- Never perform unauthorized work, preparations or experiments.
- Never engage in horseplay or pranks.
- Never remove chemicals from the facility without proper authorization.
Working alone in a lab should be avoided. To reduce the risks of working alone:
- Do not perform tasks by yourself that are not appropriate for working alone.
- Reduce the amount(s) of hazardous materials used.
- Always maintain clear access to emergency lab equipment like the safety shower, eye wash station and fire extinguisher.
- Check alarm systems, like oxygen sensors, frequently. If an alarm is activated, take action immediately.
- Implement a buddy system.
For unattended operations, additional precautions and alert systems may be necessary, but there are some general guidelines to follow.
- Laboratory lights should be left on.
- Label all containers and process equipment.
- Provide for containment of materials in the event of spills or failures.
- Signs should clearly identify the nature of the experiment and the hazardous substances in use.
- Make arrangements, if possible, for other workers to periodically inspect the operation.
- Post emergency numbers on the lab door or other easily noticeable location.
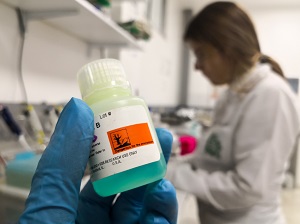