Safety isn't just something that you think about once a month at the mandatory HQ meeting. What is a JHA, why is it important and how often should it be done?
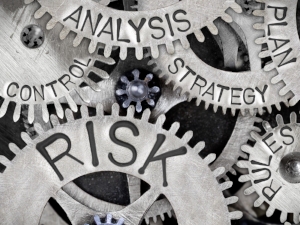
Job Hazard Analysis (JHA) is a way to help workers focus on accident prevention by writing down the steps, possible hazards, and controls for any specific job. A job hazard analysis can help workers and their supervisors find hazards before they turn into accidents.
When incidents occur, one of the first questions that will be asked, or should be asked, by the manager, the incident investigator, the OSHA representative (or whoever is asking questions...) is Can I see the JHA? By using this as a starting point for any incident investigation, it can be known if the workers were aware of the specific hazard, had planned how to prevent incidents from occurring on the job site, or if the crew even knew what a job hazard analysis is and why it's important.
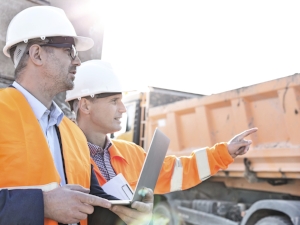
Job Hazard Analysis is sometimes called by different names including:
- Pre-Task Hazard Analysis
- Job Task Analysis
- Pre-Job Plans
- Job Safety Analysis (JSA)
- Pre-Task Planning
- Safety Task Analysis
A job hazard analysis is an exercise in detective work. The goal is to discover the following:
- What can go wrong?
- How can injuries happen?
- What would cause an accident to happen?
- How likely is it that the hazard will occur?
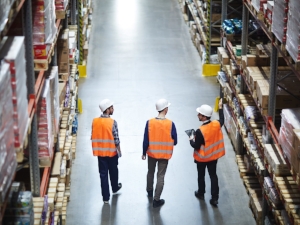
OSHA Standard Section 5(a)(1) Each employer shall furnish to each of his employees employment and a place of employment which are free from recognized hazards that are causing or likely to cause death or serious physical harm to his employees.
A specific work task can be separated into a series of simple steps. For each step hazards should be identified.

As steps required to complete a job or task are identified it is important to think about the types of hazards. Consider these common types of hazards and be sure they are included in the JHA:
- Struck Against or Struck By
- Contact With or Contact By
- Caught In, Caught On, or Caught Between
- Fall to Same Level or Fall to Below
- Overexertion or Exposure
More examples of tasks or hazards that lead to accidents include:
- Working at heights
- Slippery surfaces
- Exposed moving machinery parts
- Fires or explosions
- Noise
- Electricity
- Toxic Emissions
- Corrosive chemicals
- Low oxygen
- Repetitive tasks
- Heavy lifting
- Overhead work
- Rigging activities
- Use of heavy equipment
- Working with powder actuated tools
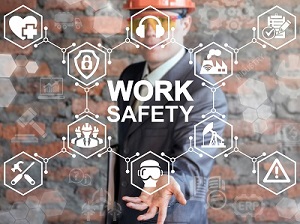
For each hazard written it is important to take the next step and write down a way to reduce, eliminate, or control the hazard. Consider these ideas as a few examples of safety controls:
- Are safety handles and guards for tools and equipment available?
- Can you move the work to ground level or prepare on the ground and lift it to a safe area?
- Are the right tools, materials and equipment being used?
- Is there a lift, or scaffold available instead of ladders?
- Are electrical or other power sources able to be switched off?
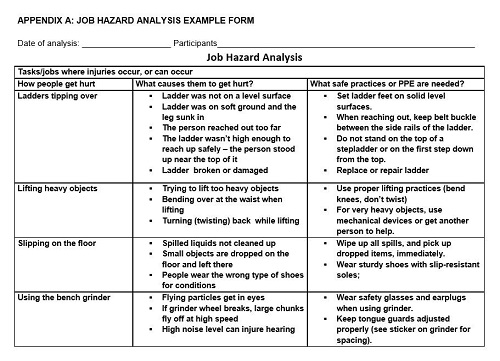
Remember these important tips when completing a Job Hazard Analysis (JHA):
- Job Hazard Analysis (JHA) is a way to help workers focus on accident prevention.
- Job Hazard Analysis is sometimes called by different names and many companies have their own forms and processes - the basic idea is to find hazards and prevent injuries.
- Workers and supervisors are the best sources for identifying hazards in the work they perform.
- For each step in a task the hazards should be identified, written down or checked off.
- Every hazard discovered has to have a safety control or accident prevention method written down.
- JHAs are often done at the start of a new job, and may be required daily.
- A few minutes used to write a good JHA can save hours or days lost to an injury.
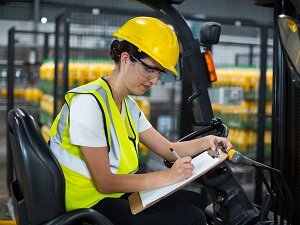