With the assumption that all workers have been trained and understand the horizontal directional drilling process and HDD equipment operations, this article provides reminders to ensure excavation teams keep a focus on safety at the drilling site.
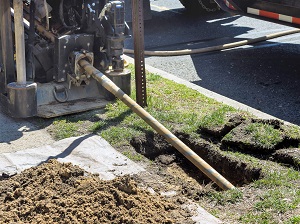
Horizontal Directional Drilling (HDD) is a trenchless technology that uses surface-launched equipment to drill underground horizontally and install pipes, conduits, and cables. HDD may be used where traditional vertical excavations are too hazardous, at sites with limited space, like dense, urban areas, and in industrial and residential areas.
Horizontal directional drilling projects always vary depending on the bore's diameter, the installation length, and individual worksite complexities such as physical features, weather, and industry type.
Although horizontal directional drilling can be a cost effective and environmentally friendly option (compared to traditional open trench excavations), it can be more difficult to avoid utility lines due to limited visibility. Potential hazards associated with HDD operations include struck-by and caught-in hazards from mechanical moving parts, as well as electrocution, fire and explosions from damaging electric and gas lines.
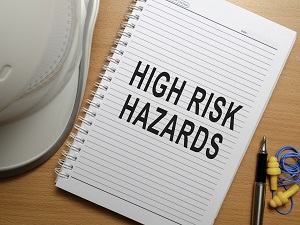
IMPORTANT TERMS TO KNOW:
Back Reamer: tool used for enlarging the pilot bore, and for pulling the utility line into the bore.
Bore: the extended underground cavity or hole created by the HDD process.
Casing: a pipe installed to stabilize a wider diameter bore after drilling.
Conduit: plastic piping installed in a bore to protect fiber optic cable or low voltage power lines.
Drill stem and head: metal rod and drill bit that convey rotational force, transmit drilling fluid into the bore, and excavate soil and rock while cutting the bore.
Potholing: method used to excavate small test holes from the surface to a buried utility line to expose its location. Techniques range from hand digging to using mechanical digging tools.
Reception Pit: excavation into which trenchless technology equipment is driven and recovered following the installation of the product pipe, conduit, or cable.
Tracking Device: a device used to track the boring progress along the drilling path using an electromagnetic field to detect the drill head.
Vacuum Excavator: a system used to dig potholes by high-pressure air or water to break up and vacuum soil and expose buried utility lines.
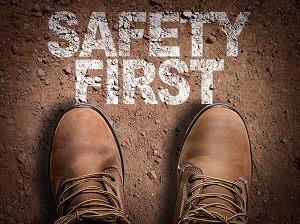
Verify placement of existing underground utility lines before drilling. Before any drilling occurs, contractors must use their state's utility location system. Always call 811, or the “Call Before You Dig” number in your area, to establish the location of underground utility lines in the work area. Additional steps in the identification process may include:
- Visually inspect the entire planned digging path for structures that indicate potential underground utilities, like gas meters and manhole covers.
- Review drawings, whenever possible, to verify underground utility locations.
- Compare findings with surface markings to identify any missed utility.
Underground utility lines can be difficult to identify because they might be covered by other lines, undocumented, buried at depths different from code requirements, and/or in a different position from initial installation due to ground settling.
Underground service locators typically cannot provide depth information for utility lines. Implement safe work practices, like potholing, to verify the depth of utility lines near the planned drill. It is important that potholes go to the planned drill path's depth, even if this is beyond the deepest known utility line, to identify any hidden lines. Potholing also allows the tracker to visually observe the drill stem and drill head during drilling to ensure that the HDD machine operator avoids striking utility lines along the drill path.
Workers should be able to identify a potential natural gas leak. Handheld natural gas detectors are most effective, but other indicators include:
- Dirt, water, or debris blowing from the ground into the air.
- An unusual sound, such as hissing, whistling, or roaring, near a natural gas line.
- Smelling a distinctive sulfur-like odor, which is typically added to natural gas, although some people cannot smell the odor. Note that not all gas is odorized, especially at large industrial sites, and may be impossible to smell.
Immediately contact local emergency responders (call 911) if excavation damage results in a natural gas release.
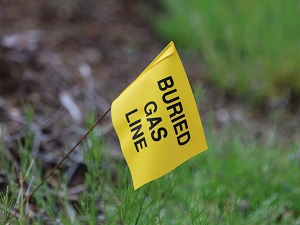
Drill at a pace that is slow enough to permit the tracking device to sense any drill line deflections caused by large obstructions. Trackers should check the tracking device readings frequently during HDD operations and compare them with the pre-operational walkthrough readings. If any changes in readings occur, like depth, the tracker should immediately signal the operator to stop drilling, investigate, and take appropriate safety precautions before continuing to drill.
Trackers will also be looking into the potholes to observe the drill stem as it passes near underground utility lines during drilling and guide the HDD machine operator along the bore path to avoid striking a line and the back reamer to verify that it follows the bore path and avoids utility lines.
Before drilling begins, the following safety precautions should be in place.
- Entry and exit drilling locations should be visibly marked or staked. A safe work area should be maintained in these areas.
- All overhead power lines have been identified and marked.
- A site-specific emergency action plan, as well as an effective traffic control plan, are both in place to protect workers, and have been well communicated to the entire team.
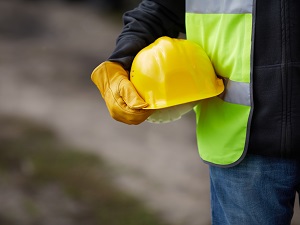
HDD machine operation requires technically skilled workers who understand the machine's complexities and safe work practices. Only trained and qualified personnel shall operate horizontal directional drilling machines.
OSHA Standard 1926.20(b)(4) The employer shall permit only those employees qualified by training or experience to operate equipment and machinery.
HDD machine operator safety recommendations include:
- Read, understand, and follow the directions and guidance provided in the operator’s manual.
- Wear appropriate PPE as required by the task and as required per OSHA regulations.
- Conduct a walk around inspection checking all fluids and noting any items needing maintenance and repair. Ensure all critical repairs are performed before operation.
- Be familiar with the work area.
- Remove debris and clutter in the cab that would prevent safe operation.
- Verify operation and accuracy of tracking equipment.
- Use 3 points of contact to enter the machine. Do not use any controls
- as handholds when entering or exiting the operator compartment.
- Check that controls are in proper settings before starting the machine.
- Only use approved methods and equipment to connect or disconnect
- components from the drilling system.
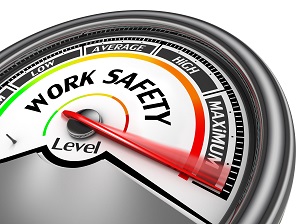