A thorough inspection of a fall protection body harness to ensure it is safe to use can be the critical difference between a routine task and a life-altering incident.
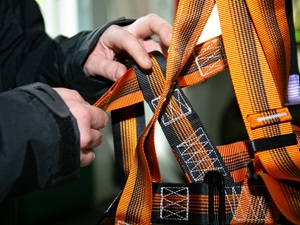
Types of personal fall protection harness inspections:
Initial Inspection
When you receive the harness from the manufacturer, perform a preliminary inspection to make sure it’s the right harness and does not have any defects. Confirm the model number, the size, the fit, and the condition.
Frequent Inspections
An inspection should be completed by the person who is going to wear the harness before every use. If the harness is shared, perform another inspection after the work is done to ensure it is safe to put back into rotation for the next person to use.
Periodic Inspections
A documented inspection of the harness that occurs at least once every 12 months is critical. Maintain records of these inspections. A third-party company may be performing the periodic inspection.
OSHA Construction Standard 1926.502(d)(21) Personal fall arrest systems shall be inspected prior to each use for wear, damage and other deterioration, and defective components shall be removed from service.
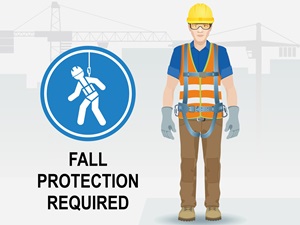
Inspect your full body harness before you use it, every time.
During the inspection confirm that:
- the ID tag is completely legible, labels are intact and readable
- all shoulder, chest, leg, and back straps are intact
- all hardware on the harness is in good condition and there are no defects, heat damage, weld damage, modifications, corrosion, cracks, breaks, or bends
- the nylon webbing is in good condition and does not have any heat damage, weld splatter, chemical damage, pulled stitching, crushed webbing, knots, cuts, snags, tears, or holes
- there are no torn, frayed, or broken fibers
- there are no pulled stitches or frayed edges
- there are no signs of heat or UV damage
- the buckles and adjusters work correctly, move freely, and are not deformed or cracked
- all grommets are secure, and all rivets are tight
- there are no additional punched holes in the harness
- the straps do not have excessive wear
- it is in good working order and no part of the harness is damaged
OSHA General Industry Standard 1910.140(c)(18) Personal fall protection systems must be inspected before initial use during each workshift for mildew, wear, damage, and other deterioration, and defective components must be removed from service.
YOU need to inspect your harness before you use it.
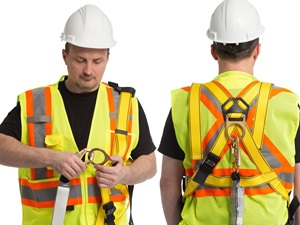
As you begin the inspection, start at the top of the harness. Examine the hardware first including the buckle and connection point. Make sure the hardware moves freely and is not defective. If you recognize any of these issues with the hardware, do not use the harness.
- defects, deformities, corrosion, or cracks on the D-ring, fasteners, adjusters, or other hardware
- missing or bent grommets or any grommets that are not fully secure (wiggling a bit in their place)
After inspecting the hardware, then inspect the straps and webbing of the harness. Use your hands to feel for heat damage while visually inspecting the harness at the same time. If you recognize any of these issues with the harness, do not use it.
- loose or frayed stitching
- worn or damaged straps or webbing
- foreign objects (staples, duct tape) adhered to the fabric
- damage from corrosives, chemicals, flames, or weld splatter
- any kind of cuts or holes, intentional or from wear
- fabric damage from paint or grease
During visual harness inspections, hold the components and also perform a “hand over hand” inspection. Grasp the webbing and bend it, checking both sides. This will create some surface tension making damaged fibers or defects easier to see. It is best to perform harness inspections without gloves so that you are able to feel the material.
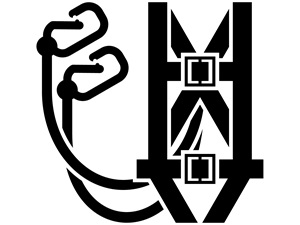
Labels must be visible and legible on personal fall protection equipment. If labels are unreadable, or have been removed, the equipment should be removed from service.
The manufacturer’s ID tag on a harness must display the manufacturer’s name, the unique serial number, the model number, the size, and the date of manufacture.
Some common reasons why a harness will not pass inspection are when the manufacturer’s tag is illegible, there is heat damage or UV damage on the harness, or there is writing in marker on the load-bearing webbing.
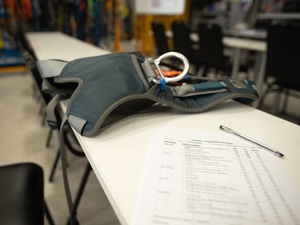
If a harness fails an inspection for any reason, even if you think it’s not a big deal, the harness should be removed from service, and tagged so that it is not used again before it can be repaired or replaced.
Do not write your name with a marker on the straps of the harness. This introduces a chemical onto the load bearing straps and it could fail inspection.
During the inspection if you see anything questionable… anything you are unsure of… do not wear it. Take it out of service. Do not risk it. Get it looked at by a competent person (a trained and qualified harness inspector) or replace it.
After a fall, the components of a fall arrest system, including the harness, should be removed from service. Follow the manufacturer’s instructions for inspection requirements before allowing any portions of the system to be allowed back into service.
Some parts of a fall arrest system, like the shock absorbing lanyard or retractable lifeline, will be returned to the manufacturer for recertification if they were involved in a fall or they may be destroyed.
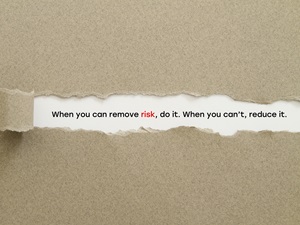