Using an Activity Hazard Analysis effectively is critical to identify, assess, and control jobsite hazards in a way that ensures a saferwork environment.
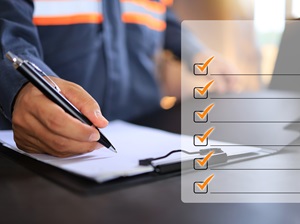
An Activity Hazard Analysis (AHA) is very similar to a Job Hazard Analysis (JHA). The primary goal of an Activity Hazard Analysis is to enhance workplace safety by systematically identifying and controlling hazards associated with specific tasks.
An Activity Hazard Analysis (AHA) is commonly associated with military projects and contracts, but its application extends even further. AHAs are now widely used across various industries as part of an organization’s overall risk management plan.
The purpose of an Activity Hazard Analysis is to:
- Identify Job Tasks: Break down the job into individual tasks to understand each component.
- Determine Hazards: Identify potential hazards associated with each task.
- Implement Controls: Develop and implement measures that will eliminate or minimize the identified hazards.
- Use as a Reference: Regularly review and use the AHA as a reference to ensure ongoing safety throughout the job.
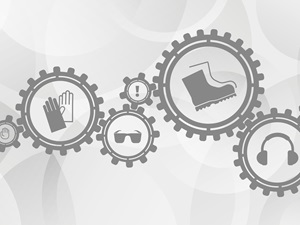
An Activity Hazard Analysis typically contains some or all of the following information:
Basic information about the project including the date(s), project name, contractor, activity type and location, and names of who prepared the AHA and who reviewed the document.
Job Steps involved and the sequence of work activities.
Potential Hazards associated with each job step.
Recommended Controls and precautionary actions to eliminate or minimize each hazard.
Equipment to be used during the work activities.
Training Requirements for personnel (example: equipment operator training).
Inspection Requirements for the equipment and work activities (example: inspect scaffold daily.)
PPE Requirements including the minimum PPE required for all job steps, and special PPE requirements for some job steps.
Competent and Qualified Person(s) and their areas of expertise.
An Activity Hazard Analysis may also have a Risk Assessment Code (RAC) Matrix that is used to assign a RAC to each job step.
A Risk Assessment Code (RAC) Matrix is a tool used to evaluate and categorize the level of risk associated with specific hazards identified during an Activity Hazard Analysis (AHA).
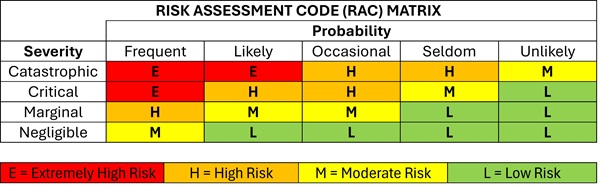
The RAC Matrix combines severity and probability to determine the overall risk level. The intersection of severity and probability in the matrix provides a risk code or rating, such as:
- Extremely High Risk: Do not proceed until risk is reduced to acceptable level.
- High Risk: Work may not begin until management agrees on safe course of action.
- Moderate Risk: Corrective action needed as soon as possible.
- Low Risk: Monitor and manage with routine procedures.
The RAC Matrix helps determine likelihood of potential accidents or incidents, allowing organizations to prioritize and implement appropriate control measures.
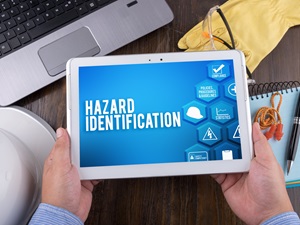
Conducting an Activity Hazard Analysis starts with systematically identifying job tasks, followed by a thorough review of potential hazards, and then the assignment of control measures.
First, break down the scope of work activity into job steps. List each job step in the order it is performed. Do not make the steps too generic or too detailed.
Identify the hazards for each step of the process and ask these questions:
- What can go wrong and what are the ways it could go wrong?
- What are the consequences if something does go wrong?
- How likely is it that something will go wrong?
- What contributing factors will increase the likelihood of something going wrong?
- What are the contractual and regulatory requirements associated with the hazard?
Be specific when identifying the controls that will be used to eliminate or reduce the hazards. For each hazard, there should be at least one control, but there may be more than one.
Consider the hierarchy of controls and always try to eliminate hazards. If elimination isn’t possible, substitution and engineering efforts should reduce the hazard, and administrative controls along with personal protective equipment can add further protection for workers.
Ensure that administrative controls include required work permits, inspections, and training. Be specific when identifying the type of required personal protective equipment.
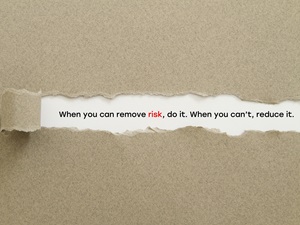
Utilizing an Activity Hazard Analysis (AHA) helps create a safer work environment by fostering a proactive approach to hazard identification and risk management.
An Activity Hazard Analysis is not just a corporate document but is intended to be created and used in the field.
Review the job steps, hazards, and controls listed on the AHA with workers who have performed the same tasks or have worked on a similar project to ensure that no items have been left out.
Before work begins, review the contract to ensure all conditions of the Activity Hazard Analysis have been met, including approvals of the completed AHA.
Keep a copy of the AHA at the job site during work activities. All workers must review the Activity Hazard Analysis before work begins.
The AHA should be reviewed and modified as necessary to address changing site conditions, operations, or any change to the competent persons.
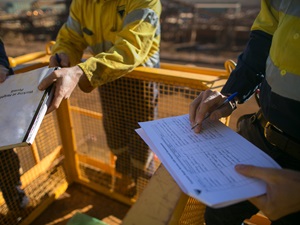