The Hierarchy of Controls is a framework for protecting workers from hazards that involves identifying, ranking, and implementing safeguards.
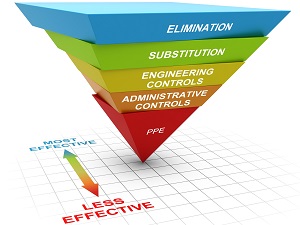
The Hierarchy of Controls is a method of identifying and ranking safeguards that protect workers from hazards. Often, implementing a combination of control methods will protect workers the best. To decide if a control is likely to work, it is necessary to understand how well it can protect workers and if it can be implemented successfully.
When evaluating control measures and trying to decide which ones to install or implement, consider whether the control measure is:
- Right for the hazard and appropriate for the risk
- Consistent with employer policies
- Not too burdensome to workers
- Recognized as an appropriate industry practice
- Effective, reliable, and durable
- Cost-effective in both the short-term and long-term
- Readily available
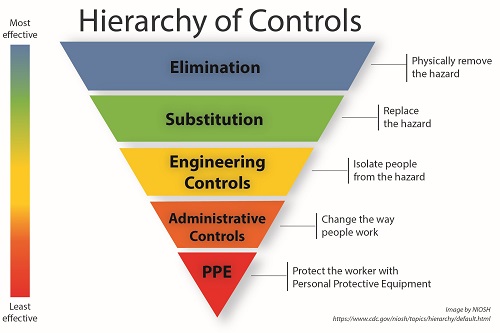
Elimination makes sure the hazard no longer exists. The best way to protect workers is to completely remove the hazard and eliminate exposure altogether.
Examples of elimination as a means to protect workers include ending the use of a hazardous material, doing work at ground level rather than at heights, or stopping the use of noisy processes.
Substitution means changing out a material or process to reduce the hazard. When considering a substitute, it’s important to compare the potential new risks of the substitute to the original risks. Effective substitutes reduce risk and do not create new hazards.
Examples of a workplace substitution might be switching out a hazardous material for a safer, less toxic chemical or switching to a process that uses less force, speed, temperature, or electrical current.
While elimination and substitution are the most effective control options and provide the greatest protection to workers, they can be more difficult to adapt into an existing process. These methods are best used at the design or development stage of a work process, when selecting new equipment, or when redesigning procedures.
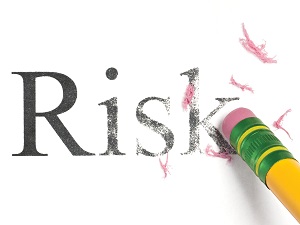
Engineering controls reduce exposure by preventing hazards from coming into contact with workers while still allowing workers to do their jobs. Modifying the equipment or the workspace to implement engineering controls may cost more upfront, when compared to administrative control efforts or PPE, but the long-term operating costs tend to be lower, especially when the protection is for multiple workers.
There are infinite examples of engineering safeguards that can be used including noise enclosures, local exhaust ventilation, a guardrail system, machine guarding, interlocks, and lift equipment.
Administrative controls change the way work is done or give workers more information by providing them with relevant procedures, training, and guidance. Often used together with higher-level safety precautions, administrative controls establish work practices that can reduce the duration, frequency, or intensity of hazard exposure.
Procedures like equipment inspections, planned preventive maintenance, checklists, work schedule adjustments, ensuring adequate rest breaks, and rotation of workers are all great examples of administrative controls. Training on topics like hazard communication, permit-required confined space entry, lockout/tagout, and safe work practices are also consider an administrative control because you are providing the necessary safety information to workers. A more immediate way that workers receive information is through the use of warnings like signs, backup alarms, smoke detectors, mirrors, horns, labels, and instructions, which are also all considered administrative controls.
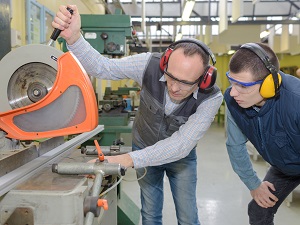
Personal Protective Equipment (PPE) includes clothing and devices to protect workers. Do not rely on PPE as the only control mechanism when higher-level safety precautions can be implemented to provide a greater degree of worker safety. When other control methods have been implemented but are unable to reduce the risk to a safe level, then appropriate PPE must be utilized.
Organizational management is typically aware of the types of personal protective equipment that may be required, but the list of PPE available is vast and includes safety glasses, goggles, face shields, personal fall protection systems, hardhats, gloves, work boots, respirators, hearing protection, protective clothing, and high-visibility safety apparel like safety vests.
Adding PPE requirements to a safety program requires more effort than just handing out safety vests or hardhats. A PPE program should be implemented that addresses issues like PPE selection, use, training, inspection, and replacement. PPE can be effective, but only when workers use it correctly and consistently.
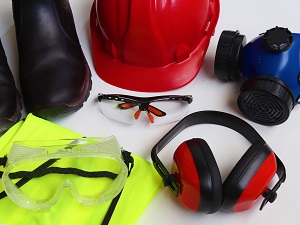
Using the hierarchy of controls to improve worker safety may take some time, resources, and collective brainstorming. Focus on one hazard at a time and start by considering all the different ways the hazard can either be eliminated or controlled.
Start at the top of the hierarchy and ask, Can this hazard be eliminated? Because eliminating the hazard is always the safest choice.
If the hazard cannot be eliminated completely, then continue down the list choosing one or more controls that will provide the maximum protection to keep workers safe. Always comply with any Federal, State, or workplace regulations which may require specific types of control for certain hazards.
Keep in mind that implementing new control measures can sometimes create additional risks. It’s critical that the new safeguards and processes are also evaluated using the hierarchy of controls and that any new hazards that have been introduced are adequately addressed.
If you are interested in applying the hierarchy of controls to your organization's hazard control efforts, download OSHA's guide to Identifying Hazard Control Options, a product of OSHA's Recommended Practices for Safety and Health Programs. This helpful document includes an easy-to-use worksheet (with examples!) that companies can use to plan out control methods for specific hazards in the workplace or on the jobsite.
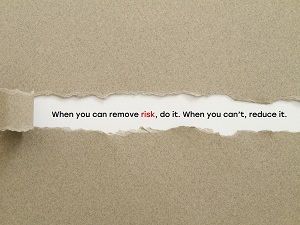