Applying general safety principles can help reduce incidents involving the moving, handling, and storing of materials. Workers should know and understand the potential hazards associated with material storage and how to control the worksite to minimize the danger.
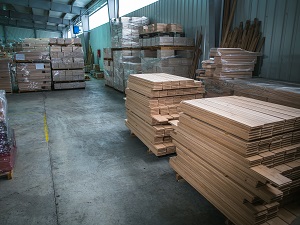
Stored materials must not create a hazard for workers. Consider factors such as the materials’ height and weight, how accessible the stored materials are, and the condition of the containers where the materials are being stored.
To prevent creating hazards when storing materials, it is important to keep storage areas free from accumulated materials that can cause tripping, fires, or explosions, or that may contribute to the harboring of rats and other pests.
OSHA General Industry Standard 1910.176(b) Storage of material shall not create a hazard. Bags, containers, bundles, etc., stored in tiers shall be stacked, blocked, interlocked and limited in height so that they are stable and secure against sliding or collapse.
When putting materials into storage, put bound material on racks when possible, or otherwise secure items by stacking, blocking, or interlocking them to prevent sliding, falling, or collapsing.
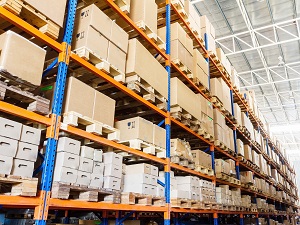
Storage areas should be kept neat, clean and orderly to eliminate hazards and conserve space. Material and supplies should never block access to emergency exits, fire extinguishers, fire alarms, fire hoses, or electrical panel boxes.
OSHA Construction Standard 1926.250(c) and General Industry Standard 1910.176(c) Storage areas shall be kept free from accumulation of materials that constitute hazards from tripping, fire, explosion, or pest harborage. Vegetation control will be exercised when necessary.
All passageways that workers use must remain clear of obstructions and tripping hazards. Workers should not store materials in excess of supplies needed for immediate operations in aisles. Do not store materials on scaffolds in excess of supplies needed for the immediate task.
To follow fire safety precautions, workers must understand that flammable and combustible materials must be stored according to their fire characteristics. Flammable liquids must be separated from other material by a fire wall. Combustibles must be stored in an area where smoking and using an open flame or a spark-producing device is prohibited. Dissimilar materials that are dangerous when they come into contact must be stored apart from each other.
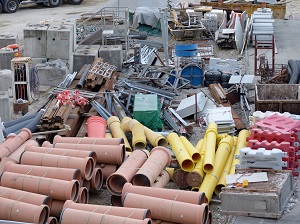
Unique safety precautions are required for the storage of hazardous materials. All chemicals and hazardous materials must be stored safely and securely, and away from forklift traffic areas. Drums containing hazardous liquids should be stored in a protected area out of the sunlight.
Safety Data Sheets (SDS) must be available for all chemicals that workers may be exposed to on the job and employees must follow the instructions on the SDS when handling chemical products.
Spill cleanup kits should be available in areas where chemicals are stored, and workers should know where to locate the written spill control plan. Workers must be trained to clean up spills safely including what PPE they should wear for cleanup and how to properly dispose of used materials.
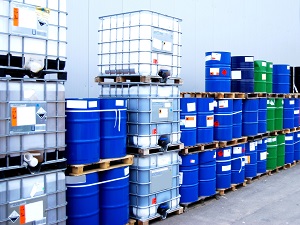
Compressed gas cylinders should be stored on a smooth floor in an upright position with the valve covers in place. All cylinders should be chained or fastened against a wall or stable surface to prevent displacement.
Different kinds of gases, especially those that are incompatible, should be stored separately. Empty cylinders should be stored in a location away from the full cylinders.
Traffic should be restricted in areas where compressed gas cylinders are stored.
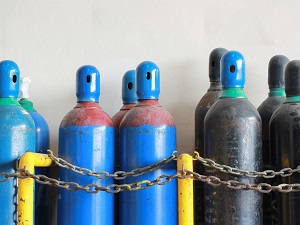
Steel storage racks or pallet racks are used to hold goods stacked on pallets. Every piece or component of pallet racking must be installed according to the manufacturer’s requirements.
The two most common causes of racking failures are 1) racking that is not installed properly and 2) damaged racking that is not reported or not repaired quickly.
Column or post guards help prevent impacts and protect uprights from damage that could result in catastrophic failures.
Inspect racks regularly to discover any damage, wear, or problems. Report any damage found on racks and ensure that repairs are made quickly. If necessary, unload racks, and then tag and mark or barricade them to remove them from service until repairs are completed.
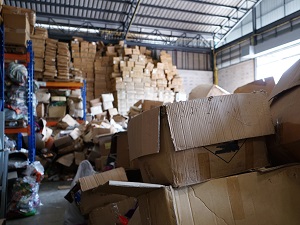
Consider the safety requirements of specific materials as they are handled and placed into storage.
Drums, barrels, and kegs should be stored symmetrically with planks, sheets of plywood dunnage, or pallets between each tier of drums, barrels, and kegs to make a firm, flat, stacking surface. If stored on their sides, block the bottom tiers of drums, barrels, and kegs to keep them from rolling.
Lumber should be stored in such a way that is stable and self-supporting with all nails removed. Store lumber no more than 16 feet high if it is handled manually, and no more than 20 feet if using a forklift.
Boxed materials should be banded or secured with cross-ties or shrink-wrap. Interlocking boxes will create a more stable stack. For stability, boxes can be placed on a pallet which will also make them easier to move.
OSHA Construction Standard 1926.250(a)(1) All materials stored in tiers shall be stacked, racked, blocked, interlocked, or otherwise secured to prevent sliding, falling or collapse.
Bags and bundles can be stored in interlocking rows to keep them secure.
Pipes and bars should be stored in racks or stacked and blocked to prevent spreading or tilting. Do not store pipes and bars in racks that face main aisles to avoid creating a hazard to passersby when removing supplies.
Baled paper and rags stored inside a building should be no closer than 18 inches to the walls, partitions, or sprinkler heads.
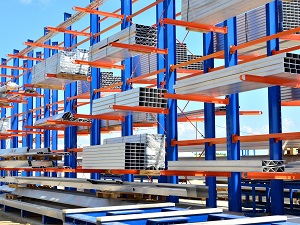