Automated Guided Vehicles, commonly known as AGVs, may be generally safer than manual forklifts, but safety precautions and worker safety are still critical.
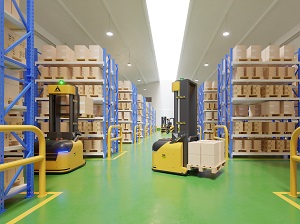
Automated Guided Vehicles, commonly known as AGVs, are portable robots that are typically designed to carry loads from one area to another. AGVs are not operated by people but instead use sensors to detect their intended path.
With industrial technology becoming more sophisticated, there are specifications that differentiate AGVs from similar equipment like powered industrial trucks and remote-control operated equipment.
Autonomous Mobile Robots, commonly known as AMRs, are often used in similar industrial settings as AGVs and utilize advanced technology that allows them to be more flexible in dynamic locations. As technology evolves, the industry may see hybrid or more advanced vehicles and robots emerge, with similar or different names.
Depending on the work environment, personnel safety precautions may be similar for AGVs and AMRs, but this article focuses on the safe operation and utilization of Automated Guided Vehicles. The Automated Guided Vehicles covered here are:
- self-driving.
- equipped with a collision warning sensor.
- able to navigate a pathway via sensors (or other technology) to complete tasks.
- capable of knowing the destination depending on the load it is carrying.
- not able to navigate around an obstacle but will instead stop until the obstacle is removed.
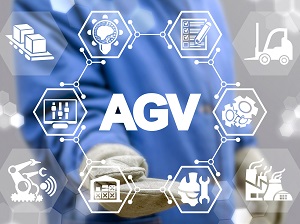
In addition to custom styles, there are four main types of AGVs typically used in industrial settings that can perform different functions.
- Tugger Automatic Guided Vehicles are wheel-based transport vehicles that can pull multiple non-powered vehicles with loads trailing behind it.
- Forklift Automatic Guided Vehicles are used to transport pallets but may also have standard manual forklift attributes. Some even have infrared sensors on the forks that are used for pallet interfacing.
- Unit Load Automated Guided Vehicles are mainly utilized to transport individual items like a coil of steel or an engine to another machine.
- Light Load Automatic Guided Vehicles are typically 500 pounds or less and travel around tight spaces with loads containing small parts, baskets, etc.
There are no specific OSHA standards for the robotics industry.
OSHA requirements for Powered Industrial Trucks (PIT), which covers forklifts that may be similar to industrial AGVs, are found in OSHA Standard 1910.178, but these requirements were written with an assumption that the vehicles would be manned.
The American National Standards Institute (ANSI) and the Industrial Truck Standards Development Foundation (ITSDF) have developed the Safety Standard ANSI/ITSDF B56.5 which covers Automatic Guided Industrial Vehicles.
While utilizing the ANSI/ITSDF B56.5 Standard, other industry guidelines and best practices that may cover AGVs, and manufacturer requirements, employers must remember that the OSHA General Duty Clause is always applicable.
OSHA General Duty Clause 5(a)(1) Each employer shall furnish to each of his employees employment and a place of employment which are free from recognized hazards that are causing or are likely to cause death or serious physical harm to his employees.
Comprehensive training is critical for all users responsible for the safe operation of AGV systems as well as all personnel that may be walking or working in the area where AGVs are operating. Personnel must receive training on the concepts of hazard zones and restricted areas of AGVs in order to be able to avoid the risks of these areas.
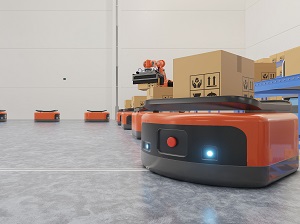
AGVs have the potential to cause injury if hazard zones and restricted areas in the work environment are not respected by personnel. AGVs may not be able to stop in time if an object or a person suddenly appears in their pathway unexpectedly.
ANSI/ITSDF B56.5-2019 4.3.2 Should an object suddenly appear in the path of the vehicle between the leading edge of the sensing field and the vehicle (i.e. an object falling from overhead or a pedestrian stepping into the path of a vehicle at the last instant), the vehicle shall initiate braking in accordance with brake system but may not be expected to stop in time to prevent contact with object.
Restricted areas of AGV operation must be clearly marked. In non-restricted areas, the floor space boundary required for the vehicle and its intended load and/or train shall be clearly marked, including the clearance necessary for turns and maneuvering.
Ensure blind corners have suitable audible and/or visual alarms to allow personnel to anticipate the approach of the AGV. Mirrors are also recommended in these locations. Signs, warning devices, and other safety devices should be used to alert and protect personnel from contact with the AGV, items moved by the vehicle, and any other equipment that interacts with the vehicle system.
Permanent aisles, roadways, and passageways utilized by the AGV should be clearly marked to warn personnel of potential AGV traffic and indicate that these vehicles have the right of way.
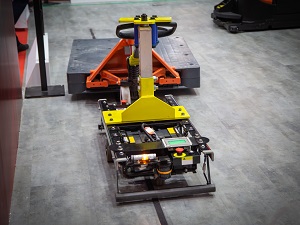
ANSI/ITSDF B56.5-2019 provides the following definitions:
- Guidepath – an intended path for the AGV
- Hazard Zone – an area of inadequate guidepath clearance with a max vehicle speed permitted of 1.2 m/s ≈ 2.6 mph
- Restricted area – an area of inadequate guidepath clearance with no escape route or an area of guidepath clearance which cannot be protected by object detection devices with a max vehicle speed permitted of 0.3 m/s ≈ 0.6 mph
- Very Narrow Aisle (VNA) Restricted Area – an area defined by fixed continuous racking and clearances of less than 0.5 m (19.7 inches) on both sides. Unauthorized personnel are prohibited from entering the area.
ANSI/ITSDF B56.5-2019 4.7.4 A minimum guidepath clearance of 0.5 m (19.7 inches) shall be maintained on both sides of the guidepath or on one side of the guidepath if the guidepath clearance on the other side is 0.1m (3.94 inches) or less to a continuous closed fixed structure (e.g. a wall). All other areas shall be considered hazard zones or restricted areas and be clearly marked by signs, stripes, lights, or other designations.
When walking or working in areas where AGVs may be operating, personnel should:
- Slow down and look carefully when walking around corners or coming up to a new aisleway.
- Listen for warning alarms.
- Remain a safe distance from AGVs in operation.
- Avoid distractions such as looking down at a cell phone or clip board or using headphones set at a high volume.
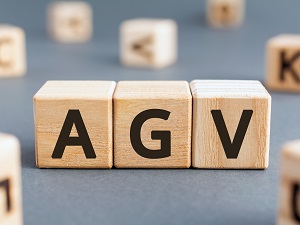
Automatic Guided Vehicles can cause injury or damage if improperly used or maintained. OSHA states that many robot incidents occur during non-routine operating conditions, such as programming, maintenance, testing, setup, or adjustment. Never manually override vehicle safety devices.
ANSI/ITSDF B56.5-2019 4.2.1 No modifications or alterations to an automatic guided industrial vehicle that may affect the capacity, stability, or safe operation of the vehicle shall be made without the prior written approval of the system supplier.
All nameplates, caution labels, instruction markings and any other tags or decals on the AGV that have been provided by the manufacturer must remain in place and legible.
Only authorized personnel are permitted to maintain, repair, adjust, and inspect vehicle systems. Follow all manufacturer’s recommendations for maintenance and inspection. Maintain records of all maintenance activities.
AGVs should only handle stable or safely arranged loads. Consider how changes to the load, load position, coupling type, position, floor surface conditions and battery weight may affect rated capacity and safe operation. Changes in weather, surface conditions or applications may affect vehicle stopping distance so speed, the load, brake settings, or operation may need to be adjusted accordingly.
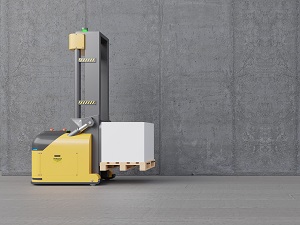