Effective controls (safeguards) protect workers from workplace hazards. Controls should minimize or eliminate safety and health risks with the ultimate goal of preventing injuries, illnesses, and incidents.
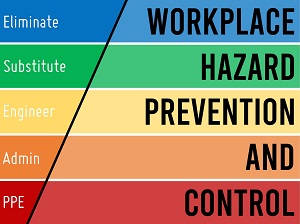
To effectively control and prevent hazards on the job, employers must go through the process of identifying hazards, selecting, and implementing one or more control methods, and then follow-up to ensure that those controls are working as they were intended.
The hierarchy of controls is a popular and effective tool that can be used to choose the safest methods of protection. When selecting control methods, it is always a wise decision to involve employees familiar with the work process who often have the best understanding of the conditions that create hazards and insights into how they can be controlled.
After hazards are identified, organizations can follow the steps outlined below to effectively select and implement control measures, develop a hazard control plan, and then evaluate how well those controls are actually protecting workers.
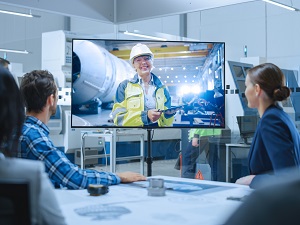
STEP 1 – IDENTIFY CONTROL OPTIONS
A wealth of information exists to help employers investigate options for controlling identified hazards. Before selecting any control options, it is essential to solicit workers’ input on their feasibility and effectiveness.
Review sources such as OSHA standards and guidance, industry consensus standards, NIOSH publications, manufacturers’ literature, and engineering reports to identify potential control measures. Keep current on relevant information from trade or professional associations.
Investigate control measures used in other workplaces and determine whether they would be effective at your workplace.
STEP 2 – SELECT CONTROLS
Select the controls that are the most feasible, effective, and permanent.
Eliminate or control all serious hazards (hazards that are causing or are likely to cause death or serious physical harm) immediately. Use interim controls while you develop and implement longer-term solutions.
Select controls according to a hierarchy that emphasizes engineering solutions (including elimination or substitution) first, followed by safe work practices, administrative controls, and finally PPE. Avoid selecting controls that may directly or indirectly introduce new hazards.
Review and discuss control options with workers to ensure that controls are feasible and effective. Use a combination of control options when no single method fully protects workers.
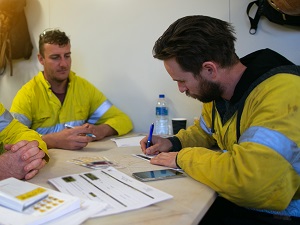
STEP 3 – DEVELOP A HAZARD CONTROL PLAN
A hazard control plan describes how the selected controls will be implemented. An effective plan will address serious hazards first. Interim controls may be necessary, but the overall goal is to ensure effective long-term control of hazards. It is important to track progress toward completing the control plan, and periodically (at least annually and when conditions, processes, or equipment change) verify that controls remain effective.
To create a hazard control plan:
- List the hazards needing controls in order of priority.
- Assign responsibility for installing or implementing the controls to a specific person or persons with the power or ability to implement the controls.
- Establish a target completion date.
- Plan how you will track progress toward completion.
- Plan how you will verify the effectiveness of controls after they are installed or implemented.
STEP 4 – IMPLEMENT THE CONTROLS
Once hazard prevention and control measures have been identified, they should be implemented according to the hazard control plan.
Implement hazard control measures according to the priorities established in the hazard control plan. When resources are limited, implement measures on a “worst-first” basis, according to the hazard ranking priorities (risk) established during hazard identification and assessment. Regardless of limited resources, employers have an obligation to protect workers from recognized, serious hazards.
Promptly implement any measures that are easy and inexpensive—such as general housekeeping, removal of obvious tripping hazards such as electrical cords, and basic lighting—regardless of the level of hazard they involve.
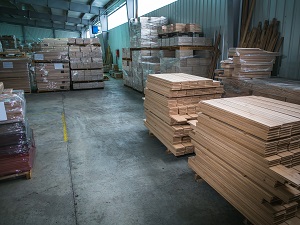
STEP 5 – CONFIRM CONTROLS ARE EFFECTIVE
To ensure that control measures are and remain effective, employers should track progress in implementing controls, inspect and evaluate controls once they are installed, and follow routine preventive maintenance practices.
Track progress and verify implementation by asking the following questions:
- Have all control measures been implemented according to the hazard control plan?
- Have engineering controls been properly installed and tested?
- Have workers been appropriately trained so that they understand the controls, including how to operate engineering controls, safe work practices, and PPE use requirements?
- Are controls being used correctly and consistently?
Conduct regular inspections and monitoring to confirm that engineering controls are operating as designed. Evaluate control measures to determine if they are effective or need to be modified. Involve workers in the evaluation of the controls.
If controls are not effective, identify, select, and implement further control measures that will provide adequate protection. Confirm that work practices, administrative controls, and PPE use policies are being followed. Conduct routine preventive maintenance of equipment, facilities, and controls to help prevent incidents due to equipment failure.
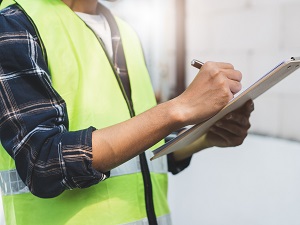
For more information on how to evaluate and improve your workplace safety and health program, download a copy of OSHA’s booklet Recommended Practices for Safety and Health Programs.