Guest Article written by Gregory Sanders of Crom Weld
Welding hazards are the same, whether you are running a small business or a big manufacturing company. Implementing proper safety measures protects not just the welders but anyone within the proximity of the workplace.
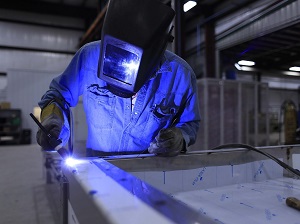
Whether you’re looking for the best welder for beginners or a robust welding machine fit for business use, the welding safety tips are interchangeable. Here are the 7 welding safety tips at the workplace to implement:
1. Provide The Manuals
Equipment comes with a manual, so it is essential for any welder operating the machine at the workplace to read the manual. It contains operating guides and information on how to maximize the machine’s output and safety measures.
In the event the manual is lost or damaged, contact the manufacturer for another copy. Fortunately, many manufacturers are now providing manuals online for easy access.
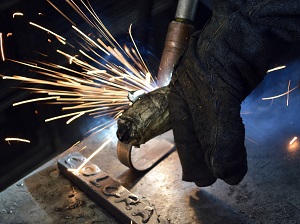
2. Carry Out Safety Training
While reading a manual is essential, it is equally important to ensure all designated employees receive training on the machinery's safe operations, including the supervisors.
Organizations like OSHA also carry out programs that educate students on hazards, precautions, the different types of welding, welding equipment, and the required PPE (personal protective equipment).
3. Provide the Right PPE
This includes gloves, boots, respirators, fire-resistant clothing, helmets, and ear protection to protect your employees from the welding hazards by providing them with the right PPE.
Ensure the welding helmets have side shields and the ideal shade of lens to protect the eyes and the face from arc flashes.
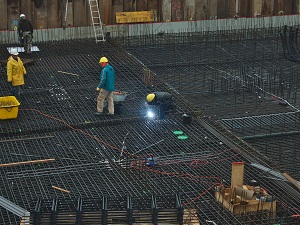
4. Proper Ventilation
The welding workplace must be well ventilated for the proper removal of airborne particles and gasses. Welding produces gases like nitrogen oxide, ozone, nickel oxides, carbon monoxide, and chromium, which are easy to penetrate the lungs when inhaled.
Inhaling these can lead to severe health problems like cancer, irritation of the lungs and throat, pneumonia, and asthma.
OSHA provides clear guidelines on ventilation requirements, such as the space needed between welders in any working space.
Depending on your company's working area, one ventilation strategy might not work. In this case, use multiple methods to ensure there's proper ventilation.
There are three main ventilation strategies:
- Local Exhaust Ventilation (LEV) is the most effective ventilation strategy for removing gases and fumes from welding. This method involves removal or the exhaustion of the fumes, vapors, dust, and gases before they can mix with the air in the working space. Some examples of LEV include a moveable hood, fume extraction welding guns, and a downdraft bench.
- Mechanical Dilution Ventilation - this uses roof exhaust fans and wall fans, or other mechanical strategies to keep airborne pollutants from entering the welding workspace.
- Natural Dilution Ventilation - it is the least effective strategy and involves the addition of fresh air into a working space through mechanical or non-mechanical methods.
Mechanical methods include opening doors and windows, while the non-mechanical method uses exhaust fans on the area's roof or walls.
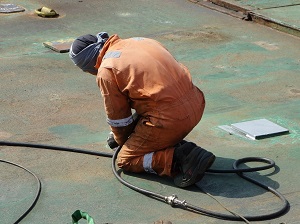
5. No Flammable Materials in the Workspace
Sparks, molten splatters, and heat will cause fires if they land on a flammable material. The workspace must have non-flammable materials, including the walls and other partitions. If the walls, roof, ceiling, or partitions are combustible, provide workers with fire-resistant shields.
These shields can also be used to cover any flammable content within the workspace that you cannot move when welding, especially when working in confined areas with limited spaces.
However, the work area must not have any clutter, regardless of how limited space you may have.
6. Adopt Boom-Mounted Feeders for Wires
Part of reducing clutter includes reducing the number of wire cables lying around the workplace. A simple trip can be hazardous, and boom-mounted wire feeders can help reduce this hazard.
Boom-mounted feeders will also save workers the time and energy needed to lift and move around with some of the welding equipment, which can be heavy. A boom moves up and down to about 60-degrees and rotates up to 360-degrees.
Also, it has a counterbalance feature that holds it in place when the welder sets the position.
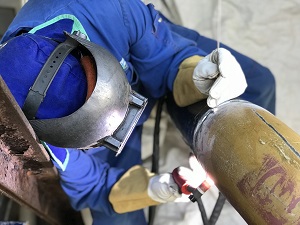
7. Fire Extinguishers and First-Aid Kits
Due to the high fire risks that come with welding, the workspace must have fire extinguishing and protection equipment strategically placed. The workplace must also have first aid kits available and easily accessible.
It is also essential to have all workers trained on using fire extinguishing equipment and steps to take if there is a fire, including performing first aid.
These welding safety tips are paramount for the protection of everyone in the workplace. Ensure everyone receives the necessary training and is aware of the hazards and the required safety measures.
Furthermore, we recommend putting together effective reporting structures where employers can report any safety concerns and offer recommendations.