In order to build, inspect, maintain, test, repair or decommission communication structures and equipment, professional technicians must know how to safely climb towers.
Some of the more frequently encountered hazards that tower climbers face include:
- falls from great heights
- inclement weather
- equipment failure
- structural collapse of towers
- electrical hazards
- falling objects
- fatigue
OSHA Standard 1910.268 covers safety and health standards that apply to the work conditions, practices, means, methods, operations, installations and processes performed at telecommunications centers and at telecommunications field installations, which are located outdoors or in building spaces.
The OSHA 1926 Construction Standard may also apply for construction, installation, and decommission work activities that occur on telecommunication towers.
Only trained and authorized workers are allowed to participate in tower climbing work activities! Tower climbers must receive extensive, specialized training before being allowed to climb towers.
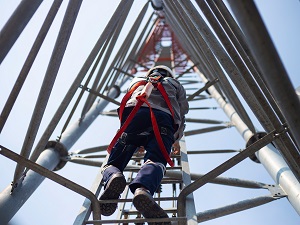
Because tower climbing is so physically and mentally demanding, preparation is key.
Inspect the work environment, including the structure and equipment, for any unsafe conditions. Report unsafe or questionable conditions to the site supervisor. Take appropriate measures to correct or minimize unsafe conditions.
Understand and follow all safety regulations. Anticipate environmental hazards and any other site hazards. Periodically inspect the site as the work progresses. Look for the safest, most effective path up the tower, become aware of any obstacles, and look for rest positions along the way.
Complete as much of the work as possible on the ground, before beginning your ascent. Secure any tools or other gear that will be carried up and down the tower.
When climbing, know your limits and conserve energy when possible. Use your legs to support your weight and pace yourself when climbing to prevent fatigue. Always maintain 100% tie-off while on the tower. Maintaining a good climbing form and rhythm can contribute to a safer climb and less fatigue.
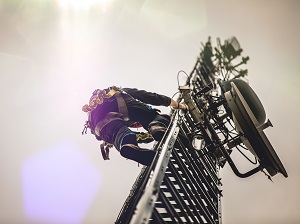
Tower climbers have a responsibility to properly wear, inspect, care for, clean and maintain their personal protective equipment (PPE), including personal fall protection.
OSHA Standard 1910.135(a)(1) The employer shall ensure that each affected employee wears a protective helmet when working in areas where there is a potential for injury to the head from falling objects.
PPE that may be required for most tower climbing jobs includes:
- hard hat
- approved eye protection
- gloves
- climbing boots with good arch support and a defined heel
- work positioning lanyard (fall restraint)
- full body safety harness
- energy absorbing lanyards (fall arrest)
- cable grab/robe grab
OSHA Standard 1926.100(a) Employees working in areas where there is a possible danger of head injury from impact, or from falling or flying objects, or from electrical shock and burns, shall be protected by protective helmets.
When not in use, always store PPE and fall protection equipment in an area that is clean, dry and free from exposure to fumes or corrosive elements.
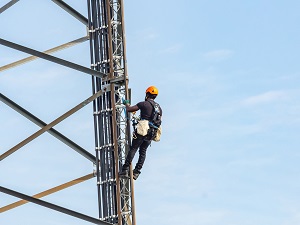
Many of the incidents that compromise safety involve situations where the tower technician was not properly tied-off to the structure. 100% tie-off is required at all times.
OSHA Standard 1926.502(d)(21) Personal fall arrest systems shall be inspected prior to each use for wear, damage and other deterioration, and defective components shall be removed from service.
Inspect personal fall arrest equipment before every climb and look for defects, such as:
- cuts, tears, abrasions, mold or undue stretching
- alterations or additions which might affect its efficiency
- damage due to deterioration or contact with fire, acids, or other corrosives
- distorted hooks, d-rings or faulty closures or locking devices
- tongues unfitted to the shoulder or buckles
- loose or damaged mountings
- non-functioning parts
- wearing or internal deterioration in the ropes
Check fall protection equipment for legible tags of service. Remove any harness from service if the tag is missing, illegible or the date on the tag has passed. Defective equipment should be tagged or marked as unusable or destroyed.
Tower climbers and ground crew employees should know how to report unsafe conditions and should follow the applicable reporting process whenever they discover unsafe conditions.
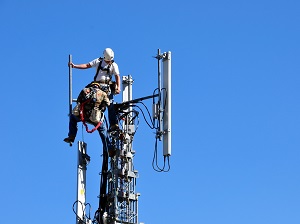
All work crews need to have and use proper safety equipment at all times. No work should be done if proper safety equipment is unavailable or the safety equipment available is not functioning properly. Work crews should promptly report issues with any safety device and cease operations if the safety device is compromised.
OSHA Standard 1910.268(g)(1) A positioning system or a personal fall arrest system shall be provided and the employer shall ensure their use when work is performed at positions more than 4 feet (1.2 m) above the ground, on poles, and on towers. The employer shall ensure that all climbing equipment is inspected before each day's use to determine that it is in safe working condition.
All employees make a commitment to “100% tie-off”. Job site supervisors need to have a firm commitment to enforcing 100% tie-off at every worksite at all times when employees are climbing.
All climbing work should include comprehensive safety planning, including a Job Hazard Analysis (JHA) and an Emergency Action Plan (EAP) for every job site. Work crews should not work at heights when weather conditions raise safety risks.
No member of a work crew should work at heights if their physical or mental health is impaired. For example, if a member of a work crew is taking medication that affects their physical abilities (such as over-the-counter cold and flu medication that can cause drowsiness), they should not climb or work at elevations.
Particular attention should be paid to inspections, including equipment inspections (such as inspections of tools, hoisting and rigging equipment, and other machinery) and inspections of personal protective equipment.
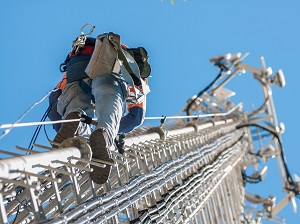