If safety precautions are not followed, workers who operate or work near skid-steer loaders are in danger of crushed-by, caught-in, rollover, and runover risks. When skid-steer loaders are used on site, workers must always:
- use and maintain all the safety devices provided by the manufacturer.
- safely enter and exit the loader.
- observe safe operating procedures.
- follow proper maintenance guidelines.
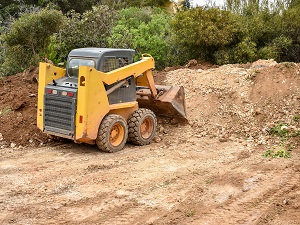
Only workers who are trained and authorized may operate a skid-steer loader. All workers at the job site must have training that allows them to work safely around heavy equipment.
OSHA Standard 1926.20(b)(4) The employer shall permit only those employees qualified by training or experience to operate equipment and machinery.
Do not operate heavy machinery if you are tired or have taken drugs or alcohol. If you are on medication, discuss with your medical provider to determine if you are capable of safely operating machinery.
Workers on foot at the job site should maintain a safe distance from heavy equipment, only use designated walkways, and wear high-visibility clothing, like safety vests.
Never modify, disable, override, or bypass the safety devices on any skid-steer loader.
Control Interlocks prevent unintentional control activation. These interlocked control systems require a safety device (like a seat belt or restraint bar) to be properly positioned before the operational controls can function. This feature ensures that the operator is safely seated away from the zone of the lift arm movement before the machine can be operated.
Seatbelts must be functioning, properly maintained, and used by the operator.
Rollover Protective Structures (ROPS) keep the operator inside the loader during rollover incidents.
Side Screens (metal or glass) are integrated with the ROPS to prevent the operator from leaning or reaching out of the operator’s compartment and coming into contact with a moving lift arm. Side screens also protect operators from being injured by debris or objects entering the cab.
Falling Object Protective Structures (FOPS) are provided to protect the operator from being struck by falling material.
Lift Arm Supports secure the lift arms in the raised position. Never work under a raised attachment unless the lift arm support device is in place. Never use concrete blocks or simple metal angle irons because they can shift or collapse under even light loads.
Workers can be crushed by moving parts if they do not enter and exit the cab of the skid-steer loader safely. To prevent injuries when getting into and out of the loader, workers must mount and dismount safely. Enter and exit when the bucket (or other attachment) is flat on the ground or when the lift arm support device is in place. When entering the loader, face the seat and keep a three-point contact with handholds and steps. Never use foot or hand controls as steps or handholds. Keep all walking and working surfaces, on and near the loader, clean and clear of debris.
Before leaving the operator’s seat lower the bucket (or other attachment) flat on the ground, set the parking brake, and turn off the engine. If the operator is unable to exit through the primary opening for entering the machine, they should use the emergency exit located at the back of the operator’s compartment or as specified by the manufacturer.
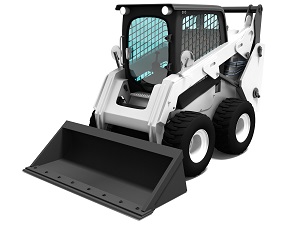
If you operate or work near skid-steer loaders, always follow safe operating and job site procedures. Never exceed the manufacturer’s recommended load capacity for the loader.
Operate the skid-steer loader only when properly positioned inside the operator’s compartment. NEVER operate the loader or attempt to activate the loader’s controls from outside the cab.
If a seat belt or restraint bar is provided, ensure it is engaged during operation. Always stay seated when operating the loader controls. Do not leave the operator’s seat while the engine is on. Keep all body parts inside the operator’s compartment during operation.
Load, unload, and turn the loader on level ground, when possible. Carry the load low. Travel and turn with the bucket in the lowest position possible. Do not travel across slopes. Travel straight up or down, with the heavy end of the loader pointed uphill. Avoid slippery surfaces. Operate loaders on stable surfaces only. Always look in the direction of travel.
Keep bystanders a safe distance away from the work area and NEVER carry riders.
OSHA Standard 1926.21(b)(2) The employer shall instruct each employee in the recognition and avoidance of unsafe conditions and the regulations applicable to his work environment to control or eliminate any hazards or other exposure to illness or injury.
Make sure that the seat belt is secured around the operator whenever the operator is in the seat of the skid-steer loader. The seat belt protects the operator in several ways. In the event of a rollover, the seat belt restrains the operator within the protective envelope of the ROPS. The seat belt can also protect the operator from falling out or being jostled into the operating zone of the lift arm and bucket. If the seat belt is part of the interlocked control system, it protects workers from being caught and crushed between the lift arm and frame.
If side screens, interlocks, ROPS/FOPS, and seat belts are not on the machine, contact the equipment dealer or manufacturer’s representative about the availability of field modification kits or replacement parts.
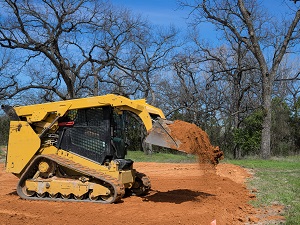
When equipment such as a skid-steer loader is used in construction activities, construction employers must develop safety and health programs that provide for frequent and regular inspections by competent persons of 1) the job sites, 2) materials, and 3) equipment.
A routine maintenance and inspection program should be followed that aligns with the manufacturer’s recommendations. Inspect the skid-steer loader to ensure that all safety systems are functioning properly prior to operating the equipment. Keep the foot controls free of mud, ice, snow, and debris.
Maintenance work should be performed when the engine is turned off, the key removed, the parking brake set, the wheels blocked, and attachments lowered or supported by an approved lift arm support device.
There are many attachments available that may be used on a skid-steer loader including buckets, backhoes, augers, chippers, trenchers, and pallet forks. Always ensure the attachment on the loader has been mounted correctly.
OSHA Standard 1926.20(b)(2) [Accident prevention] programs shall provide for frequent and regular inspections of the job sites, materials, and equipment to be made by competent persons designated by the employers.
Ensure that all the safety features on the loader are properly maintained. Never operate heavy equipment, like a loader, in which safety systems have been modified or are not working properly. Equipment with modified or malfunctioning safety systems should be taken out of service until they are repaired or replaced.
Never work on the machine with the engine running unless directed to do so by the operator’s manual. Follow the manufacturer’s safety recommendations to complete the task. If the adjustments require that the engine be in operation, use an additional person and work as a 2-person team with a trained operator properly positioned in the operator’s station who can effectively communicate with the worker making the adjustment.
If the skid-steer loader is not equipped with a lift-arm support device or it is damaged, contact the equipment dealer or manufacturer’s representative for help in determining proper support procedures or for replacement parts.
Although workers and employers may perceive safety features such as interlocked controls and seat belts as obstacles to efficient machine operation, bypassing these devices increases their risk of serious injury and death.
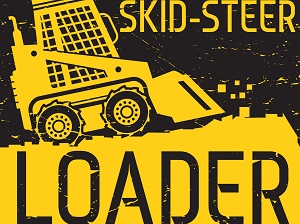
The current OSHA regulations for the construction industry do not specifically address skid-steer loaders but they do, however, require employers to protect workers from hazards associated with operating and maintaining mobile machines and heavy equipment.
While OSHA does not have a standard requiring employers to use control interlock systems or seatbelts on skid-steer loaders, it is important for employers to understand that under the General Duty Clause employers must provide their employees with a workplace free from recognized hazards likely to cause death or serious physical harm. OSHA may cite an employer for a violation under the General Duty Clause if recognized hazards exist and the employer does not take feasible, effective measures to abate such hazards.
OSHA General Duty Clause Each employer shall furnish to each of his employees employment and a place of employment which are free from recognized hazards that are causing or are likely to cause death or serious physical harm to his employees.
If skid-steer loaders are used in situations covered by OSHA’s general industry standards, then the requirements of OSHA’s Control of Hazardous Energy (lockout/tagout) standard 1910.147 may be applicable. Such situations may include, but are not limited to, use of skid-steer loaders in warehousing operations or servicing and maintenance performed on skid-steer loaders in maintenance facilities.
