Making your workplace a safer working environment is important for any business. American author Annie Dillard said, “How we spend our days is, of course, how we spend our lives.”
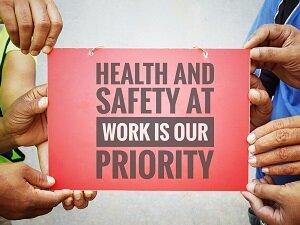
Most people spend much of their day at work. Approximately eight to ten hours a day. That’s a lot of hours at work. No matter what your job is, it is crucial to feel safe at your job.
An organization that values its staff guarantees their safety.
When staff know their work environment is safe, they wake up energized and happy. They are ready to conquer the world for you.
There are legal obligations that organizations must follow to meet the safety requirements.
When staff don’t feel safe at work, it affects many aspects of an organization. These include:
- Performance - workers don’t reach their potential.
- Productivity - there is low production and reduced innovation at work.
- Company image - the organization bears a negative image.
- Turnover - workers lose morale and there is a high rate of staff turnover
- Availability - increased absenteeism from work.
- Loyalty - the workers are disloyal.
- Cost - the organization incurs more costs through high insurance premiums.
And many more.
This need not be your organization’s story. These five practical ways guarantee your workplace is a safe working environment.
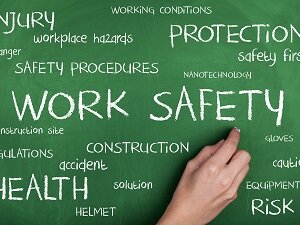
1. Offer Training Programs on Safety
Workplace safety is not only the responsibility of the employer. Employees also have a role to play.
To make them aware of this, you need to educate them.
“Education is the most powerful weapon which you can use to change the world.”- Nelson Mandela
Many people hear about work injuries all the time, but they get the impression these only happen elsewhere. As a result, they are casual and complacent until an accident occurs.
Offer general training to all your staff about the potential risks at work. Let them know how to protect themselves from these risks.
Later, give specialized training to the staff dealing with specific equipment.
Don’t make the training a one-off. Technology, employees and even regulations are not static, neither should you. Seek out for every available opportunity to offer regular training.
Some of these include:
- When hiring new staff
- When existing staff need refresher training
- When there is a change in management
- When you introduce new equipment at work
- When staff take up new roles
- When staff return to work after a long leave of absence, such as maternity or paternity leave
- When you notice the need for retraining
Besides the training, give all staff a company safety and emergency guideline manual.
Back up your training with regular safety meetings. During these meetings, let the staff have an open dialogue and ask questions.
Use peer-to-peer learning. It is effective. This is where staff learn from each other as opposed to learning from a trainer or instructor.
Let the training be interactive. Don’t lecture and have practical examples related to your industry. When you engage adults, they learn best.
Assign them roles. For example, they can role-play different scenarios on work safety and how to respond. This goes a long way in imparting a safety attitude to them.
From time to time, review your training methods and material so it remains relevant.
You may consider incorporating online training. It is cost-effective and offers flexible learning.
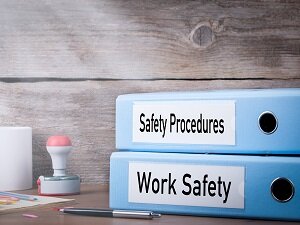
2. Get Rid of Potential Hazards
A serious organization wants to make its staff comfortable. As a standard, it ensures workers have the right tools at work.
These include work equipment and protective work wear. It is a basic step to ensuring your staff is safe as they work.
Further, the organization seeks ways to remove potential hazards at work. It is difficult to do so if you are not aware of them.
Create a system of identifying hazards. You can begin by carrying out a job hazard analysis.
What is a job hazard analysis?
This is a technique that focuses on a job task to identify a hazard before it occurs. Once identified, you can take practical steps to rectify the situation. You can either remove or reduce the hazard to an acceptable risk level.
It’s also important to review reports that show injuries, accidents and close calls at work. Look out for common patterns among these. Therein lies the hazards.
Once you have identified the hazards through the reports, prioritize them in the order of:
- Likelihood of it causing a serious injury
- Whether you can fix it in the short term or long term
Then come up with a plan of action to address these.
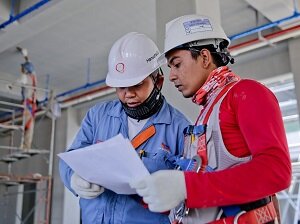
3. Carry Out Regular Inspections
Regular inspections are important and need to be the norm in the organization. This is not solely the work of a manager.
Invite experts to do inspections from time to time. They may notice something you have overlooked.
Make your staff accountable by assigning them the responsibility of inspection.
Let them have a routine inspection of all equipment and work wear before work starts. Follow up with random inspections to be sure they are following all protocols.
As a habit, keep your staff informed on work injury statistics on a monthly basis. It makes them safety-conscious all the time.
After inspection, set a clear system for reporting safety-related issues. For example, let staff report when machines break down. Also, let them report and record all injuries, close-calls, hazards, and illnesses.
When staff report safety issues, take immediate action. Investigate and repair machines as soon as possible. Failure to do so can cause staff to be complacent in their reports. They may feel that the organization does not listen to their grievances.
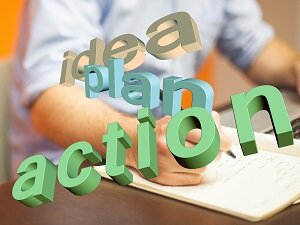
4. Lead By Example
In an organization, everyone should own the process of safety. That also includes management. Their support and commitment are key.
Let them lead by example. A good way to show this is by getting them involved in every step of the safety process.
For example, many times people don’t take training with the seriousness it deserves. To enforce this, let the management announce the training dates. They can do it through an official company memo.
All staff should lock out the day from any other activity. When you say it is compulsory, everyone should be in attendance, including management.
Leaders who lead by example walk the talk. They dedicate time and resources for workplace safety.
Use staff who uphold safety standards as peer influencers. Reward them in public and make them safety ambassadors at work.
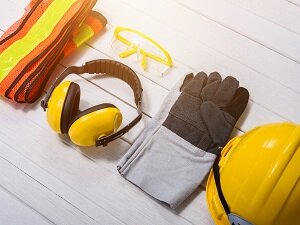
5. Provide Proper Safety Gear and Work Wear
Proper work wear and safety gear is an essential component of your company’s safety plan.
Personal protective clothing can help protect your staff in the execution of their tasks and duties.
Typically the protective gear will cover delicate areas of the body such as hands and feet as well as the skull and face.
Particles in the air such as wood shavings and dust can also pose health risks when inhaled or when they become lodged in the eyes. Glasses and face masks may be required depending on your organization.
It is essential that any work wear or safety gear fits the employee perfectly. This will prevent clothing from getting caught on sharp corners or in dangerous machinery.
Men and women have different needs when it comes to the size and shape of their work wear, avoid the mistake of trying to implement a one-size-fits-all approach to uniforms.
Find a provider that offers affordable and high-quality work wear. A rental company that also provides laundry service will keep your uniforms in excellent condition and will help reduce the risk of injury as a result of muck and grime covering the reflective paneling on your employees’ work wear.
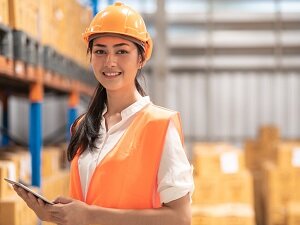
A Comprehensive Guide to Warehouse Safety provides more detailed information on keeping employees safe in warehouse working environments. Check it out!
Above All
Always ensure your staff’s well-being and safety is at the top of your priorities as a business.
Besides being the right thing to do, placing health and safety-first results in desirous effects for your business.
These benefits include, but are not limited to: fewer accidents, reduced absenteeism, higher productivity, and reduced risk of legal action.