Analyzing and addressing root causes during an incident investigation can help an organization prevent similar incidents from recurring.
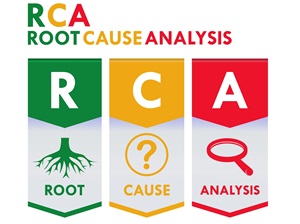
A root cause is a fundamental, underlying, system-related reason why an incident occurred that identifies one or more correctable system failures.
During an incident investigation, an organization must determine which factors contributed to the incident. A root cause analysis can uncover the underlying or systemic, rather than the generalized or immediate, causes of an incident. Correcting only the immediate cause may address the symptom, but not the underlying problem.
Incident investigations are often conducted by a supervisor, but to be most effective, these investigations should include managers and employees working together, since each brings different knowledge, understanding, and perspectives to the investigation.
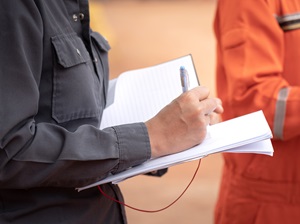
A successful root cause analysis identifies all root causes because there is often more than one.
According to OSHA, root causes generally reflect failings in workplace design, equipment maintenance, organizational and cultural factors, operating systems and procedures, staffing, management, and training.
Organizational culture and behavior may come up as a contributing factor during a root cause analysis. Companies that foster a strong safety culture can significantly reduce the likelihood of incidents.
A root cause analysis can also occur after a near miss. If an incident almost-happened once, it can almost-happen again and that indicates that corrective and preventive action is likely necessary. A root cause analysis can help determine what actions to take to ensure that near miss doesn’t turn into a catastrophic event in the future.
Addressing underlying or root causes is necessary to understand why an incident or near miss occurred, to develop effective corrective and preventive actions, and to minimize or eliminate serious consequences from similar future incidents.
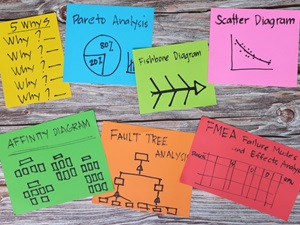
There are many tools the incident investigation team can use to conduct a root cause analysis. Ideally, a combination of these or other tools will be used.
- Brainstorming
- Checklists
- 5 Whys Analysis
- Logic/Event Trees
- Timelines
- Sequence Diagrams
- Causal Factor Determination
For simpler incidents, brainstorming and checklists may be sufficient to identify root causes. For more complicated incidents, consider using logic/event trees. Timelines, sequence diagrams, and causal factor identification are often used to support the logic/event tree tool.
There are also a variety of software tools on the market now that can assist with and enhance the efficiency and accuracy of the root cause analysis.
Regardless of the combination of root cause analysis tools that are chosen, use them to answer four important questions:
- What happened?
- How did it happen?
- Why did it happen?
- What needs to be corrected so it doesn’t happen again?
Considering human factors such as fatigue, cognitive overload, and human error can be valuable during the analysis. While these are likely not root causes themselves, they can significantly contribute to understanding the underlying issues as the investigation digs deeper to answer the questions of what went wrong and why.
Interviews and review of documents, such as maintenance logs, can be useful during the incident investigation. Involving employees in the root cause investigative process, and sharing the results of those investigations, will also go a long way toward preventing future similar incidents.
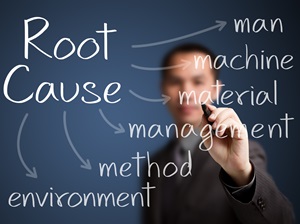
Every accident investigation is a fact-finding process. The investigation should focus on identifying root causes, not finding fault or assigning blame to an employee.
Simple conclusions like “employee failed to follow the procedure” cannot be provided as the root cause of an incident. It is important to dig deeper, for example:
- Why was the procedure not followed?
- Was training inadequate?
- Is the procedure out of date?
- Does management demand deadlines are met at the expense of safety?
For example, if the procedure is out of date and not sufficient for the current workflow, the investigation can recommend the corrective action to update the procedure and provide training to workers on the new procedure.
Then the investigation should go even further by asking: Why was the procedure out of date? Perhaps a preventive action might be to implement a review process of operating procedures on a defined periodic basis (example: annually) to ensure safety requirements are continuously updated.
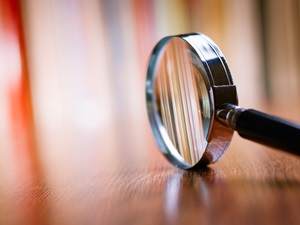
Conducting a thorough investigation that identifies root causes will help to prevent similar events from happening again and reduce the risk of future injuries, property damage, and fatalities. Incorporating root cause analysis into a continuous improvement process, with regular reviews and updates, can further enhance its effectiveness and ensure ongoing safety improvements.
By using root cause analysis to prevent similar events, companies can avoid unnecessary costs resulting from business interruption, emergency response and clean-up, increased regulation, audits, inspections, and OSHA fines.
A robust safety program that includes root cause analysis along with all incident investigations can result in more effective control of hazards, improved process reliability, increased revenues, decreased production costs, lower maintenance costs, and lower insurance premiums.
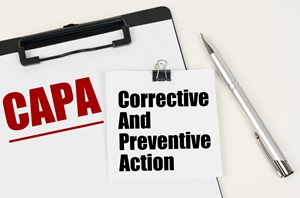