Find out how adding regular safety meetings and toolbox talks to your safety program ensures your company meets many of the OSHA safe workplace requirements.
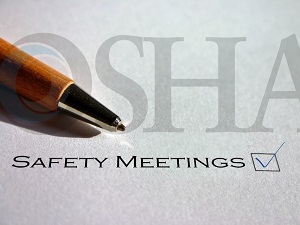
OSHA requires that every employer make safety and health a top priority and ensure a safe working environment. OSHA's job is to provide leadership and encouragement to employers to take that responsibility seriously and provide educational or awareness opportunities to employees so they know of their rights to a safe workplace.
Employers have a duty to protect workers from injury and illness on the job by developing and implementing a safety and health program. According to OSHA, there are five components that every effective safety program should have.
- Management Leadership and Employee Participation
- Workplace Analysis
- Hazard Prevention and Control
- Safety and Health Training and Education
- Program Evaluation
Holding regular safety meetings, like on-site toolbox talks or tailgate meetings or longer pre-shift all hands safety meetings, can satisfy many requirements for most of these components.
Management Leadership and Employee Participation
Employer and employee involvement and communication on workplace safety is essential. To foster this positive communication, OSHA recommends that employers show their commitment by investing time, effort and money in the safety program and hold safety meetings that focus on employee safety and health.
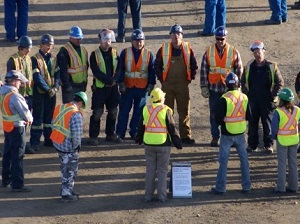
Workplace Analysis
Employers and employees must participate to identify and eliminate existing or potential hazards in the workplace. In addition to having an adequate system for reporting hazards, by implementing regular safety meetings, this will provide a casual forum for employees to speak up regarding potential workplace hazards. During safety meetings employees should be free to add to the dialogue of the meeting, report current hazards, and discuss potential solutions as a team.
Hazard Prevention and Control
After hazards are identified, it is important that employees follow safe working procedures. Regular safety meetings should be held on topics such as:
- How to regularly and thoroughly maintain equipment
- Review of the hazard reporting procedure
- Reminders of the hazard correction procedures
- PPE requirements and proper PPE wear, use and maintenance
- Safe work procedures for the current work performed
- Health safety like cold stress, heat stress, asbestos, lead, etc.
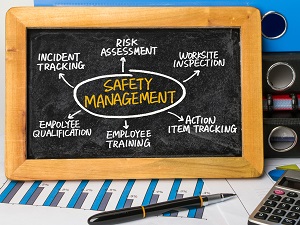
Safety and Health Training and Education
It is important that every employee receive proper and adequate training to ensure they are able to safely and competently perform their jobs. This also applies to temporary, part-time and contract employees. Regular safety meetings should be documented and attendance should be recorded. In addition to on-the-job (OTJ) and compliance training, safety meetings provide a valuable safety training mechanism on a more regular basis to teach and remind all employees of daily safety awareness and hazard prevention.
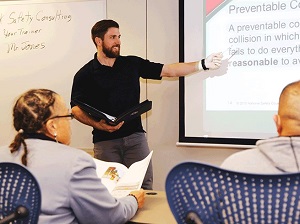
To get answers to common questions about safety meetings like what should be covered, how long should they last, and how often should you have safety meetings, visit this popular article on Toolbox Talks.
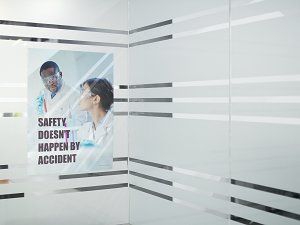