ISO 45001 is the International Standard for Occupational Health and Safety (OH&S) and is the world’s first international standard that covers health and safety at work. The ISO 45001 standard offers a single, clear framework for all organizations wishing to improve their safety performance.
Directed at the top management of an organization, ISO 45001 aims to provide a safe and healthy workplace for employees and visitors. To achieve this, it is crucial to control all factors that might result in illness, injury, and in extreme cases death, by mitigating adverse effects on the physical, mental, and cognitive condition of a person – and ISO 45001 covers all of those aspects.
ISO 45001 is not required. It is a global consensus standard with which companies can voluntarily choose to comply. It is not a legal requirement.
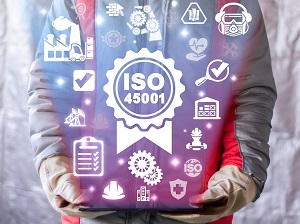
ISO stands for International Organization for Standardization. Because 'International Organization for Standardization' would have different acronyms in different languages (IOS in English, OIN in French for Organisation Internationale de Normalisation), the organization founders decided to use the acronym ISO as the standardized short name. ISO is derived from the Greek 'isos', meaning equal. Whatever the country, whatever the language, they are always referred to as ISO.
ISO, founded in 1947, is an independent, not-for-profit, non-governmental international organization with a central office based in Switzerland. One standards organization per country is allowed to be a member of ISO, and for the United States that member is the American National Standards Institute, commonly known as ANSI.
ISO brings together experts to share knowledge and develop international standards that provide solutions to global challenges. Today ISO has 23,934 international standards covering almost all aspects of technology and manufacturing. The short publication ISO in Brief provides more information on the organization, why international standards are important, and how ISO works.
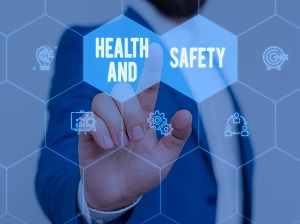
An international standard is a document containing practical information and best practices. It often describes an agreed way of doing things.
ISO standards help:
- Make products compatible so they fit and work well with each other.
- Identify safety issues of products and services.
- Share good ideas and solutions, technological know-how and best management practices.
The ISO standard for health and safety in the workplace was released in March 2018 and is called ISO 45001, Occupational Health and Safety Management Systems – Requirements with Guidance for Use.
The primary purpose of implementing an OH&S management system, like ISO 45001, is to prevent fatalities, injuries, and illnesses. Other benefits include:
- better management of safety and health risks
- identification of additional opportunities to improve safety management
- reduced cost of insurance premiums
- an improved approach to incident investigation
- a more cooperative culture for greater worker engagement and empowerment
- pursuing positive safety initiatives that are compatible with business priorities
- improvements in product, process, and service quality
- reinforced leadership commitment to proactively improve safety performance
- an increase in workplace morale
- reduced absenteeism and staff turnover, leading to increased productivity
- ability to meet legal and regulatory requirements
- a more favorable image and reputation (among customers, suppliers, and the community)
In this free brochure, ISO 45001 - Occupational Health and Safety, learn more about ISO’s international standard for occupational health and safety and what it can do for your organization.
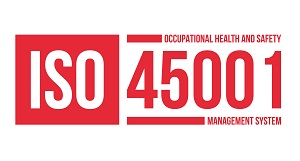
All ISO management systems use the same, simple concept: Plan, Do, Check, Act. This is often referred to as the PDCA cycle. Here is the way that the PDCA cycle relates to ISO 45001:
- Plan what the organization needs to do to prevent workplace illnesses and injuries and then plan how that will be accomplished.
- Do what was planned to prevent workplace illnesses and injuries.
- Check how well the safety processes that were implemented are working.
- Act to fix problems and look for ways to make what the organization is doing even more effective to protect workers.
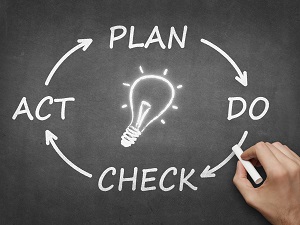
ISO 45001 is applicable to all organizations, regardless of size, industry, or nature of business. It is designed to be integrated into an organization’s existing management processes and follows the same high-level structure as other ISO management system standards, such as ISO 9001 Quality Management and ISO 14001 Environmental Management.
Certification to ISO 45001 is not a requirement of the standard but can be a useful tool to demonstrate that you meet its criteria. An organization can adopt some or all of the ISO 45001 standard to establish or improve their safety program. Simply having a formal management system in place will bring many benefits of its own through enforcing best practices. Certification is merely an added endorsement that demonstrates to external parties that you have achieved full compliance with a specific standard, but it is not required.
Work-related injuries, illnesses or fatalities are always difficult for any kind of organization, but the negative effects for small businesses can be overwhelming. This handbook, ISO 45001: A Practical Guide for Small Businesses, published jointly by ISO and UNIDO, aims to help smaller economic units implement the requirements of ISO 45001. Readers will get simple explanations and practical examples that support their first steps into the intricacies of workplace health and safety.
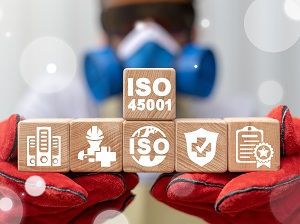
ISO 45001 enables organizations to achieve their safety goals as it provides for:
- continual improvement of OH&S performance.
- fulfilment of legal and other requirements.
- achievement of OH&S objectives.
- integration of other aspects of health and safety, like worker wellness and wellbeing.
ISO 45001 does not address issues such as product safety, property damage, or environmental impacts. It is specifically focused on worker safety, and the safety of others who may be impacted by the organization’s activities.
ISO 45001 may be particularly beneficial for companies that participate in international trade. Seeing that a partner company is ISO 45001 aligned or certified provides information with respect to how they value safety. It also demonstrates to customers and the public that the organization values employee safety, which can improve public perception and increase business opportunities.
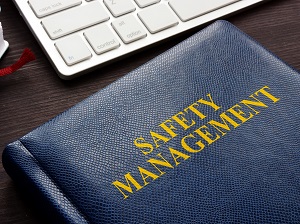
If ISO 45001 is not the right fit for your organization, other standards, guidelines, and models are available to help establish or improve your safety and health program.
- OSHA Recommended Practices for Safety and Health Programs is always a great start for any organization. The idea is to begin with a basic program and simple goals and grow from there. If you focus on achieving goals, monitoring performance, and evaluating outcomes, your workplace can progress along the path to higher levels of safety and health achievement.
- ANSI/ASSP Z10 Occupational Health and Safety Management Systems defines requirements for an occupational health and safety management system (OHSMS) and provides flexibility in how to conform to the requirements of the standard in a manner appropriate to each organization.
- OSHA Voluntary Protection Programs (VPP) recognize employers and workers who have implemented effective safety and health management systems and maintain injury and illness rates below national Bureau of Labor Statistics averages for their respective industries. To participate, organizations must submit an application to OSHA and undergo a rigorous onsite evaluation. VPP participants are re-evaluated every three to five years and are exempt from OSHA programmed inspections while they maintain their VPP status. If recognition is important, VPP may be a good choice. Note: some organizations participating in VPP base their safety programs on OSHA’s Recommended Practices, ANSI/ASSP Z10, or ISO 45001.
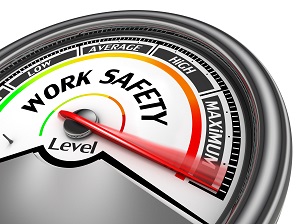