Any organization that has hazardous chemicals is use in required by OSHA’s Hazard Communication Standard (HCS) to implement a hazard communication program. The program must include labels on containers, safety data sheets (SDSs), training for workers, and a written version of the program.
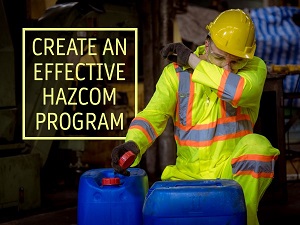
Companies can implement an effective workplace hazard communication program by following these steps:
REVIEW THE STANDARD AND ASSIGN RESPONSIBILITY
Read over OSHA’s Hazard Communication Standard 29 CFR 1910.1200 and become familiar with the requirements. Most of the rules for employers will be found in sections (e) through (h) of the standard. You must become familiar with these requirements to determine what is needed for compliance in your workplace.
Assign someone on staff, or a committee, the primary responsibility for coordinating implementation. In order to ensure that you have an effective hazard communication program, and address all of the necessary components, it’s important that someone be in charge of the overall coordination efforts.
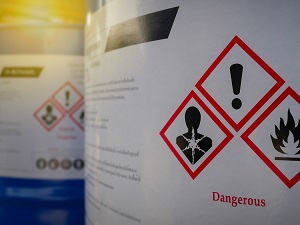
CREATE A WRITTEN HAZARD COMMUNICATION PROGRAM
Prepare a written plan to indicate how hazard communication will be addressed in your facility. This written plan must lay out how the organization will address the requirements of labeling, safety data sheets, and employee training.
The written program also requires employers to maintain a list of the hazardous chemicals known to be present in the workplace, so along with the written program, prepare a list or inventory of all hazardous chemicals in use or in storage at the worksite(s).
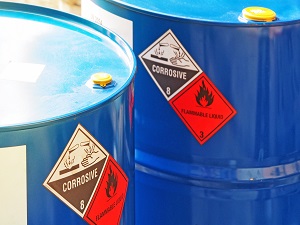
ENSURE CHEMICAL CONTAINERS ARE LABELED
Employers are required to ensure that hazardous chemical containers are labeled. At a minimum, these labels should include the product identifier and general information concerning the hazards of the chemical.
Chemical manufacturers and importers are required to provide labels on shipped containers. As long as these labels are compliant, you can keep these labels on the hazardous chemical containers.
Alternatively, or in addition to, you can label chemical containers with other compliant labels from third-party systems which could be the National Fire Protection Association (NFPA) or the Hazardous Materials Identification System (HMIS).
Whichever method is utilized, workers must have access to the complete hazard information for any chemicals in their work environment.
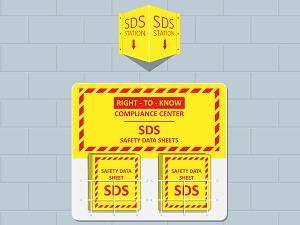
MAINTAIN EASY ACCESS TO SAFETY DATA SHEETS (SDS)
Safety data sheets (also known as an SDS) are the source of detailed information on a particular hazardous chemical. An SDS must be on file for each hazardous chemical in the workplace. If you do not receive an SDS from your supplier automatically, you must request one.
Safety data sheets must be readily accessible to employees. Workers must be able to reference any SDS in their work area during their work shift. Some worksites keep all the SDSs in a binder in a central location that can be accessed by all workers, and other organizations provide the SDSs electronically in a computer system that all employees can access.
No matter which system is used, employees must be trained on how to use the system to view the SDSs and have the ability to obtain paper copies of any SDS they need. Also, in the event of a medical emergency, a paper copy of any SDS must be immediately available to medical personnel, so keep that in mind when designing your SDS access system.
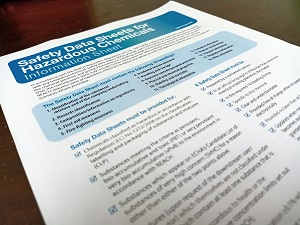
PROVIDE TRAINING TO WORKERS ON HAZARDOUS CHEMICALS
Train employees on the hazardous chemicals in their work area before initial assignment, and when new hazards are introduced. During training, review the requirements of the standard, the hazards of the chemicals, appropriate protective measures, and where and how to obtain additional information on the chemicals.
Workers must understand when and how they may be exposed to hazardous chemicals during the course of their workday and how they can protect themselves. Remember, all safety training must be conducted in a manner and a language that workers can comprehend.
For more information on how to create a HazCom program for your organization, OSHA has put together a comprehensive booklet to reference: Small Entity Compliance Guide for Employers That Use Hazardous Chemicals.
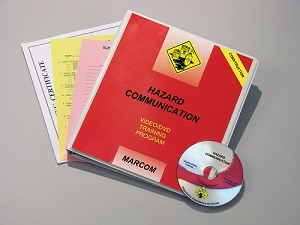