The U.S. HazCom standard (HCS), that now matches the international HazCom standard (GHS), is better for businesses and creates a safer work environment for employees.
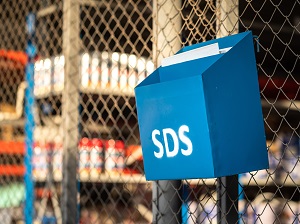
OSHA’s Hazard Communication Standard (HCS) is now aligned with the Globally Harmonized System of Classification and Labeling of Chemicals (GHS). When OSHA made this update to the HCS in 2012 they enacted a universal and easier-to-understand approach to classifying chemicals and communicating hazard information on labels and safety data sheets (SDS).
HAZARD COMMUNICATION AT WORK
Manufacturers have a responsibility to classify chemicals by their hazardous properties, label the chemicals, and prepare a safety data sheet (SDS).
Importers and Distributors should ensure that they have proper labels for the chemicals they handle along with the appropriate safety data sheets.
Employers create a written hazard communication program, ensure all hazardous chemicals are labeled, and prepare a list of the hazardous chemicals in the workplace.
Employees should know where they can access safety data sheets for the chemicals found in the workplace and participate in training on chemical hazards and protective measures.
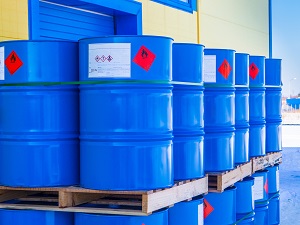
When referring to hazard communication, or HazCom, there are several acronyms and abbreviations that are often used, and sometimes it can get confusing. Here are the basics:
GHS, Globally Harmonized System, An international hazard communication standard that OSHA used as a foundation when updating the U.S. Hazard Communication Standard.
HCS, Hazard Communication Standard, OSHA Standard 1910.1200 that requires that the information concerning hazardous chemicals are communicated to workers. Per 1926.59, this standard also applies to construction work.
HazCom, Hazard Communication, the act of providing safety information about hazardous chemicals that are used or found in a workplace.
HazMat, Hazardous Material, any material or substance that would be a danger to health, safety, property, or the environment if it is released without precautions. Example characteristics: explosive, corrosive, flammable.
HAZWOPER, Hazardous Waste Operations and Emergency Response, OSHA guidelines specific to clean-up work when workers may be exposed to hazardous waster materials.
SDS, Safety Data Sheet, The document that provides detailed information on a a specific hazardous material. Previously known as MSDS, Material Safety Data Sheet.
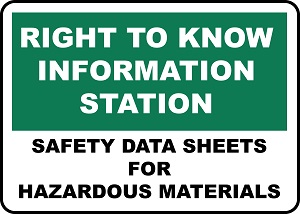
Workers have the right to know and understand the hazardous properties of the chemicals in the workplace to which they may be exposed. Workers also have the right to all pertinent information that will enable them to work with or around such chemicals in a safe manner.
OSHA Standard 1910.1200(h)(1) Employers shall provide employees with effective information and training on hazardous chemicals in their work area at the time of their initial assignment, and whenever a new chemical hazard the employees have not previously been trained about is introduced into their work area.
The Hazard Communication Standard (HCS), that aligns with the international standard (GHS), has key requirements that help to ensure chemical safety in the workplace.
Chemical manufacturers and importers are required to evaluate the hazards of the chemicals they produce or import and prepare labels and safety data sheets (SDS) to convey the hazard information.
When a workplace or jobsite has hazardous chemicals, those materials must be identified with proper labels and safety data sheets (SDS) must be readily available for workers.
Workers must be trained on the safe ways they are expected to handle hazardous materials. Employee training must include information on the hazards of the chemicals in their work area and the measures to be used to protect themselves.
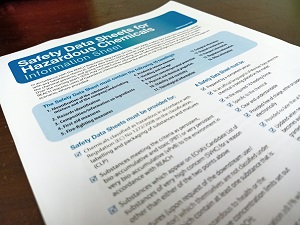
Workers who handle chemicals or are in a work environment where chemicals are used, have a right to know the dangers of those chemicals.
Employees should be trained on how to read an SDS. Because all Safety Data Sheets are written in the same manner, once employees are trained on how to read the document, they should be able to understand any SDS.
OSHA Standard 1910.1200(g)(8) The employer shall maintain in the workplace copies of the required safety data sheets for each hazardous chemical and shall ensure that they are readily accessible during each work shift to employees when they are in their work area(s).
There are 16 required sections that can be found on every SDS, that provide information on the hazardous chemical including 1) what it is, 2) what are the hazards, and 3) how do you prevent the hazards from becoming dangerous and how do you protect yourself from those hazards.
The Hazard Communication Standard (HCS) requires that Safety Data Sheets be in a uniform format so that each of the 16 sections are always in the same order to ensure that employees reading the document can quickly get the information they need. SDSs must be readily accessible to employees.
The SDS format is the same as the ANSI standard format which is widely used in the U.S. and is already familiar to many employees.
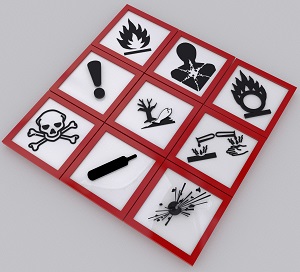
The Globally Harmonized System (GHS) and the Hazard Communication Standard (HCS) require universal pictograms to be displayed on labels to alert users of the chemical hazards to which they may be exposed.
The GHS (international standard) has 9 pictograms that are used on hazardous products. OSHA’s HCS requires 8 of these pictograms on hazardous chemical labels. The Environment pictogram is non-mandatory because environmental hazards are not within OSHA's jurisdiction.
Each pictogram consists of a symbol on a white background framed within a red border and represents a distinct hazard or set of hazards. Workers should become familiar with these images and the hazards they represent.
Labels on hazardous chemical containers must remain legible and should not be defaced or removed.
For specific information on what each pictogram looks like and what hazards they represent, visit OSHA's QuickCard 3491 on GHS Pictograms.
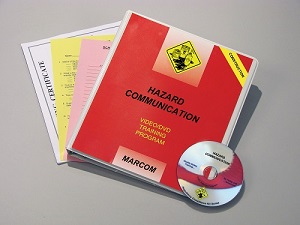