The main goal of any safety and health program is to prevent workplace injuries, illnesses, and deaths, as well as the suffering and financial hardship these events can cause for workers, their families, and employers. Sounds ideal in theory, but how can organizations actually make this happen?
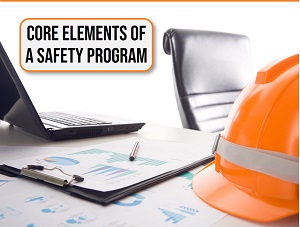
Traditional approaches to workplace safety often use a reactive approach when problems are only addressed after a worker is injured or becomes sick, a new standard or regulation is published, or an outside inspection finds a problem that must be fixed. When resources like time and money are stretched thin, this may seem like the only way to handle things, but in reality, finding and fixing hazards before they cause injury or illness is a far more effective approach that also ends up saving time, money, and heartache in the long run.
OSHA has a lot of great advice when it comes to adopting a proactive approach to workplace safety and health. The idea is to begin with a basic program and simple goals and grow from there. If you focus on achieving goals, monitoring performance, and evaluating outcomes, your workplace can progress along the path to higher levels of safety and health achievement.
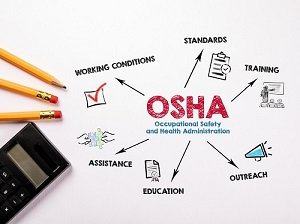
Establishing a safety and health program is one of the most effective ways of protecting your most valuable asset: your workers. Losing workers to injury or illness, even for a short time, can cause significant disruption and cost—to you as well as the workers and their families. It can also damage workplace morale, productivity, turnover, and reputation.
OSHA’s Recommended Practices present a step-by-step approach to implementing a safety and health program, built around seven core elements that make up a successful program.
Employers will find that implementing these recommended practices also brings other benefits. Safety and health programs help businesses:
- Prevent workplace injuries and illnesses
- Improve compliance with laws and regulations
- Reduce costs, including significant reductions in workers' compensation premiums
- Engage workers
- Enhance their social responsibility goals
- Increase productivity and enhance overall business operations
While the action items under each core element are specific, they may not apply to every organization exactly as they are written here. The process should be tailored to the needs of the company.
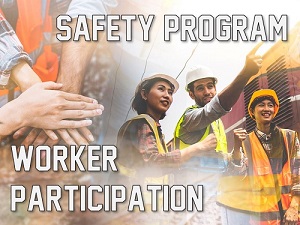
MANAGEMENT LEADERSHIP
Effective management leadership, when it comes to workplace safety, means that the leaders of the organization behave in a positive way that promotes health and safety throughout the company.
- Top management demonstrates its commitment to eliminating hazards and to continuously improving workplace safety and health, communicates that commitment to workers, and sets program expectations and responsibilities.
- Managers at all levels make safety and health a core organizational value, establish safety and health goals and objectives, provide adequate resources and support for the program, and set a good example.
WORKER PARTICIPATION
When it comes to worker participation, this means that the employees are truly involved in establishing, operating, evaluating, and improving the safety and health program. All workers should participate, including those employed by contractors, subcontractors, and temporary staffing agencies.
- Workers are involved in all aspects of the safety and health program—including setting goals, identifying and reporting hazards, investigating incidents, and tracking progress.
- All workers, including contractors and temporary workers, understand their roles and responsibilities under the program and what they need to do to effectively carry them out.
- Workers are encouraged and have means to communicate openly with management and to report safety and health concerns or suggest improvements, without fear of retaliation.
- Any potential barriers or obstacles to worker participation in the program (for example, language, lack of information, or disincentives) are removed or addressed.
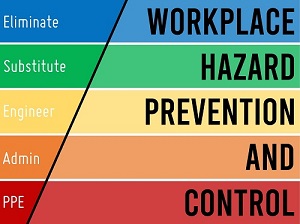
HAZARD IDENTIFICATION AND ASSESSMENT
A critical element of any effective safety and health program is a proactive, ongoing process to identify and assess hazards that have the potential to cause injuries, illnesses, or incidents.
- Procedures are put in place to continually identify workplace hazards and evaluate risks.
- Safety and health hazards from routine, nonroutine, and emergency situations are identified and assessed.
- An initial assessment of existing hazards, exposures, and control measures is followed by periodic inspections and reassessments, to identify new hazards.
- Any incidents are investigated with the goal of identifying the root causes.
- Identified hazards are prioritized for control.
HAZARD PREVENTION AND CONTROL
Effective hazard controls (safeguards) protect workers from workplace hazards. Controls should minimize or eliminate safety and health risks with the ultimate goal of preventing injuries, illnesses, and incidents.
- Employers and workers cooperate to identify and select methods for eliminating, preventing, or controlling workplace hazards.
- Controls are selected according to a hierarchy that uses engineering solutions first, followed by safe work practices, administrative controls, and finally personal protective equipment (PPE).
- A plan is developed that ensures controls are implemented, interim protection is provided, progress is tracked, and the effectiveness of controls is verified.
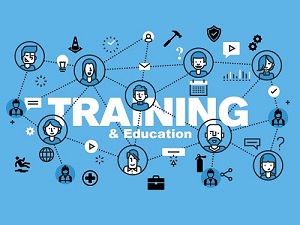
TRAINING AND EDUCATION
Training and education are important tools for informing workers and managers about hazards and controls so they can work more safely and be more productive. Another role of training and education, however, is to provide workers and managers with a greater understanding of the safety and health program itself, so that they can contribute to its development and implementation.
- All workers are trained to understand how the program works and how to carry out the responsibilities assigned to them under the program.
- Employers, managers, and supervisors receive training on safety concepts and their responsibility for protecting workers’ rights and responding to workers’ reports and concerns.
- All workers are trained to recognize workplace hazards and to understand the control measures that have been implemented.
MULTIEMPLOYER WORKSITES
At multiemployer worksites, it is imperative that general contractors, contractors, subcontractors, and staffing agencies collaboratively engage in ensuring equal safety and health protection for all employees, communicating on-site hazards, setting qualification standards, and coordinating work planning to preemptively address potential safety or health conflicts.
- General contractors, contractors, and staffing agencies commit to providing the same level of safety and health protection to all employees.
- General contractors, contractors, subcontractors, and staffing agencies communicate the hazards present at the worksite and the hazards that work of contract workers may create on site.
- General contractors establish specifications and qualifications for contractors and staffing agencies.
- Prior to beginning work, general contractors, contractors, and staffing agencies coordinate on work planning and scheduling to identify and resolve any conflicts that could impact safety or health.
PROGRAM EVALUATION AND IMPROVEMENT
Periodically, employers should assess their safety and health program to make sure it is working as intended and achieving the goals set by the organization. If there are any areas that need improvement, they should be fixed which then drives the continual improvement of the safety and health program.
- Control measures are periodically evaluated for effectiveness.
- Processes are established to monitor program performance, verify program implementation, and identify program shortcomings and opportunities for improvement.
- Necessary actions are taken to improve the program and overall safety and health performance.
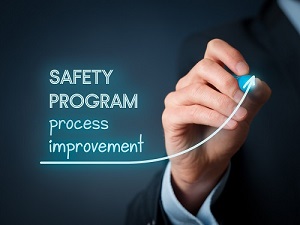
For more information about these recommended practices, tools to help you implement them, and related topics, visit OSHA’s website dedicated to safety management. This page includes links to many tools and resources developed by OSHA and others that can help employers and workers implement these recommended practices. OSHA will continue to update and add to this resource list.
If these recommended practices appear challenging, take a look at our 10 Steps for Safety article first. There you will find some simple steps your organization can take to start building an effective safety program. Completing those 10 steps first will give you a solid base from which to take on some of the more structured actions presented in the recommended practices listed above.
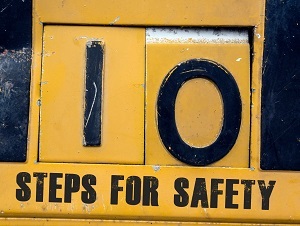