Workers often perform a variety of tasks where they could be exposed to harmful dust, chemical vapors, fumes from molten metal, and particulates from grinding, painting, or sandblasting. Although the best method to protect workers is first using engineering controls such as ventilation systems, it is not always a feasible solution. In these situations, the use of a respirator may be required to ensure the maximum amount of protection and safety is provided to the worker.
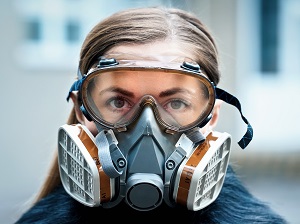
The use of respirators, even simple ones like dust masks, is serious and requires workers to understand the types of hazards they could be exposed to, the specific type of respirator needed, how to use the respirator, and its limits. Failure to follow all the requirements to properly wear a respirator can prove to be dangerous and potentially deadly.
NOTE: The respiratory protection standards for Construction are the same as for General Industry set forth in Standard 1910.134.
OSHA Standard 1910.134(a)(2) A respirator shall be provided to each employee when such equipment is necessary to protect the health of such employee. The employer shall provide the respirators which are applicable and suitable for the purpose intended.
Before requiring respiratory protection, attempts should be made to control air contaminants in the workplace. Respirators are required when effective engineering controls are not feasible, while the engineering controls are in the process of being implemented, or if the controls do not fully protect the employees.
Respirators protect the user in two basic ways:
The first is by filtering the air of pollutants. Respirators of this type include particulate respirators, which filter out airborne particles, and air-purifying respirators that use cartridges or canisters which filter out chemicals and gases.
The second is by supplying clean air for breathing from another source. These kinds of respirators include airline respirators, which use compressed air from a remote source, and self-contained breathing apparatus (SCBA), that use a tank of compressed breathing air.
Some respirators use specialized cartridges and filters. Workers using these respirators should know how to identify the type of filters and how to install or replace them.
OSHA Standard 1910.134(d)(1)(i) The employer shall select and provide an appropriate respirator based on the respiratory hazard(s) to which the worker is exposed and workplace and user factors that affect respirator performance and reliability.
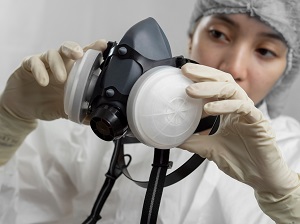
In general, respirators should be inspected for basic function prior to each use and cleaned as often as necessary to prevent the occurrence of unsanitary conditions. All respirators used in routine situations must be inspected before each use and during cleaning. All emergency-use respirators must be inspected at least once a month, but also checked for proper function before and after each use. Self-contained breathing apparatus must be inspected at least once a month.
Respirator inspections should include a check of respirator function, tightness of connections, facepiece, head straps, valves, connecting tube, cartridges, canisters or filters and any signs of malfunction or deterioration.
OSHA Standard 1910.134(h)(3)(i)(A) All respirators used in routine situations shall be inspected before each use and during cleaning.
Workers must keep respirators in a clean and sanitary condition. Respirators must be stored properly to avoid damage, contamination, dust, sunlight, extreme temperatures, excessive moisture, and damaging chemicals. Respirators should be packed or stored to prevent deforming the face piece and exhalation valve. If emergency respirators are required, they must be kept accessible to the work area and stored in compartments that are clearly marked.
OSHA Standard 1910.134(h)(1) Cleaning and disinfecting. The employer shall provide each respirator user with a respirator that is clean, sanitary, and in good working order.
All respirators that rely on a mask-to-face seal need to be annually checked with either qualitative or quantitative methods to determine whether the mask provides an acceptable fit to a wearer. Tight-fitting respirators should not be worn by employees who have facial hair or any condition that interferes with the face-to-facepiece seal or valve function.
Other PPE equipment that is required must be worn in such a manner that does not interfere with the seal of the facepiece to the face of the user. Respirators must not impair the worker’s ability to see, hear, communicate, and move as necessary to perform the job safely.
OSHA Standard 1910.134(g)(1)(ii) If an employee wears corrective glasses or goggles or other personal protective equipment, the employer shall ensure that such equipment is worn in a manner that does not interfere with the seal of the facepiece to the face of the user.
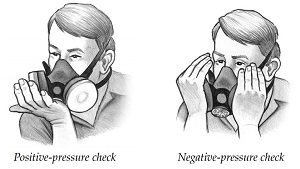
Employees must perform a user seal check each time they put on a tight-fitting respirator using one of the following methods, or the manufacturer’s recommended user seal check procedure.
Positive Pressure Check: Close off the exhalation valve and exhale gently into the facepiece. The face fit is considered satisfactory if a slight positive pressure can be built up inside the facepiece without any evidence of outward leakage of air at the seal. For most respirators, this method of leak testing requires the wearer to first remove the exhalation valve cover before closing off the exhalation valve and then carefully replacing it after the test.
Negative Pressure Check: Close off the inlet opening of the canister or cartridge(s) by covering with the palm of the hand(s) or by replacing the filter seal(s), inhale gently so that the facepiece collapses slightly, and hold the breath for ten seconds. If the facepiece remains in its slightly collapsed condition and no inward leakage of air is detected, the tightness of the respirator is considered satisfactory.
The design of the inlet opening of some cartridges cannot be effectively covered with the palm of the hand. The test can be performed by covering the inlet opening of the cartridge with a thin latex or nitrile glove.
During the safety meeting on respirators, emphasize these important points about respiratory protection.
- Respirators protect the user by either filtering contamination from the air or supplying clean air from another source.
- Workers should know how to identify the type of filters and how to install or replace these filters or cartridges.
- Respirators must be kept in a clean and sanitary condition.
- Respirators must be stored properly to avoid damage.
- Pack and store respirators safely to prevent deforming the facepiece and exhalation valve.
- Always use the proper respirator for the specific task and situation.
- Never use a respirator unless you have been properly authorized, fit-tested, and trained.
- Workers must know how to properly put on and wear their respirator.
OSHA Standard 1910.134(k) Training and information. This paragraph requires the employer to provide effective training to employees who are required to use respirators. The training must be comprehensive, understandable, and recur annually, and more often if necessary.
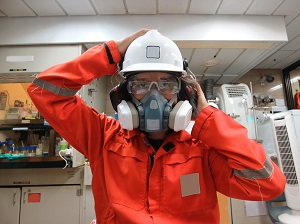