How do you start a safety program? How do you know if your safety program is good enough? Is a safety and health program ever finished? Learn more about how OSHA is helping companies like yours improve their safety program.
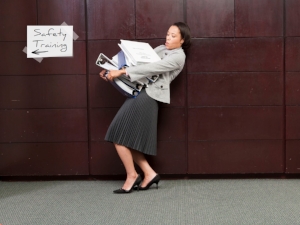
Each year, more than 4 million workers suffer serious job-related injuries or illnesses. These incidents don't just hurt workers and their families, but can hurt businesses in a variety of ways. Companies spend $1 billion per week on workers' compensation, which is money that could be better invested in growing small businesses, creating jobs, and keeping workers safe on the job.
Setting up a safety and health program can be overwhelming, especially for small businesses who may have an owner or a manager wearing many hats and responsible for so much more than just safety on the job. But safety should be a priority because by identifying and controlling the job-related hazards that lead to injuries and illnesses, these safety and health programs impact small- and medium-sized businesses' in three important ways:
- improve safety and health performance,
- save money through reduced accident costs and insurance premiums, and
- improve competitiveness in their industry.
More than 30 years ago, OSHA released the Guidelines for Safety and Health Programs document and just recently they have given the entire document an overhaul that takes into account all the changes workplaces have seen in the last three decades.
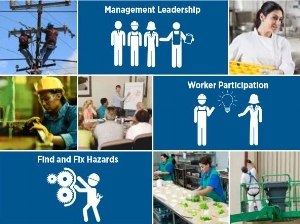
OSHA’s Recommended Practices for Safety and Health Programs is a 40-page document that anyone can download for free but OSHA has really made it as easy as possible by providing an interactive website to help guide employers and managers through the guidelines. In addition, all of the information is also provided in Spanish.
For companies in the Construction Industry, OSHA has taken it one step further by providing a specific guidelines document for construction that addresses the unique challenges of construction.
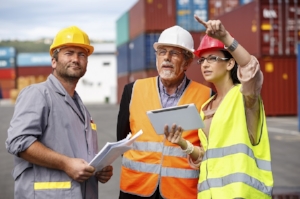
Establishing a safety and health program in your workplace is one of the most effective ways of protecting your most valuable asset: your workers. Losing workers to injury or illness, even for a short time, can cause significant disruption and cost—to you as well as the workers and their families. It can also damage workplace morale, productivity, turnover, and reputation.
The recommended guidelines for establishing and maintaining a safety and health program may be implemented in any workplace, but are particularly helpful for small and medium-sized workplaces. The guidelines are general enough that they can be applied in any workplace from manufacturing to healthcare or even an office-based work environment. There is also information specifically aimed at temporary worker and multi-employer work situations. A separate set of guidelines and recommended practices are available for the construction industry.
The concept of continuous improvement is central to the recommended practices. As with any journey, the first step is often the most challenging. The idea is to begin with a basic program and grow from there. By initially focusing on achieving modest goals, monitoring performance, and evaluating outcomes, you can help your workplace progress, over time, along the path to higher levels of safety and health.
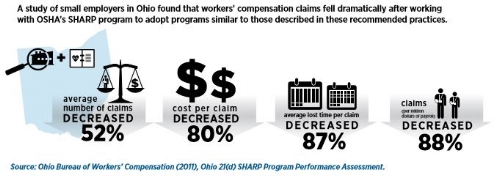
Each section of the recommended practices describes a core program element, followed by several action items. Each action item is an example of steps that employers and workers can take to establish, implement, maintain, and improve your safety and health program.
One size does not fit all! The process described in the recommended practices can, and should, be tailored to the needs of each workplace. Likewise, your safety and health program can and should evolve. Experimentation, evaluation, and program modification are all part of the process. You may also experience setbacks from time to time. What is important is that you learn from setbacks, remain committed to finding out what works best for you, and continue to try different approaches.
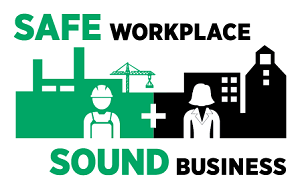
Injuries and illnesses occur in all types of workplace settings, from manufacturing sites, to hospitals and healthcare facilities, to offices, retail and service industries. Workers can even be injured or become ill outside physical facilities, such as when driving a vehicle as part of a sales or service job. The preventive approaches described in the recommended practices work equally well across all sectors of the economy; for all different kinds of hazards; in both mobile and fixed work environments; and for small, medium-sized, and large organizations.
Small employers may find that they can best accomplish the actions outlined in the recommended practices using procedures communicated through informal meetings such as monthly safety or weekly safety meetings, tailgate safety topics, or toolbox talks. Larger employers, who have more complex work processes and hazards, may require a more formal and detailed program that leverage safety meetings in addition to learning management programs. They may also wish to integrate their safety and health program with other programs that they are using to manage production, quality control, and environmental protection or sustainability.
Don’t forget, OSHA’s On-site Consultation Program offers free and confidential occupational safety and health services to small and medium-sized businesses in all 50 states. You will not be punished for using this service! The free consultation program will not result in penalties or citations.
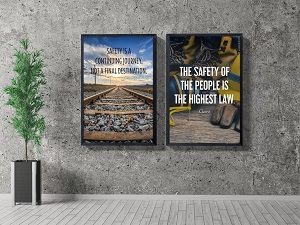