Lockout/tagout devices are an essential component of an organization’s safety program when the control of hazardous energy is required.
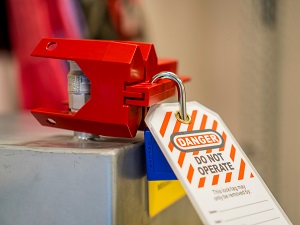
Lockout/Tagout (LOTO) devices can be installed on anything from machinery and electrical equipment to steering wheels and plumbing systems. These LOTO devices prevent unintended startups during maintenance, which can lead to injuries, or worse.
Lockout/tagout devices should be provided by the employer and they must be used only for LOTO operations and not for any other purposes.
OSHA Standard 1910.147(c)(5)(ii) Lockout devices and tagout devices shall be singularly identified, shall be the only devices used for controlling energy, and shall not be used for other purposes.
A lockout device uses a locking mechanism to hold an energy-isolating apparatus in such a way that prevents the energizing of a machine or equipment. A lockout device may include two parts, 1) a specifically designed cover which is the energy-isolating apparatus, and 2) a padlock to lock the cover in place.
A tagout device provides a prominent warning which can be securely fastened to the lockout device to indicate that the equipment serviced may not be operated until the tag and the lock are removed. Lockout tags are typically red, black, and white with bold black lettering and provide a space for a name and identifying information.
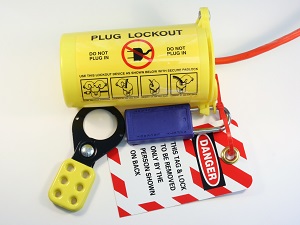
Lockout and tagout devices must be durable, standardized, substantial, and labeled.
OSHA Standard 1910.147(c)(5)(ii)(A)(1) Lockout and tagout devices shall be capable of withstanding the environment to which they are exposed for the maximum period of time that exposure is expected.
Lockout devices must be durable enough to withstand workplace conditions and tags must not deteriorate or become illegible even when used in a wet or corrosive environment.
Lockout devices must be standardized according to color, shape, or size. The print and format of tagout devices must be standardized, and tags must be legible and understandable by all employees.
Lockout devices must be substantial enough to ensure they cannot be accidentally removed. Tag attachments must be non-reusable, self-locking, and non-releasable, with a minimum unlocking strength of 50 pounds.
Lockout devices must be labeled to identify the specific employee authorized to apply and remove it. Tagout devices must warn employees with a clear instruction such as: Do Not Start, Do Not Open, Do Not Close, Do Not Energize, or Do Not Operate.
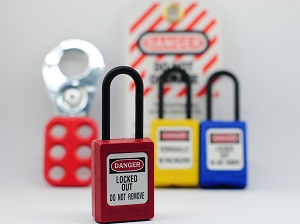
Lockout padlocks, that look like the traditional locks everyone is familiar with, are used to prevent the accidental removal of the lockout device. Each individual should have a unique key to their lock so it cannot be removed by someone else.
Lockout hasps are used when multiple people are servicing equipment at the same time. Each individual will place their lock onto the hasp and the equipment will remain locked out until the last one has removed their lock.
Lockout stations and kits provide a dedicated storage system to keep lockout/tagout equipment together and readily accessible. Lockout stations, which may sit on a counter or be wall-mounted, will include a selection of standardized lockout and tagout devices that can be retrieved from a permanent location. Lockout kits will be a portable bag or container that workers can carry around the worksite.
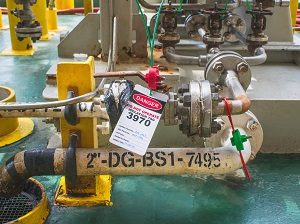
Electrical lockout devices are applied after the power is turned off and prevent equipment from being energized during maintenance. Circuit breaker lockouts keep breakers in the off position, electrical switch lockouts prevent a switch from being flipped on, and plug lockouts ensure a power cord won’t be inserted into an outlet.
Valve lockout devices are applied after the valve has been closed and prevent the valve from being opened while the pipe or equipment is being serviced. Cable lockouts are useful for locking multiple energy sources and can be flexed around difficult-to-lock devices, such as handles and gate valves. Other devices are specifically designed to lockout steering wheels, gas cylinders, pneumatic equipment, battery cables, push button controls, and more.
Group lockout boxes are used when multiple people are servicing equipment at the same time. One lock is placed at the lockout point and the key for that lock is placed in the lockout box. Then, each individual who needs to work on the equipment will add their personal padlock onto the box. The group lockout equipment will remain locked out until the last worker has removed their lock from the box and the key can be retrieved.
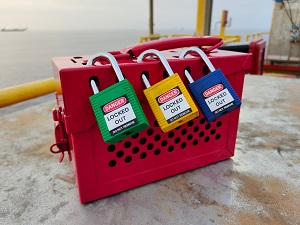
A tagout device provides a prominent warning that clearly states that the machinery being controlled must not be operated until the tag is removed. Tagout tags are attached to the padlock to indicate that the equipment is locked out and to identify the lock owner.
Tags must be attachable by hand, and the device for attaching the tag should be a one-piece nylon cable tie or its equivalent so it can withstand all environments and conditions. Tags do not provide the physical restraint of a lock and if used without a lock may give a false sense of security.
OSHA considers lockout devices to be more secure and more effective than tagout devices in protecting employees from hazardous energy.
If it is possible to lock out an energy-isolating device, a lockout device must be used. A tagout-only method can only be used only if the tagout procedure provides employees with a level of protection equal to that provided by a lockout device and that procedure has been documented.
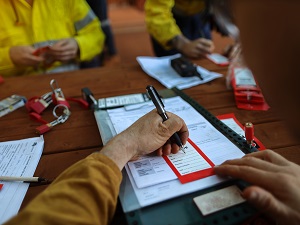