Roof repair projects require workers to complete jobs on existing buildings. These roofs are rarely designed with pre-existing fall protection safety so workers making the repairs must plan ahead and implement protection that will reduce their risk of dangerous falls.
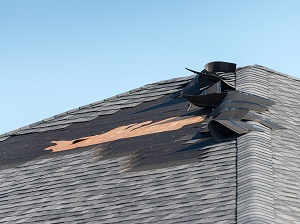
Working at heights is a hazard for any worker, but workers completing roof repairs may face additional risk if the roof is unstable, deteriorating, or if workers are uncertain how to use fall protection on a roof that is already weatherproofed.
There are several fall protection methods that workers can use during roof repair jobs to ensure the work proceeds safely. For repair jobs, roofers have several options including scaffolding, aerial lifts, and various types of conventional fall protection.
Before beginning the job, focus on identifying fall protection needs including precautions to prevent slip, trip, and falling object hazards. The best fall protection choice depends on the type of building and what area of the roof the worker needs to access to make the repair.
Guard against falls through skylights or other roof openings. Use a guardrail system, PFAS, or protective cover that will support two times the weight of a worker.
If necessary to protect workers below from falling debris, set up a work zone while roofers remove old roofing materials from the repair area.
Workers should be careful of air hoses and power cords for nail guns and other electrical equipment. If a worker steps on one, hoses and cords can slip underfoot and lead to falls.
Remember to place any removed shingles or replacement tiles in a safe location. If unsecured, these materials can visually blend in against the roof and create a dangerous trip hazard.
New materials staged on the roof should be placed so that they are safe and secure.
The structural integrity of the roof must be assessed before or during the roof repair process. If workers notice signs of deterioration on the roof, like dry rot, as old weatherproofing is removed, a competent person should evaluate the area and all necessary precautions must be taken to protect the roofers.
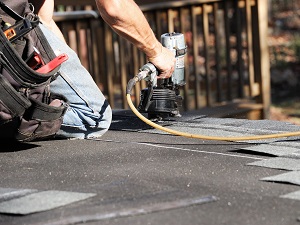
When repairs are to be completed along the edge of a roof, workers can use a scaffold or man lift. Regardless of the condition of the roof, scaffolds and lifts provide a safe, stable work platform.
For smaller tasks or shorter roof repair projects, scissor lifts or aerial lifts may be more efficient than installing scaffolds. Aerial lifts are a practical way to get to a customized height above or below the roof level. Do not overload the lift when loading material.
OSHA Standard 1926.453(b)(2)(iv) Employees shall always stand firmly on the floor of the basket and shall not sit or climb on the edge of the basket or use planks, ladders, or other devices for a work position.
When properly constructed and used, scaffolds can provide suitable fall protection for roof repairs. Guardrails installed along the open side of the scaffold provide fall protection.
Safe access must be provided because roofers also risk falling when climbing on or off a scaffold. Cross braces must not be used as a means of access for scaffolds.
OSHA Standard 1926.451(g)(1) Each employee on a scaffold more than 10 feet above a lower level shall be protected from falling to that lower level.
When scaffold platforms are 2 feet above or below a point of access, workers must use portable ladders, hook-on ladders, stair towers, ramps, or other safe means of access.
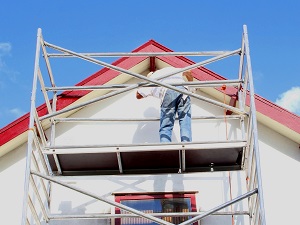
A Personal Fall Arrest System (PFAS) is usually the system of choice for most roofers. A PFAS will safely stop (arrest) a worker who is falling from a working level. It consists of an anchor point, a connector, and a body harness.
OSHA Standard 1926.502(d)(21) Personal fall arrest systems shall be inspected prior to each use for wear, damage and other deterioration, and defective components shall be removed from service.
When a personal fall arrest system is chosen as the means of fall protection on a job site, the PFAS must:
- Limit the maximum arresting force on a worker to 1,800 pounds when used with a body harness.
- Be rigged so that a worker can neither free fall more than 6 feet nor contact any lower level.
- Bring a worker to a complete stop and limit the maximum deceleration distance a worker travels to 3.5 feet.
- Have sufficient strength to withstand twice the potential impact energy of a worker free falling a distance of 6 feet or the free fall distance permitted by the system, whichever is less.
- Be inspected prior to each use for wear, damage, and other deterioration. Defective components must be removed from service.
- Workers must be trained in the safe use of the system.
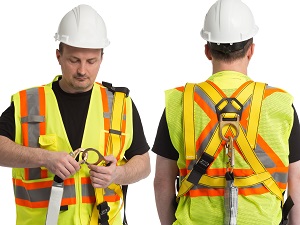
Selecting a location to install an anchor is a critical step in avoiding a fatal fall. An anchor gives the worker a secure point to tie off the lifeline for a fall arrest system. An anchor for a fall arrest system must meet the 5,000-pound strength requirement or maintain a safety factor of at least two (twice the impact load) under supervision of a qualified person.
When available, existing anchors might be effective points for a worker to tie off. From ground level inspect the ridge cap and last rows of shingles for permanently installed anchors. If present, these may be fastened to the top chord or other frame part during construction. Anchors could also have been installed with the original roof, using a low-profile style sometimes painted to match the roof color (making it less obvious from the ground).
If the roof doesn’t have permanent anchors, new anchors can be installed before repair work begins. If attaching a new anchor, roofers must fix it to the truss or rafter structure underneath. Roof sheathing does not provide enough support by itself. Always follow the anchor manufacturer’s installation instructions.
Depending on the size of the repair job and the number of workers who need to be on the roof, it might be necessary to install more than one anchor. Where practical, consider leaving roof anchors in place. It will make the current job simpler and reduce the burden for roofers in the future.
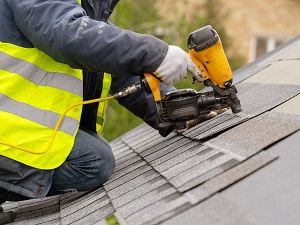
If the employer does not use ladders, scaffolds, or aerial lifts, and can demonstrate that it is not feasible or would create a greater hazard to use conventional fall protection equipment (guardrails, safety nets, or PFAS) when working at heights of 6 feet or greater, the employer must develop a written site-specific fall protection plan prepared by a qualified person. This person could be the owner, the supervisor, or a worker who has extensive knowledge, training and experience with fall protection and is able to solve problems relating to fall protection. States with OSHA-approved State Plans may have additional requirements for written fall protection plans.
OSHA Standard 1926.502(k)(1) The fall protection plan shall be prepared by a qualified person and developed specifically for the site where the leading edge work, precast concrete work, or residential construction work is being performed and the plan must be maintained up to date.
The site-specific fall protection plan must document at each location why the use of conventional fall protection equipment is not feasible or will create a greater hazard. The plan must also describe the alternative methods that the employer will use so that workers are protected from falls. Workers and their supervisors must be trained on the proper use of those other fall protection methods.
Conventional fall protection equipment can reduce or eliminate the chances of a fatal fall. Written site-specific fall protection plans ensure that protection continues, even when conventional fall protection methods are determined to not be feasible.
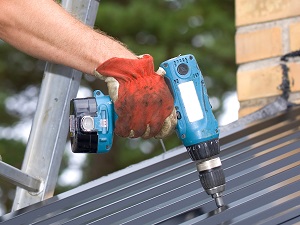