It’s up to everyone on the team to recognize the dangers of complacency and take action when we notice ourselves, or others, mentally checked out during routine tasks.
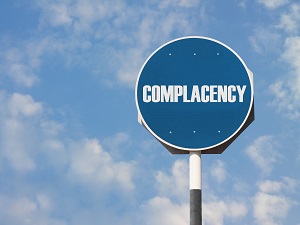
Complacency occurs when workers are unaware of the actual dangers on the job or feel like they are so familiar with the task at hand that there is no chance they can be hurt, even if they skip important safety steps.
Complacency can be and often is the cause of injuries and incidents on the job. Often, we don’t see how complacency has creeped into the workday until there is a near miss, or someone gets hurt.
Complacency on the job happens when workers:
- take potentially dangerous shortcuts
- don’t perform the same quality of work as they should
- become mentally distracted
- believe experience makes them invincible
- are bored or uninterested
- have a false sense of safety and security
- go into “autopilot” and stop paying attention to what they are actually doing
It’s often possible to become complacent at work, especially when we are performing the same tasks over and over.
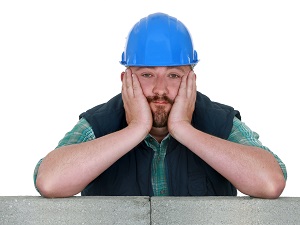
It’s important that workers and managers recognize the signs of complacency before they become dangerous missteps during the workday. Signs of complacency to watch for include:
- distractions, disengagement, or disinterest
- change in attitude
- carelessness, the tendency to take shortcuts
- frequent mistakes, close calls and near misses
- loss of initiative, neglecting tasks
- risky behavior, not wearing PPE
- negative safety culture
- lack of accountability, tardiness for meetings or shifts
Critical errors that can happen during moments of complacency:
- Eyes lose focus as movements go on autopilot
- Mind wanders off the task at hand
- Walking into “the line of fire”
- Close calls by equipment operators
- Loss of balance or grip
- Increased risk of caught-in, struck-by, and fall incidents
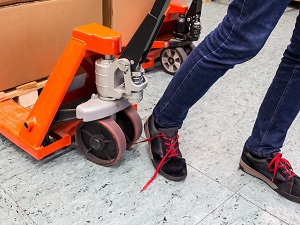
All workers can take responsibility to ensure complacency doesn’t become a dangerous problem on the job by 1) the actions they take at work, 2) their personal behavior, and 3) speaking up when needed.
Take hazards seriously. Understand the risks associated with the work activities you participate in and know the consequences of unsafe behavior.
Pay attention and participate in safety meetings. Listen to the material being presented, offer anecdotes and lessons you’ve learned along the way, and provide tips you find helpful that pertain to the safety topic.
Follow all safety policies and work procedures, even if they seem unnecessary or tedious. Do not rush through tasks, skip steps, or try to multitask.
Do not delegate work to someone else on the team who is not trained or qualified.
If a Job Hazard Analysis (JHA) or other pre-work hazard assessment is required, do not skip this step! Every project may have unique risks and it’s important to identify all the hazards before work begins.
Participate in the hazard reporting process. If you see a hazard you can correct immediately, fix it.
Don’t skip the inspections. If regular inspections are required on tools, equipment, or machinery, make sure to take your time and be thorough.
If there’s a checklist for a task, use it. If you would benefit from a checklist, create one or ask for one.
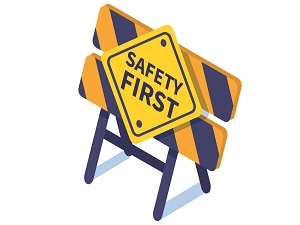
Think about the work tasks that you do every day and consider the safety precautions that you may skip because you are so confident you don’t need to follow all the rules. If you were training someone else, would you encourage them to skip steps too?
Practice self-awareness. If you feel complacency creeping in, consider doing a self-audit of the work process, taking it step by step, and checking along the way to make sure you are not missing any safety precautions.
Observe the way other workers incorporate safety into their work processes. By observing others, we can become more aware of our own habits and identify areas where we can improve.
Recognize when you may be rationalizing the ways it’s okay for you to cut corners and fight the urge to take the easy way out. Hold yourself accountable to following the safer process.
Make safety a habit. Instead of letting complacency take over, practice the safe way over and over until the safest process is the one you do every time.
Be a good example for your co-workers! If someone on the team is not following through on the safety aspects, then others assume it’s fine for them to skip those steps too.
If you notice that you are lost in thought during a task, take a moment and do what you need to do to shake yourself out of it.
“But I’ve always done it this way” is not an acceptable excuse for unsafe behavior!
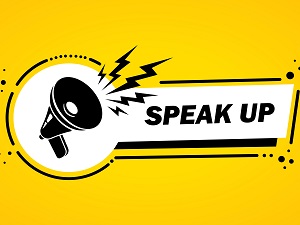
To ensure a successful safety culture, all workers must feel comfortable addressing safety issues on the job. If you have concerns regarding safety or complacency, talk to your supervisor, bring it up during a safety meeting, or correct the issue on the spot.
If you are resistant to following any safety procedure because you think it is unnecessary, instead of skipping that step, start a conversation about it. Bring it up to a supervisor or at the next safety meeting. Is there a way to streamline the process that is equally as safe?
If personnel safety is being compromised due production deadlines, lack of PPE, equipment malfunctions, missing safety signs, poor planning, broken tools, or unreasonable expectations, then make sure you bring up the issue so it can get corrected.
If you notice newer employees starting to take shortcuts, remind them not to skip the important safety steps in the process. Be firm, positive, and encouraging.
If the entire team seems to be going through the motions, bring your concerns to the supervisor and/or offer suggestions on how to boost morale.
Mention any ideas you have for the next safety meeting or toolbox talk.
If you are unsure of the correct and safe way to complete any task, ask.
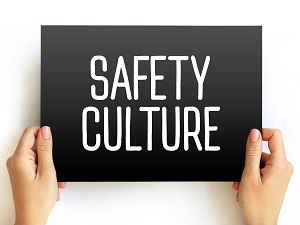