Working at height is always dangerous which makes it extremely important to provide a safe way for workers to access their job location. Using scaffolds to access hard-to-reach areas is often necessary for many construction activities. For especially difficult areas the safest approach may be to use a suspended scaffold.
According to OSHA, two-point adjustable suspension scaffolds, also known as swing-stage scaffolds, are perhaps the most common type of suspended scaffold. These types of scaffolds are usually hung by rope or cables connected to stirrups at each end of a platform and allow the workers to be raised and lowered to reach various work locations.
Most suspended scaffolds must meet basic OSHA regulatory requirements however, it is always important to follow the regulations for the specific type of suspended scaffold. In addition, workers must be trained and familiar with the precautions and manufacturer’s operating procedures for the specific model and brand of scaffolding systems they are using at their site.
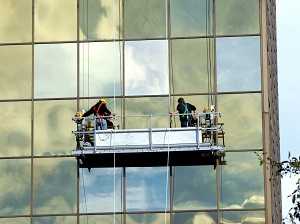
The first step to ensuring worker safety when using suspended scaffolds is to start with a sound and secure anchorage system. The anchorage is critical because it holds the weight of the workers, their tools, and supplies as well as the entire platform, the cables, and the hoists being used to operate the suspended scaffold. Workers must ensure that the surface or roof they use to anchor to is strong enough to support the suspended scaffold.
Suspension scaffold outrigger beams, cornice hooks, parapet clamps, and similar devices, must rest on surfaces capable of supporting at least 4 times the load imposed on them by the scaffold, operating at the rated load of the hoist. All components used as part of the scaffold must also be able to support the workers and scaffold itself. Suspension ropes, including connecting hardware, used on suspension scaffolds must be capable of supporting at least 6 times the maximum intended load applied.
OSHA Standard 1926.451(a)(4) Each suspension rope, including connecting hardware, used on adjustable suspension scaffolds shall be capable of supporting, without failure, at least 6 times the maximum intended load applied or transmitted to that rope with the scaffold operating at either the rated load of the hoist, or 2 (minimum) times the stall load of the hoist, whichever is greater.
Suspended scaffold outrigger beams must be stabilized to the supporting surface using counterweights or bolts or direct connections to the floor or deck. Counterweights must be secured by mechanical means to the outrigger beams to prevent accidental displacement.
Only items specifically designed as counterweights may be used to counterweight scaffold systems. Never use masonry units, rolls of roofing felt, and other similar construction materials as counterweights. Counterweights can not be made of flowable materials such as sand, gravel, and similar materials that can shift, move, or easily be dislocated.
OSHA Standard 1926.451(d)(2) Suspension scaffold outrigger beams, when used, shall be made of structural metal or equivalent strength material, and shall be restrained to prevent movement.
Never remove counterweights from an outrigger beam until the scaffold is disassembled. Outrigger beams that do not use counterweights must be installed and secured on the roof structure with devices specifically designed for that purpose.
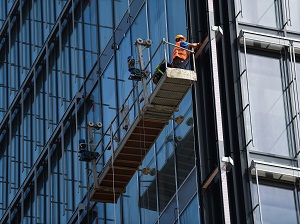
The platform is the work area of a suspended scaffold and must meet specific requirements for capacity, stability, and use to ensure the safety of all workers. The scaffold platform must support its own weight plus 4 times the maximum intended load. The maximum intended load includes the workers, tools, and supplies. Platforms must be at least 18 inches wide but no more than 36 inches wide. Workers must never stand on boxes, barrels, or other makeshift devices on top of scaffolds to get additional height.
Workers must never overload a scaffold with too many people, too much material, or stack too much in one area (known as point-loading). Manufacturer's requirements must be followed on the maximum number of occupants allowed on the suspended scaffold. Personnel on the scaffold must practice good housekeeping and avoid accumulating anything that could cause a slip, trip or fall such as loose tools, scrap materials, chemicals, snow or ice.
OSHA Standard 1926.451(f)(14) Makeshift devices, such as but not limited to boxes and barrels, shall not be used on top of scaffold platforms to increase the working level height of employees.
Suspended scaffolds must provide a safe and stable surface for workers to do their job safely. Extreme weather, excessive loads, or damage to structural components can all affect a scaffold's stability. In addition, workers need to be able to safely access their work area. Safe access must be provided to any scaffold that is 2 feet above or below an access point.
Suspension scaffolds must be tied (two-point or swing stage) or otherwise secured to prevent them from swaying, as determined to be necessary by a competent person. Never use window cleaners' anchors as a tie down for a suspension scaffold. Workers are not allowed to work from a scaffold during storms or high wind, unless a competent person has determined that it is safe.
OSHA Standard 1926.450(b) Competent person means one who is capable of identifying existing and predictable hazards in the surroundings or working conditions which are unsanitary, hazardous, or dangerous to employees, and who has authorization to take prompt corrective measures to eliminate them.
Any part of a scaffold that has been damaged or weakened must be immediately taken out of service and evaluated for repair or replacement in accordance with the manufacturer's requirements.
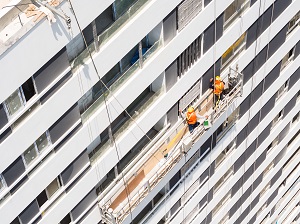
A tieback is a taut wire rope attached to a suitable anchor and is used to prevent temporary rigging devices from shifting or falling off the structure in an emergency. Inadequate counterweights, parapet failure, or even improper spacing of suspension ropes could lead to a serious event but having a properly installed tieback will prevent more serious damage or injury. Some describe the tieback as a lifeline for the support device.
Outrigger beams which are not stabilized by bolts or other direct connections to the floor or roof deck must be secured by tiebacks. Suspension scaffold support devices such as cornice hooks, roof hooks, roof irons, parapet clamps, or similar devices must be secured against movement by tiebacks.
Install tiebacks that are equal in strength to the suspension ropes and hoisting rope. Never anchor tiebacks to vents, electrical conduit, or standpipes and other piping systems. Set up and install tiebacks perpendicular to the face of the building or structure or at opposing angles. Never install a single tieback at an angle.
Since suspended scaffolds are usually held aloft by only suspension ropes, most would agree that the wire suspension ropes are the single most important component of the suspended scaffold. A failure of one or more suspension ropes is nothing less than catastrophic and often deadly.
Ropes must be inspected for defects by a competent person prior to each work shift and after every event that could affect the rope's integrity. Damaged wire rope may jam in a hoist and can create a hazard to workers.
Ropes must be replaced when any of the following exist:
- physical damage that could prevent proper function and strength of the rope
- kinks that could cause problems with the tracking or wrapping of the rope around the drum or sheave of the hoist
- loss of more than one-third of the original diameter of the outside wires due to abrasion, corrosion, scrubbing, flattening, or peening
- heat or electrical damage caused by a torch or any contact with electrical wires
- evidence that the secondary brake has been activated during an overspeed condition and has engaged the suspension rope
OSHA Standard 1926.451(d)(10) Ropes shall be inspected for defects by a competent person prior to each work shift and after every occurrence which could affect a rope's integrity.
Ensure that the load end of wire suspension ropes is equipped with proper-size thimbles and secured by eye-splicing or equivalent means. Never use a repaired wire rope as suspension rope. Joining wire suspension ropes is dangerous if not done properly. Only use wire ropes joined together with proper eye splice thimbles connected with shackles or coverplates and bolts.
Protect suspension ropes from heat-producing processes. When working with corrosive materials such as acids, caustics, or similar materials, shield suspension ropes or use treated wire ropes, that will not be damaged by the substances.
If wire rope clips are used on suspension scaffolds, there must be a minimum of three clips installed. All clips, shackles, and other devices used with wire rope must be installed according to manufacturer’s recommendations.
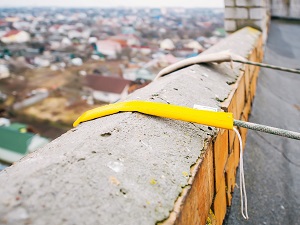
Scaffold hoists are a critically important component of the suspended scaffold because they help adjust the height of the platform, allowing the operators to get to their work. Hoists are intended to safely lift the platform if they are used according to manufacturer’s specifications. Never allow the stall load of any scaffold hoist to exceed 3 times the rated load as provided by the manufacturer for the specific device used.
When winding drum hoists are used and the scaffold is extended to its lowest point of travel, there must be enough rope to still wrap four times around the drum. When using other types of hoists, the suspension ropes must be long enough to allow the scaffold to travel to the level below without the rope end passing through the hoist, or else provide a way to prevent the end from passing through the hoist.
Never allow gasoline-powered hoists to be used on suspension scaffolds. Gears and brakes of power-operated hoists used on suspension scaffolds must be guarded and enclosed. Power-operated and manual hoists must have an automatic braking device to safely support, decelerate and stop a load during a fall.
OSHA Standard 1926.451(d)(13) Suspension scaffold power-operated hoists and manual hoists shall be tested by a qualified testing laboratory.
Falls are one of the most common dangers that workers are exposed to on the job site. However, falls involving suspended scaffolds are even more dangerous because the extreme heights that can be involved with the work. Workers on suspended scaffolds could be exposed to falls from potentially hundreds of feet high.
OSHA requires workers on scaffolds more than 10 feet above a lower level be protected from falling to that lower level. When workers are using a two-point adjustable suspension scaffold they must be protected by both a guardrail system and a personal fall arrest system.
OSHA Standard 1926.451(g)(1)(ii) Each employee on a single-point or two-point adjustable suspension scaffold shall be protected by both a personal fall arrest system and guardrail system.
The first step to ensuring workers are protected from falls from suspended scaffolds is to make certain that all suspended scaffolds are equipped with a sturdy and properly constructed guardrail. Although most suspended scaffolds come pre-built with guardrails workers should be aware the requirements of guardrails.
Guardrails must be installed on all open sides and on the ends of suspended scaffold platforms. A proper guardrail consists of a top rail, mid rail, and toe board and must meet these strength requirements applied in any downward or horizontal direction:
- Each top rail must withstand a force of at least 200 pounds.
- Mid rails, screens, mesh, intermediate vertical members, solid panels, etc., must withstand a force of at least 150 pounds.
- Toe boards must withstand a force of at least 50 pounds.
If screens, mesh, or solid panels are used, they must extend from the top edge of the guardrail system to the scaffold platform, and along the entire opening between the supports. The top edge height of top rails on suspended scaffolds must be between 36 inches and 45 inches.
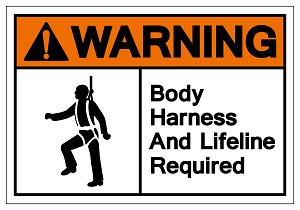
All workers on or near the supported scaffold must wear hard hats! Additional protection from falling hand tools, debris, and other small objects must be provided.
OSHA Standard 1926.451(h)(1) In addition to wearing hardhats each employee on a scaffold shall be provided with additional protection from falling hand tools, debris, and other small objects.
Toe boards are used for falling object protection and must be at least 3½ inches high from the top edge to the level of the walking/working surface. Where tools, materials, or equipment are piled to a height higher than the top edge of the toe board, paneling or screening extending from the toe board or platform to the top of the guardrail must be constructed for a distance sufficient to protect employees below.
In some instances, the construction of debris nets, catch platforms, or canopy structures may be needed to contain or deflect potential falling objects. The area below the scaffold to which objects can fall may need to be barricaded to prevent workers and pedestrians from entering a hazardous area. If falling objects are too large or heavy to be contained or deflected, then those items must be secured and placed away from the edge.
Personal fall-arrest systems (PFAS) used on scaffolds are to be attached by lanyard to a vertical lifeline. Each worker must be attached to a separate lifeline. Never connect two or more vertical lifelines together or to the same anchorage point. Vertical lifelines cannot be used on two-point adjustable suspension scaffolds with overhead components such as multiple platforms.
Vertical lifelines must be fastened to a fixed safe point of anchorage, independent of the scaffold. Lifelines must be protected from sharp edges, cuts, abrasion, or other potential damage. Safe anchorage may include structural members of buildings. Workers must never anchor to standpipes, vents, electrical conduit, or similar components that could break under the force of a fall.
OSHA Standard 1926.451(d)(10) Ropes shall be inspected for defects by a competent person prior to each workshift and after every occurrence which could affect a rope's integrity.
Personal fall arrest systems (PFAS) used by workers on suspended scaffolds must not only be installed correctly but the workers must know how to use, maintain, and properly wear the systems.
Inspect PFAS prior to each use for wear, damage and other deterioration. Remove any defective components from service immediately. Only use PFAS equipment as intended – for worker protection! Never use body belts, harnesses, lanyards or other components to hoist materials.
Wear harnesses properly! The attachment point of the body harness should be located in the center of the wearer's back near shoulder level or as described by manufacturer’s instructions.
Each worker who might be exposed to fall hazards should have training in the procedures to be followed in order to minimize these hazards.
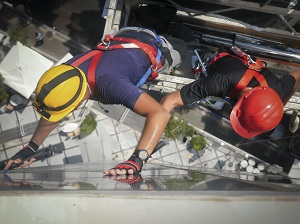