Because stationary masonry saws can cut a wide variety of tough materials like stone, granite, concrete and brick, and can cut through these harder materials more effectively, they are useful tools to have on the job site. These powerful tools can be dangerous if safety precautions are not taken seriously.
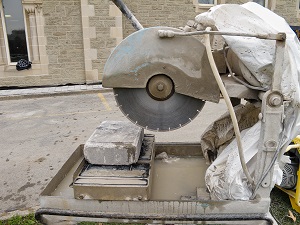
Anyone operating a stationary masonry saw on site must be trained and authorized before use.
Always wear proper PPE when operating any stationary masonry saw, including eye protection, like safety glasses, heavy duty gloves, and hearing protection. A hard hat, work apron, safety footwear, and respiratory protection may also be recommended.
The major safety risks to be aware of when operating a stationary masonry saw include:
- electrocution
- flying particles
- abrasions and lacerations
- amputations
- respiratory hazards
OSHA Standard 1926.702(i)(1) Masonry saw shall be guarded with a semicircular enclosure over the blade.
When working with stationary masonry saws, much of the danger occurs at the point of operation, where the work is performed and where the machine cuts.
Position the saw on a firm, flat area. Ensure the saw will not move at all while in use. Ensure the area around the saw is clear, with no nearby slip or trip hazards. While using the saw, the operator must be able to maintain a firm, stable footing. Inspect the saw blade before use to be sure it is in good condition and does not show excessive wear.
The conveyor cart should be kept free of debris and grit to ensure that the material does not unexpectedly slide during cutting operations. Keep fingers and hands out of the path of the blade.
Using a stationary masonry saw to cut bricks, concrete blocks, pavers, or other silica-containing materials can generate respirable crystalline silica dust. When using a stationary masonry saw, wet cutting with an integrated water delivery system that continuously feeds water to the blade is an effective way to reduce exposure to silica dust. Many stationary masonry saws come equipped with a water basin that holds several gallons of water. A pump recirculates the water through a nozzle that directs a continuous stream onto the blade where it wets the material being cut and reduces the amount of dust generated.
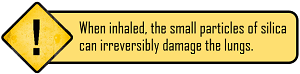
The stationary masonry saw, and the saw’s dust-control equipment, must be operated and maintained in accordance with manufacturer’s instructions to minimize dust emissions.
- Check that hoses are securely connected and are not cracked or broken.
- Ensure that water flows at the rates recommended by the manufacturer.
- Water flow rates must be sufficient to minimize the release of visible dust.
- Adjust nozzles so that water goes to the blade and wets the cutting area.
- Replace basin water when it gets gritty or begins to silt up with dust.
- Rinse or replace water filters at recommended intervals.
OSHA Standard 1926.1153(c)(2)(i) For tasks performed indoors or in enclosed areas, the employer shall provide a means of exhaust as needed to minimize the accumulation of visible airborne dust.
Where water is used to control dust, electrical safety is a particular concern. Use ground-fault circuit interrupters (GFCIs) and watertight, sealable electrical connectors for electric tools and equipment.
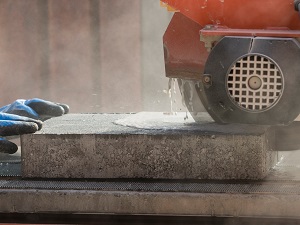
When properly used, wet cutting methods can effectively control silica dust and additional respiratory protection is not required. Wet cutting indoors or in enclosed areas may not reliably keep silica exposures low, so extra ventilation or a means of exhaust may be needed to reduce visible airborne dust.
Some stationary masonry saws come equipped with a Vacuum Dust Collection System (VDCS) to capture the dust generated when sawing. When VDCS is being used as the dust control method (dry cutting), respiratory protection will be required if the employee exposure is found to be above the permissible exposure limit.
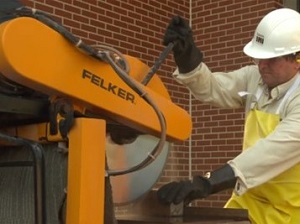