Guest Article written by Kristin Savage
Safety in the workplace has become a complex and ever more critical concern. COVID is just the latest among many factors that have come to impact how companies design, develop, and implement safety policies. And once those policies are in place, there is critical employee training – retraining existing employees and fully training all new employees from the ground up.
Adding to this complexity is the need to separate out the type of training for different segments of employees. Office staff, for example, will need very specific types of training; workers on the manufacturing floor or in the warehouse will need customized training related to their workplace environments.
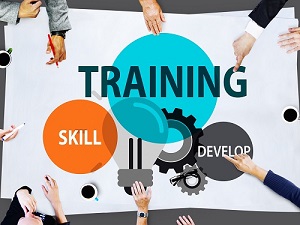
General and Overall Safety Training Needs for All Employees
There are some OSHA regulations that relate to all workplace environments.
- Air Quality: This can be an issue in an office or on the warehouse/manufacturing floor. OSHA looks at several factors that impact air quality – ventilation, circulation, temperature, and humidity. Buildings must provide appropriate ventilation. OSHA does not have specific standards, which is not ideal. Rather, it simply states that employers must provide a safe workplace with proper air quality. Some states have gone beyond this and do have strict standards, which are inspected and evaluated.
- Hazardous Materials: Workplaces that do have hazardous materials on site must have a written plan for their storage and disposal, and that plan must be made available to OSHA. Employees in the presence of hazardous materials must receive appropriate training in the handling of hazardous materials according to that written plan. Warehouses hold hazardous materials until they are shipped to purchasers; factory floors have hazardous materials for operation and cleaning of machinery; even office spaces do have hazardous materials – cleaning and copier supplies, for example.
- Fire Hazards: Hazardous chemicals are not the only fire hazard in the workplace. Consider just the presence of large amounts of dust, a potentially explosive situation. OSHA does have regulations regarding such things as fire drills, fire-fighting equipment, and alarm/sprinkler systems and does inspect companies for compliance. Even outside construction sites have fire hazards. Part of that compliance investigation will include a company’s training plan for its employees to both prevent and deal with fire hazards.
- Injuries: This is a huge category, and training must be separated out based upon the specific workplace environment. The types of injuries that are common for construction workers, for example, are not the same as for warehouse workers, machine operators on a factory floor, or office workers. Safety training must be divided into categories based upon the specific positions of employees. Every company must develop safety plans to prevent injuries – everything from slips and falls in the office to the dangers of operating machinery, operating forklifts in warehouses, to injuries resulting from lifting heavy objects, to muscle and tendon issues of office workers at computer stations. Training and development departments must develop training programs for each category of worker they have, taking into account the OSHA regulations for each environment. Some OSHA content has specific prevention requirements; other content consists of suggestions. Training providers within a company need to design their programs based upon both requirements and suggestions.
- Fatigue: OSHA stipulates those conditions under which fatigue results – strenuous working conditions, irregular and constantly shifting work hours, longer-than-normal work hours. While labor laws address these relative to increased pay, the safety concerns related to fatigue. Fatigue contributes to safety issues, and OSHA does provide links to guidance that address the prevention of worker fatigue. While employers must comply with OSHA and other federal agency requirements (transportation, labor, etc.), the demands for training are not as rigorous. Still, employees need to understand the regulations so they know when they are being violated.
- Structural Integrity: While this has not been a frequent concern for OSHA, it does nevertheless perform inspections on structural soundness, especially in old buildings. Employee training in this facet of health and safety should not be complicated. Employees need to understand that they must report any issues they observe regarding structural integrity. Such training might include visuals of structural issues of which they should be aware.
- Newer COVID Compliance: This is such a new area that OSHA is still in the midst of collaborating with other health agencies to establish guidelines for employers. In this area, business leaders must look to local and state regulations first and ensure that immediate training sessions are put into place to provide for an optimal work environment that will protect their employees. This training might include mask requirements, social distancing, restroom cleanliness/sanitation, and a testing protocol. Part of this training must include segments specifically geared to custodial staff.
- Lighting: Employers need to be fully apprised of the numerous requirements for lighting in all areas of workplaces. These include such things as the amount of lighting as well as the wiring and safe electrical current specifications. Employees in all workplace areas should be trained to look for potential electricity issues regarding lighting and wiring so that these may be reported for immediate correction.
Design and Development of Employee Training Programs
These eight areas are only the most critical identified by OSHA. Each organization is unique and must assess health and safety needs accordingly.
The challenge for training and development departments, usually arms of HR, is to analyze each of the individual work environments and identify which of the OSHA regulations and recommendations apply to them. Once that is accomplished, customized training can be designed for employees in those environments. How that training is delivered poses many options, and new technology allows for employees to complete modules and assessments electronically.
No matter how the training is delivered, there should be health and safety policy manuals distributed to each employee – manuals the sign for – so that there is documentation should OSHA ever ask. And, as reminders for the most important aspects, there should be posters – lots of them.
Additional Important Wrap-Up News
In 2020, OSHA announced that it will be adding a new targeting category for organizations that have consistent increases in illness or injury rates over a three-year period, based upon their required reporting. This applies to non-construction entities with over 20 employees and will involve on-site inspections. OSHA has other targeting programs, and companies would do well to see if they might fall into any of these categories.
Training has always been an important facet of both onboarding and other regular updates and/or new learning. Health and safety training should always be included on a regularly scheduled basis or when there are new additions to a work environment or new events/situations, such as the current COVID crisis. Employers must keep apprised of additions or modifications to OSHA requirements as well so that they do not risk non-compliance.